After austenitizing treatment and isothermal transformation, the microstructure of ductile iron has changed obviously. Figure 1 shows the microstructure of Austempered Ductile Iron with different as cast microstructure (MS = 0.25cm, Ms = 0.50cm, Ms = 0.75cm, Ms = 1.00cm and Ms = 1.25cm) after being treated at 920 ℃ / 2H + 280 ℃ / 1.5h, respectively. The matrix structure is graphite ball + austenite, and the microstructure of austenite is relatively small. The picture shows the SEM image of matrix structure of Austempered Ductile Iron with different as cast microstructure.
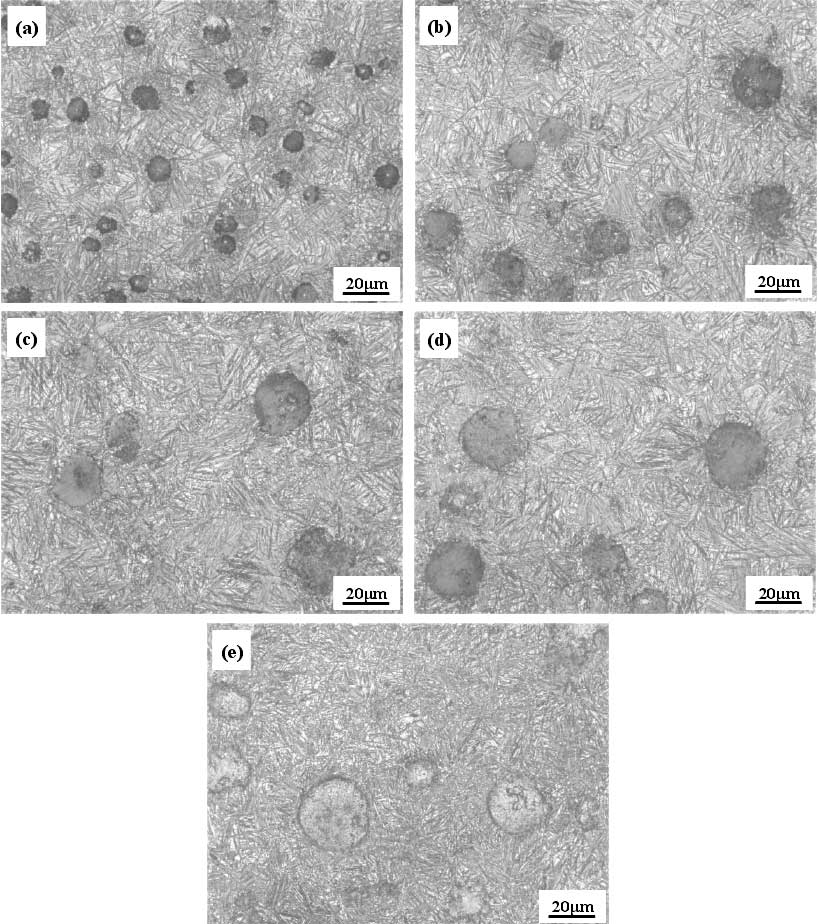
It can be seen from Fig. 2 that the austempered ductile iron matrix of MS = 0.25cm ductile iron is the shortest, the isothermally quenched ductile iron with MS = 0.50cm is the second, and the austempered ductile iron with MS = 0.75cm, Ms = 1.00cm and Ms = 1.25cm is longer. The smaller the grain size of high temperature austenite, the shorter the acicular ferrite after isothermal transformation.
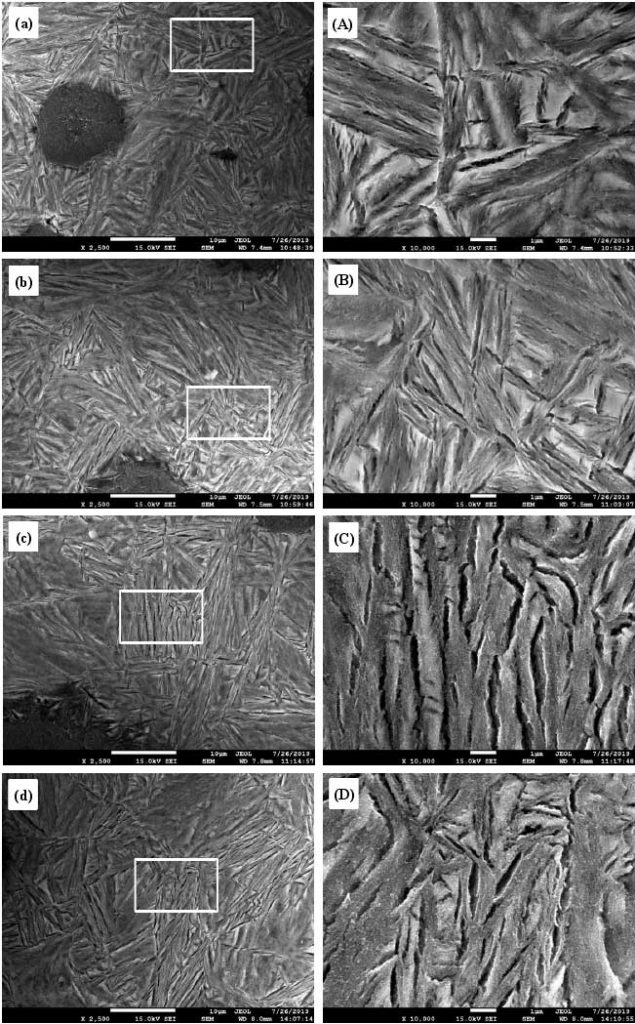
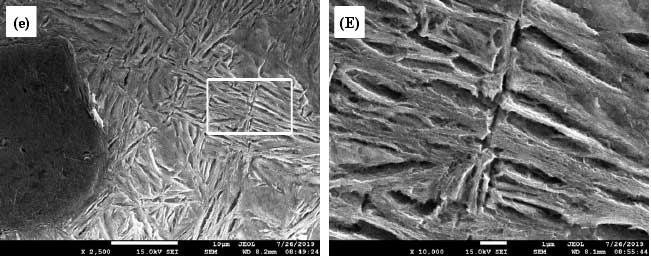
On the one hand, it is shown that the nucleation of austenite in the process of austenite nucleation also needs some structural fluctuation, energy fluctuation and concentration fluctuation as well as that of liquid crystal nucleation. At the same time, the atoms on the phase interface are in a high energy state due to their scattered arrangement, which is prone to structural fluctuations and energy fluctuations. Because the carbon concentration of austenite is between ferrite and cementite, it is easy to have concentration fluctuations at the interface of these two phases. Therefore, when the heating rate is not too fast, austenite always begins to nucleate at the interface of α – Fe / Fe3C, and then begins to grow, until the γ – Fe grains meet each other, it will not grow any more.
On the other hand, there are a large number of α – Fe / Fe3C interfaces in pearlite, and pearlite accounts for 73.7%, 22.6%, 7.4%, 6.6% and 6.0% of as cast ductile iron with MS = 0.25 cm, Ms = 0.50 cm, Ms = 0.75 cm, Ms = 1.00 cm and Ms = 1.25 cm, respectively. Therefore, in the as cast structure of MS = 0.25cm ductile iron, the nucleation interface of austenite is large enough, the amount and size of high temperature austenite grains obtained after austenitizing are the largest and the smallest, followed by Ms = 0.50cm ductile iron, while the as cast structure of MS = 0.75cm, Ms = 1.00cm and Ms = 1.25cm nodular iron has less and larger austenite grains after austenitizing.