During the cooling and solidification process of cylinder liner, the cooling water from the outer wall metal mold and impacting on the metal mold have a great impact on its solidification process. The difference of local cooling intensity will affect the solidification characteristics of various parts of cylinder liner, which will lead to the difference of organization and hardness at different positions of cylinder liner. Based on this view, the research team conducted a test on the influence of different cooling and solidification conditions on casting black spot defects, and the test results are shown in the table.
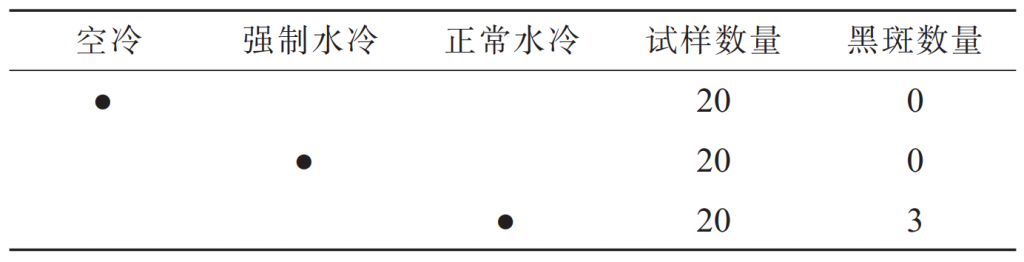
② Forced water cooling: it refers to flushing and cooling the outer wall of cylinder liner mould immediately after pouring, with a water supply time of 45 s, and forcibly shortening the cooling and solidification time of cylinder liner.
③ Normal water cooling: according to the requirements of normal production process, after pouring, the water is delayed for 20 s to cool the mold, and the water supply time is 35 s.
It can be seen from the table that neither air cooling nor forced water cooling produced casting black spot defects; On the contrary, 15% of the cylinder liners produced by normal water cooling process have casting black spot defects. This result is consistent with the actual production. In the actual production, all cylinder liners adopt the mode of delayed drainage cooling and solidification. The cooling rate of air cooling is very slow, the molten iron is in the molten state for a long time, and the specific gravity segregation is more thorough in the solidification process; In the same diameter direction, the microstructure uniformity is better, and the casting black spot defect is not easy to occur.
When forced water cooling is adopted, the temperature of molten iron is forced to reach near the solidus in a very short time, the specific gravity segregation has not occurred, the molten iron has lost fluidity, and the casting black spot defect is not easy to occur. When the normal cooling solidification process is adopted, there is a certain delayed cooling time, which gives the necessary conditions for the occurrence of specific gravity segregation; However, this time is short, the specific gravity segregation cannot be fully carried out, and then the water is discharged for cooling and solidification. The temperature of the molten iron quickly drops near the solidus and loses fluidity, and the specific gravity segregation in the molten iron is solidified; This radial specific gravity segregation is disordered, which directly affects the crystallization of microstructure in the subsequent solidification process, resulting in serious microstructure segregation. Therefore, the difference of cooling and solidification conditions has a direct impact on the casting black spot defect.