Inoculant is added during the post-treatment of molten iron furnace, and the melting point of inoculant is generally 1300 ~ 1400 ℃. When the temperature of molten iron is low, the inoculant cannot melt and diffuse well in the molten iron, and the local inoculant concentration is too high, resulting in differences in the inoculation effect of various parts of molten iron during solidification and crystallization, resulting in differences in the morphology and structure of graphite at various parts, which may lead to the occurrence of black spots. Therefore, add inoculant with the same particle size to pour the cylinder liner at high temperature and low temperature respectively, and test run the samples. The test data of inoculant as shown in Table 1 are obtained.
It can be seen from table 2 that casting black spot defects will appear when No. 1 inoculant is used at low temperature. The targeted low-temperature inoculant test was continued to lower the pouring temperature and increase the particle size of inoculant, resulting in the state that the inoculant cannot be fully melted. The test results are shown in Table 3.
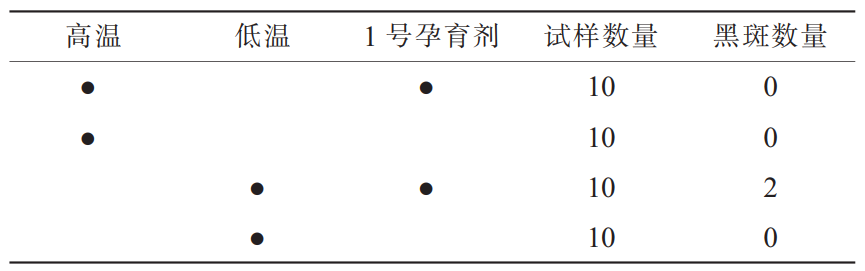
② No. 1 inoculant: 75sife, particle size 1 ~ 2 mm.
In the above test, No. 2 inoculant (75sife, 5-8 mm) with large particle size was added in the semi solidified state of molten iron. During the test, it is obvious that the inoculant can not be completely melted in the molten iron, and part of the inoculant is still adhered to the ladle. From the test data, the samples produced in this state do not have casting black spot defects. The test shows that the incomplete melting of inoculant when the temperature of molten iron is low and the high local Si element in molten iron are not the inevitable factors causing casting black spot defects.