In this experiment, the method of controlling variables is adopted. The mold temperature is set as 230 ° C, 140 ° C and 50 ° C respectively under the condition of other parameters unchanged. Through the measurement of actual mold temperature, the temperature at the bottom of the moving mold is higher than that at the top under three different setting conditions, and the temperature distribution of the fixed mold is uniform. This phenomenon conforms to the principle of “sequential solidification” The actual mold temperature measurement diagram is shown in Fig. 1.
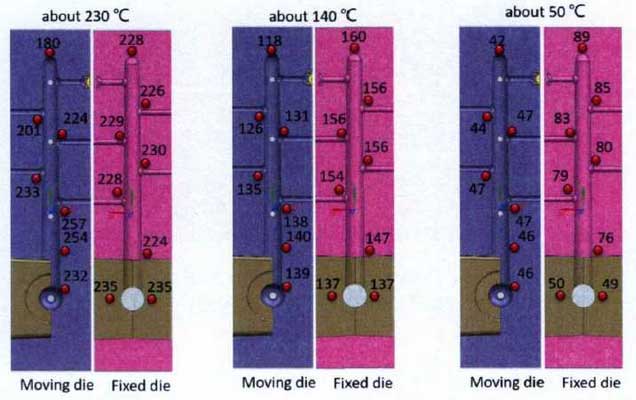
According to the sample preparation and detection methods mentioned above, the semi-solid die casting samples were analyzed by sawing, polishing, fluorescence detection and metallographic observation. The effect of die temperature on shrinkage cavity and porosity is shown in Fig. 2. Fig. 3 shows the metallographic photos of typical positions at 230 ° C and 50 ° C mold temperature.

It can be seen from Fig. 2 that when the mold temperature is low (50 ° C), there are significant shrinkage and porosity defects in the middle and upper parts of the sample, which show bright spots and aggregation spots under fluorescence, and black holes in the metallographic photos (Fig. 3b); when the mold temperature is increased (140 ° C), it can be seen that 140 ° C is compared with 50 ° C under fluorescence observation When the mold temperature increased to 230 ° C, there were no bright spots or aggregation spots in the whole area of the sample under fluorescence observation Under microscopic observation, the black holes also disappear completely (Fig. 3C, d), which means that the shrinkage cavity and porosity defects have been completely eliminated. After actual production verification, when the mold temperature rises to 230 ° C, the cylindrical sample without shrinkage cavity and porosity can be produced stably.
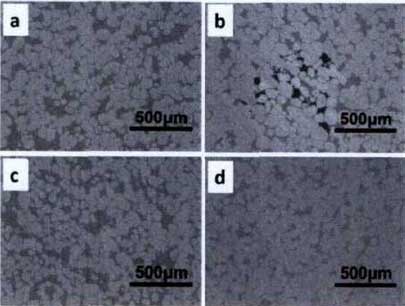
According to the analysis and discussion of this phenomenon, it is considered that the effect of mold temperature on shrinkage cavity and porosity mainly lies in the filling process of slurry and the feeding process after filling.
(1) Analysis of slurry filling process
When the mold temperature is low, the slurry contacts with the mold surface during the filling process. Because the mold temperature is low, the supercooling degree is large, and the cooling rate is fast. This will lead to that the top area of the sample is nearly solidified or completely solidified before the filling stage is completed, which leads to the difficulty of pressurization and the formation of shrinkage cavity and porosity. When the mold temperature increases, the undercooling degree of slurry is small and the cooling rate is slow. Before the filling stage is completed, the top area of the sample is still semi-solid or nearly semi-solid, which makes the subsequent feeding process more smooth, so as to reduce or even completely eliminate shrinkage porosity defects.
(2) Analysis of feeding process
When the mold temperature is low, the slurry cooling speed is faster in the feeding process, which leads to the short time of feeding channel and the difficulty of feeding, and finally leads to shrinkage cavity and porosity. When the mold temperature is high, the slurry cooling rate is slow in the feeding process, the feeding channel exists for a long time, and the feeding is sufficient, so as to reduce or even completely eliminate the shrinkage cavity and porosity.