Semi solid die casting is different from the traditional liquid die casting, which is mainly reflected in the different slurry characteristics used in the process of die casting. Due to the viscosity characteristics of slurry, it is not easy to produce flow defects such as flying material and air entrainment in the flow front during the filling process. However, in the actual industrial production, we found that the defects of shrinkage cavity and porosity are easy to appear in the semi-solid die-casting production of thick wall products, and the production of the defects is closely related to such factors as the pressurization pressure mold temperature.
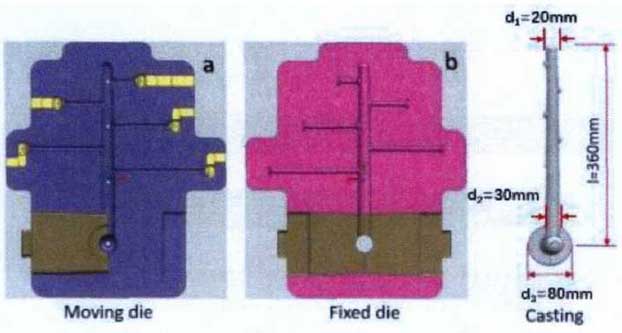
Therefore, the influence of three common process parameters on shrinkage cavity and porosity in die casting production was studied. The alloy used in the experiment was A357 aluminum alloy. The aluminum alloy melt was placed at 630 ° C and poured into a crucible. The semi-solid slurry was obtained by shaking at 180 rpm and moving to 590 ° C. finally, the die was cast. The experimental mold was a cylindrical mold, as shown in Figure 1 The final product produced by the mold is a nearly columnar sample with a length of 360mm. The sample belongs to a thick wall product, and the thickest part is about 30mm. Through simulation analysis, it can be concluded that the mold design conforms to the principle of “sequential solidification”, as shown in Fig. 2.
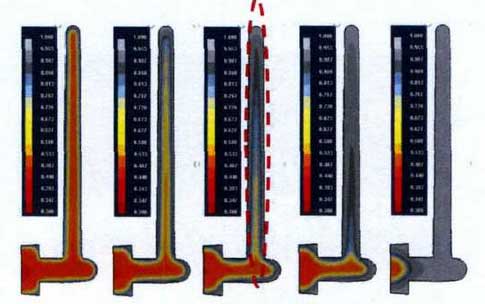