Y-shaped samples were used. The burden ratio was 85% of cast pig iron and 15% of Q235 steel. The addition of inoculant and vermicularizing agent were 0.4% and 0.5% of the burden mass fraction respectively. The inoculation and vermicularizing treatment were carried out in the ladle. The treatment temperatures of molten iron were 1510 ° C and 1560 ° C respectively. The effect of molten iron treatment temperature on the microstructure of vermicular graphite cast iron was studied.
Figure 1 shows the graphite morphology of vermicular graphite cast iron obtained at two liquid iron treatment temperatures.
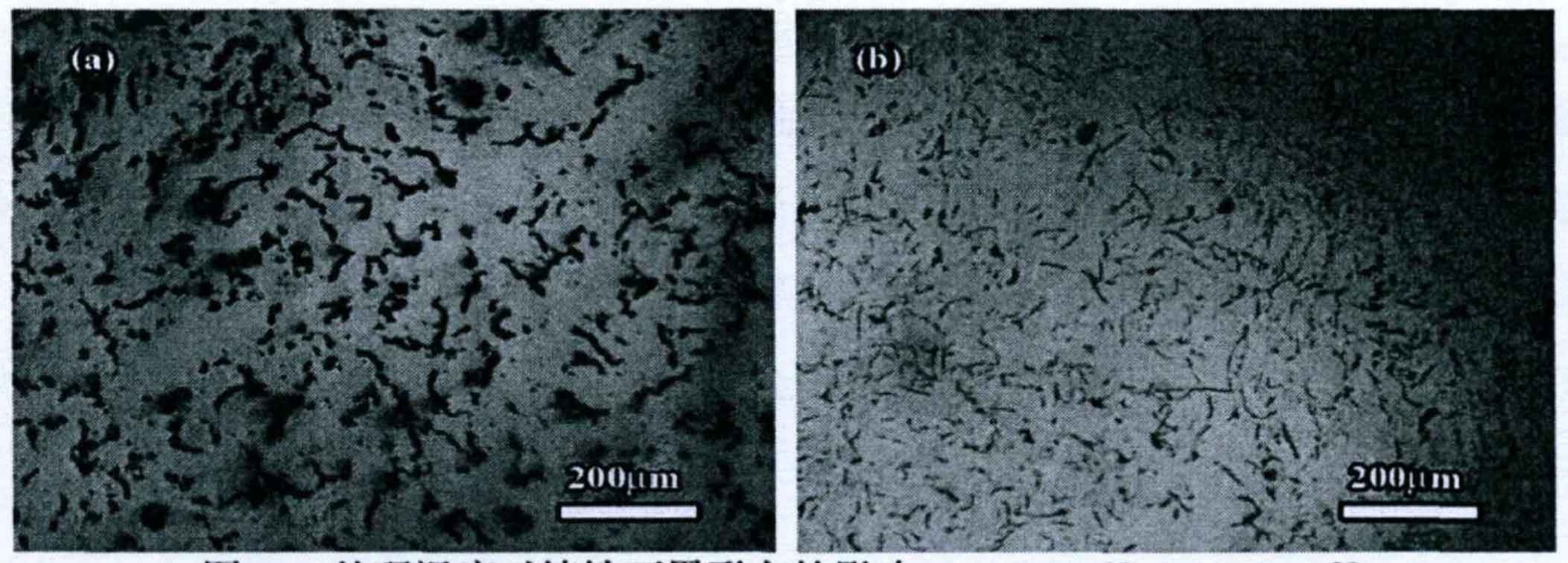
It can be seen from Figure 1 that the cast iron alloy prepared at 1510 ° C of molten iron treatment temperature is vermicular cast iron, and the graphite in the structure contains vermicular and spherical graphite; However, the vermicular graphite in the cast iron alloy prepared at the molten iron treatment temperature of 1560 ° C became thinner and shorter, and the vermicular graphite changed to flake graphite. In general, the graphite has a small adhesion on the (1010) edge, that is, the thickening of the flake is slow. However, there is always a covalent bond on the (0001) edge that is not bonded, so the carbon atoms are easy to enter and firmly bond with it, and continue to grow in flakes. However, the growth of graphite in molten metal is not stable. It is not only affected by the cold degree, but also by the composition of molten metal and other additional elements. When the vermicularizing agent is added, the rare earth elements and residual magnesium elements in the vermicularizing agent are easy to be adsorbed on the (0001) edge surface, which hinders the thickening of the flake graphite and the continuous combination of the unbound covalent bond in the graphite with the carbon atoms, becoming a barrier for the diffusion of the carbon atoms to the edge of the graphite, inhibiting the growth of the graphite and refining the graphite. When the treatment temperature of molten iron is high, the heat released in the solidification process is increased, the magnesium and rare earth elements in the vermicularizing agent are burned seriously, the adsorption on the graphite crystal edge is reduced, the diffusion speed of carbon atoms along a direction is increased, and the growth speed of graphite to C is reduced. Therefore, the morphology of graphite changes from vermicular to A-type flake graphite.
In addition, as the treatment temperature of molten iron increases, the chilling effect of the mold on the metal melt is strengthened, and the solidification undercooling of the alloy increases. According to the heterogeneous nucleation radius, the critical nucleation radius of graphite decreases, which is conducive to the nucleation of graphite and increases the number of graphite in cast iron.
Figure 2 shows the morphology of primary austenite of cast iron prepared at two liquid iron treatment temperatures.
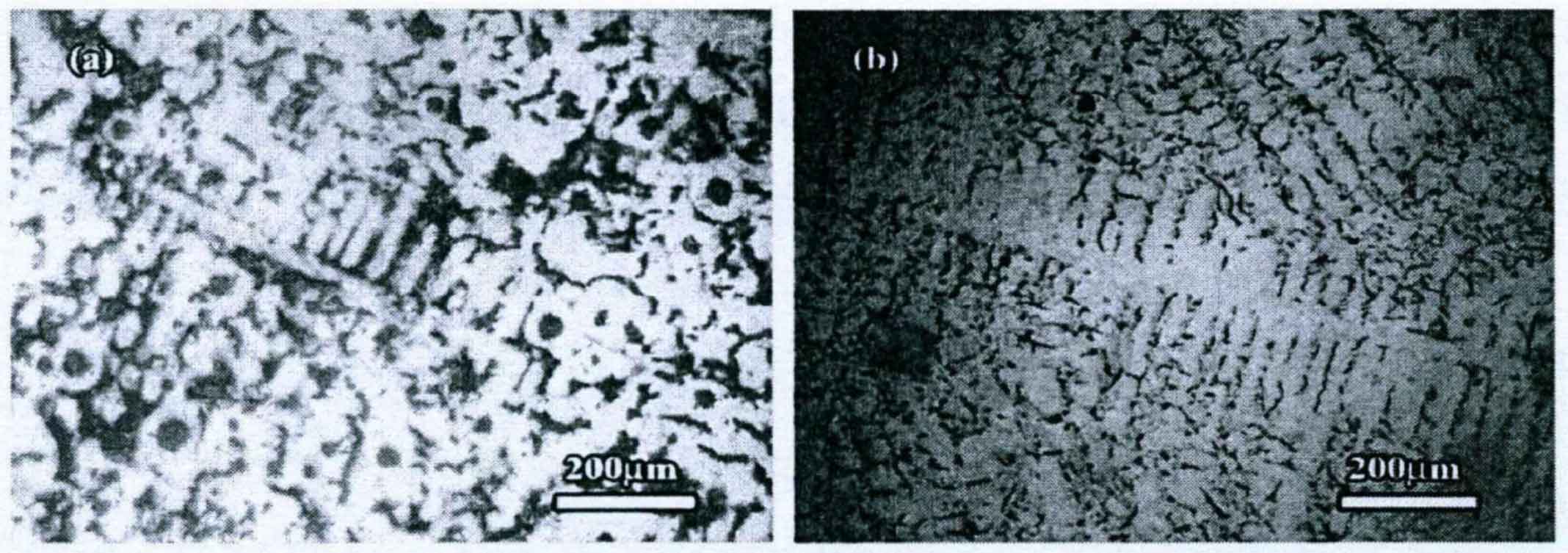
The results of statistical analysis on the arm spacing of austenite secondary dendrite in Figure 2 are shown in the table below.
Treatment temperature / °C | 1510 | 1560 |
μm | 27.88 | 25.22 |
It can be seen from Figure 2 and table that the primary dendrite arm and secondary dendrite arm of austenite are relatively developed in cast iron prepared at two different molten iron treatment temperatures. In cast iron prepared at higher treatment temperature, the length of primary dendrite arm is much larger than that of cast iron prepared after low temperature treatment, The arm spacing of secondary dendrites is smaller than that of cast iron after low temperature treatment.
The size of the secondary arm spacing mainly depends on the cooling rate and local solidification time of the alloy. The slower the cooling rate and the longer the local solidification time, the larger the arm spacing of the secondary dendrites.
When the treatment temperature of molten iron increases, the chilling effect of the mold on molten iron will be increased, the undercooling degree of metal solidification will be increased, the critical radius of metal nucleation will be reduced, the number of nuclei in the metal melt and the driving force in the process of metal solidification will be increased, and the number of nuclei in the metal melt will be increased. The increase of the number of nuclei in the molten metal significantly reduces the secondary dendrite arm spacing. Therefore, the higher the treatment temperature of molten iron, the smaller the secondary dendrite arm spacing of austenite.