Most of all kinds of porosity casting defects are located in the key parts of the cylinder block, and the size is generally large. Once they occur, the cylinder block blank will be directly scrapped. Therefore, such defects directly affect the scrap rate of the casting cylinder block. The reason for the large size of these pore casting defects is that their formation mode is not single, but the comprehensive effect of various forms of gas. In the floating process after the formation of pore casting defects, they often gather with various slag inclusions to form large gas slag holes. Therefore, the size of this defect is larger than that of a single pore, The impact is more serious. The figure below shows the scanning diagram of comprehensive gas slag hole defects inside the cylinder barrel and its energy spectrum component analysis. As shown in figure (a), the shape of the defect is an inverted cone with a diameter of about 600 μ m. The inner surface is black and smooth, and there are some small pits nearby. EDS analysis shows that the 1 and 2 positions in the pores are oxide scales, and the white and bright parts are various inclusions or fallen sand particles. At the same time, the graphite around the defect has obvious coarsening phenomenon.
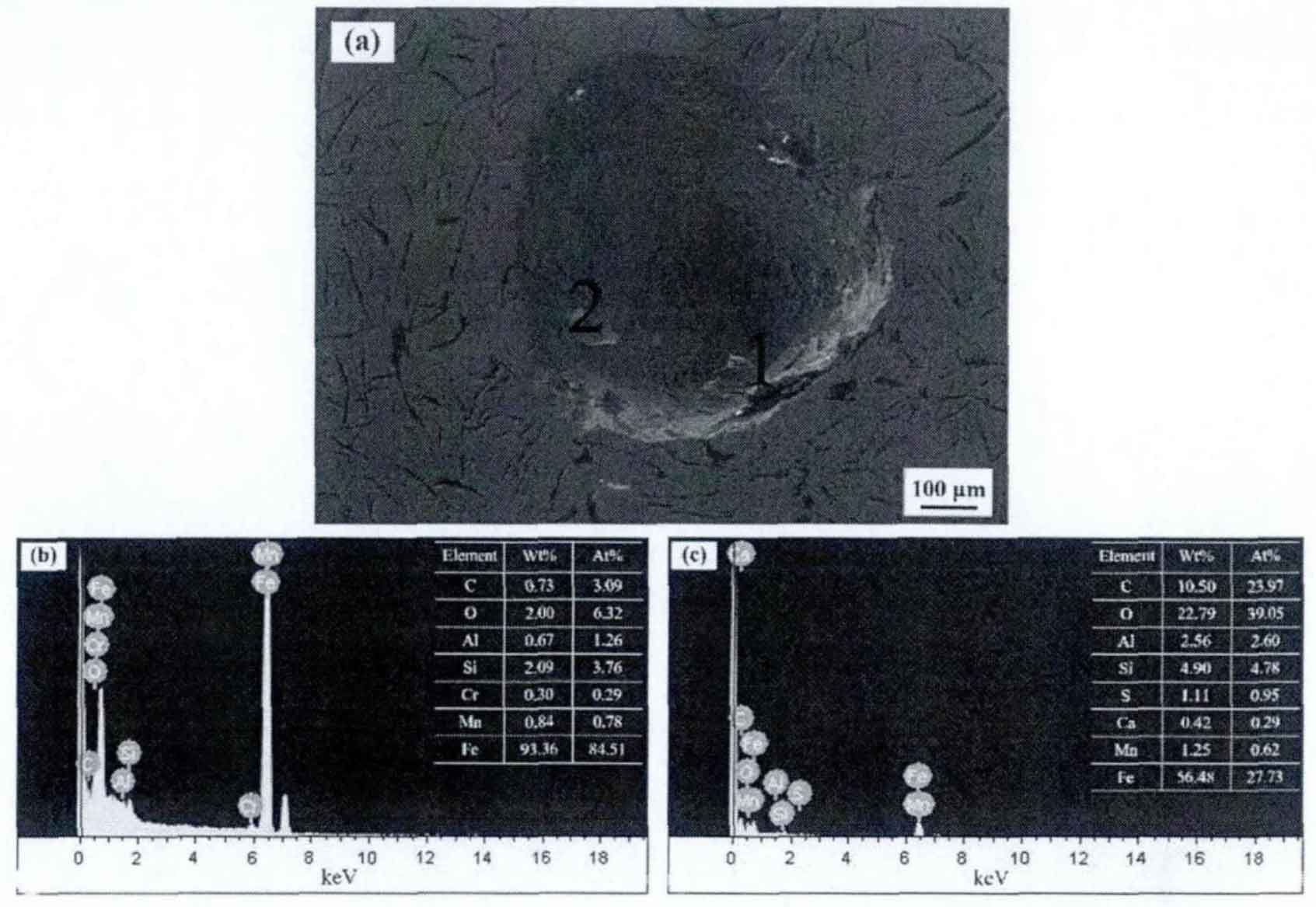
Air hole defect is an urgent problem to be solved in the production of gray cast iron by sand mold casting at present. There are many factors causing such defects, so countermeasures must be put forward:
- The air outlet needle or exhaust plate shall be reasonably designed above the sand mold, so that the total exhaust section shall be 1.5-1.8 times of the total section of the ingate.
- The gating system should be designed as a semi open and semi closed system, which not only has a certain slag retaining capacity, but also the molten iron filling pouring is relatively stable, reducing the involvement of gas casting defects.
- The melting and box pouring temperature of molten iron shall be strictly in accordance with the process. It is better to adopt automatic pouring to ensure the continuous and stable pouring process.
- Sand mold parameters are an important factor affecting porosity casting defects, which should be strictly controlled: moisture 2.8-3.2%, compactness 36-42%, warm compaction strength 180-220kpa.
By adopting the above improvement measures, ZHY casting has greatly reduced the porosity casting defects of gray cast iron cylinder block produced by sand casting and reduced the scrap rate.