In the filling process of liquid metal in gray iron lost foam casting, there is an air gap between the front of liquid metal and the pattern, and there is a dynamic balance between gas generation, gas escape, liquid metal filling speed and air gap size. The filling speed of liquid metal is affected by many factors, such as the type of alloy, pouring temperature, model material, coating layer permeability, negative pressure Model geometry, etc. The effects of negative pressure, model density, pouring temperature, static head of liquid metal, permeability of coating layer, pouring scheme and model geometry on mold filling speed were mainly studied.
In dry sand lost foam casting, vacuum negative pressure has the following functions:
- Generate pressure gradient in the mold, compact the molding sand, and prevent sand flow and mold collapse;
- Absorb the gas produced by the thermal decomposition of EPS model, reduce the pressure in the mold, and promote the flow of liquid between EPS model and mold interface;
- Prevent pores, bright carbon and other defects caused by EPS gas decomposition products.
The test results are shown in Table 1.
Negative pressure (mmHg) | Total mold filling time (s) | Average filling speed (cm/s) |
No vacuum pumping | 1.18 | 17.00 |
-200 | 1.05 | 19.05 |
-300 | 0.94 | 21.35 |
-400 | 0.87 | 22.99 |
-500 | 0.74 | 27.02 |
Fig. 1 is the curve of the relationship between the average mold filling speed and negative pressure of molten metal in lost foam casting of gray cast iron under the same other test conditions.
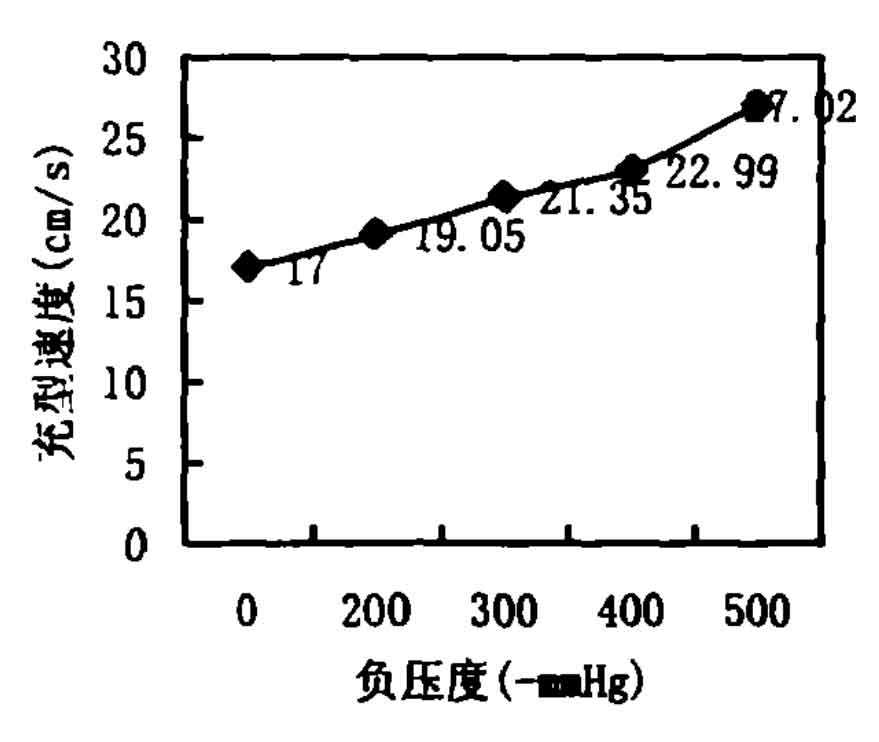
The time difference between two adjacent points along the length of the model is the time when the liquid metal flows through the two points. According to the distance between the two points, the average speed of the liquid metal flowing through the two points can be calculated, and the speed value is regarded as the instantaneous speed at the midpoint of the line between the two points.
Figure 2 shows the velocity distribution between the filling velocity and flow distance of liquid metal under different negative pressure degrees. Below the negative pressure of – 400mmhg, the filling speed of molten metal is relatively slow at the beginning of filling, and then gradually accelerates until it reaches a maximum value. After this point, the filling speed gradually slows down, and then reaches a relatively stable filling speed. At the initial stage of pouring, because the liquid metal has a certain degree of superheat and low viscosity, the mold filling acceleration of the liquid metal is very large under the action of vacuum and negative pressure. As the filling process proceeds, the EPS model vaporizes and decomposes, the air pressure in the air gap between the EPS model and the liquid metal increases, and the driving force of liquid metal filling will decrease. In addition, the decomposition of EPS model of liquid metal front has a great chilling effect on the liquid metal, which makes the front temperature of liquid metal drop and the fluidity become worse. Therefore, after a period of time, the liquid metal filling gradually enters the dynamic equilibrium state, and the liquid metal filling speed tends to be stable. When the negative pressure reaches – 500mmhg, the decomposition products of EPS model can quickly escape from the mold, and the filling speed is very fast at the beginning of liquid metal filling. After a period of time, the negative pressure in the vacuum box decreases, and the fluidity of the liquid metal becomes poor. The liquid metal is filled at a relatively stable filling speed.
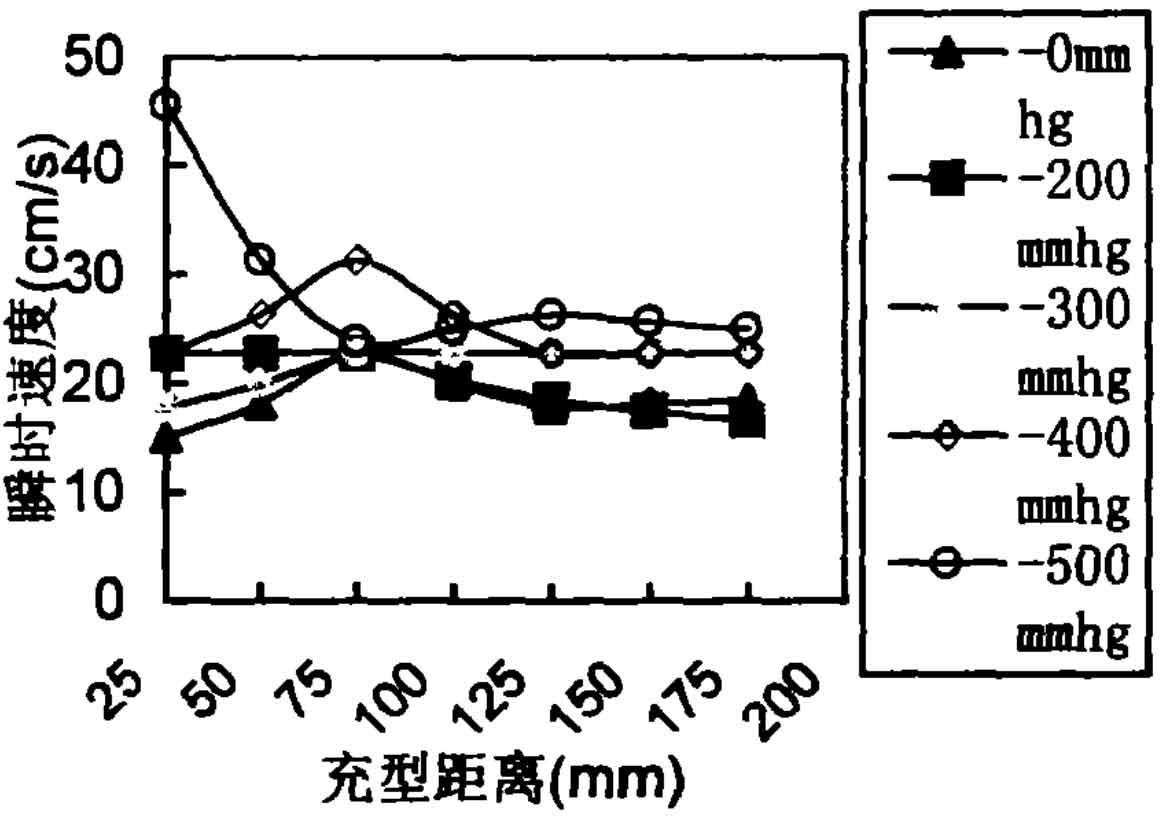