The samples as cast and normalized were observed by Kearns vh-5000 ultra depth of field optical metallographic microscope. The metallographic microstructure of the samples as cast and at different normalizing temperatures is shown in the figure. Figure a shows as cast nodular cast iron, which is composed of pearlite, ferrite, graphite and a small amount of cementite, and a large amount of graphite is surrounded by ferrite in the as cast state, showing an ox eye shape. Fig. B shows the microstructure of the metallographic phase at the normalizing temperature of 870 ℃. Compared with as cast nodular cast iron, there are a lot of fine pearlite around the graphite ball, and the ferrite becomes less. In addition, massive cementite is mixed in the middle of pearlite structure. Fig. C shows the metallographic microstructure with normalizing temperature of 900 ℃. Compared with 870 ℃, there are more fine-grained pearlite, but there is no obvious change in cementite content. It can be seen from figure d that when the normalizing temperature increases to 930 ℃, there is almost no massive cementite structure, and the granular pearlite structure continues to increase and the ferrite structure continues to decrease.
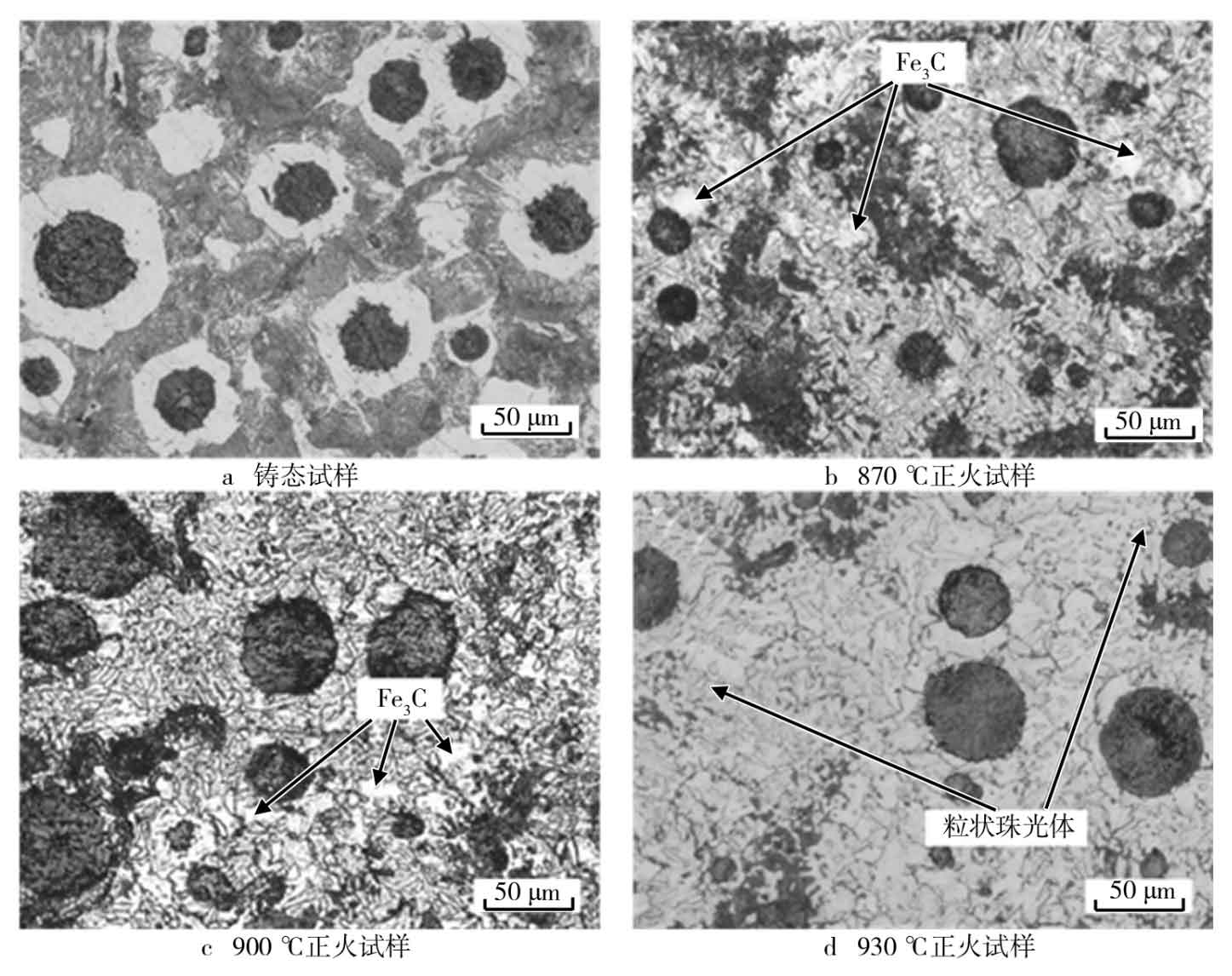
When the temperature rises, the hot pressing stress occurs in the material. When the hot pressing stress reaches a certain value, it will deform the austenite and plug the dislocations in the austenite around the cementite. These dislocations produce local stress around the cementite, making the cementite unstable and easy to decompose. In addition, under thermodynamic conditions, cementite is a metastable phase, which will change from high temperature to low temperature (Fe3C → 3Fe + C). However, the diffusion of carbon atoms will increase with the increase of temperature, so as to promote the decomposition of cementite. Theoretically, the nucleation and growth temperature of graphite in austenite is 900 ~ 950 ℃, which is consistent with the reduction of cementite seen in the experiment when the normalizing temperature is 930 ℃.
Most of the carbon in nodular cast iron exists in the form of graphite balls, which can absorb or release carbon atoms, and the decomposition of cementite will inevitably produce carbon atoms, which will form graphite core at the austenite grain boundary. According to the colloidal equilibrium theory, the solid solubility of graphite core is large. There is a high to low solute concentration gradient between graphite core and graphite ball, which makes the carbon in graphite core diffuse around graphite ball. Therefore, under the normalizing condition of 930 ℃, cementite decomposes and granular pearlite becomes more in the microstructure of nodular cast iron.
Normalizing is a heat treatment process applied to nodular cast iron (also known as ductile iron) to refine its microstructure and improve its mechanical properties. This process involves heating the iron to a temperature above its austenitizing temperature, followed by air cooling. The effects of the normalizing temperature on the properties and microstructure of nodular cast iron are significant and can be summarized as follows:
Microstructural Changes
- Refinement of Grain Structure: Normalizing at higher temperatures leads to the formation of a more uniform and refined grain structure. This refinement occurs because the high temperature dissolves the carbides in the matrix, and the subsequent air cooling promotes a uniform distribution of graphite nodules in a ferritic or pearlitic matrix.
- Graphite Nodule Effects: The normalizing process can impact the size and distribution of graphite nodules. Proper control of the normalizing temperature is crucial to maintaining the nodular shape of the graphite, which is essential for the ductility and toughness of the material. Too high a temperature can lead to nodule growth and potential coalescence, which may adversely affect mechanical properties.
- Matrix Changes: The matrix of nodular cast iron can shift from pearlitic to ferritic or vice versa, depending on the normalizing temperature. Lower normalizing temperatures favor the formation of a ferritic matrix, which is softer and more ductile. Higher temperatures promote a pearlitic matrix, enhancing strength and hardness.
Effects on Mechanical Properties
- Tensile Strength and Yield Strength: Normalizing can increase the tensile and yield strength of nodular cast iron, especially when a pearlitic matrix is formed. The refinement of the grain structure and the uniform distribution of graphite nodules contribute to this improvement.
- Ductility: The impact of normalizing on ductility depends on the resulting matrix structure. A ferritic matrix, resulting from lower normalizing temperatures, will typically have higher ductility. In contrast, higher normalizing temperatures that promote a pearlitic matrix can reduce ductility due to the inherent brittleness of pearlite.
- Hardness: The hardness of nodular cast iron increases with normalizing temperature, particularly as the matrix shifts towards pearlite. This is because pearlite is harder than ferrite, offering improved wear resistance but at the cost of reduced machinability.
- Impact Toughness: The uniform distribution of refined graphite nodules and a more homogeneous matrix contribute to improved impact toughness. The effect of normalizing on impact toughness will also depend on the matrix composition, with a ferritic matrix generally providing better toughness.
Optimal Normalizing Temperature
The optimal normalizing temperature for nodular cast iron depends on the desired combination of mechanical properties. Typically, the normalizing temperature range is between 900°C and 950°C (1652°F and 1742°F). Adjustments within this range can fine-tune the balance between strength, ductility, and toughness by altering the microstructure of the material.
In conclusion, the normalizing temperature plays a critical role in determining the microstructure and mechanical properties of nodular cast iron. By carefully selecting the normalizing temperature, manufacturers can tailor the material’s properties to meet specific application requirements, balancing strength, ductility, and toughness.