Solid liquid segregation is one of the main defects in thick wall products. Under the condition of good feeding condition and complete disappearance of shrinkage cavity and porosity, the performance of a single thick wall product at different positions is quite different. The most intuitive performance is that the hardness value of the area close to the outer wall and far away from the outer wall of the thick wall product is quite different. The hardness value near the outer wall is generally greater than that far away from the outer wall. Figure 1 shows the hardness distribution of 319s alloy semi-solid die-casting calipers in T6 state. It can be seen that the hardness of the area near the surface of the sample is higher, while the hardness of the core area is the largest, with a difference of nearly 60HV. By analyzing this phenomenon, it may be caused by the uneven distribution of solute elements in the edge and core caused by solid-liquid segregation.
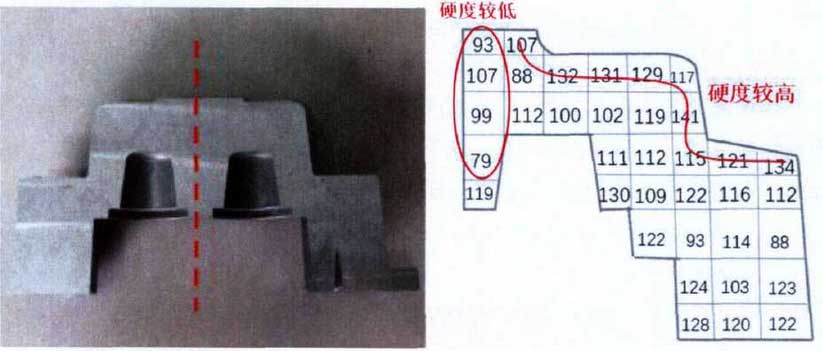
Through a large number of practical production observation, it is found that the solid-liquid segregation in the samples can be divided into two categories: the first is the phenomenon that the liquid phase is significantly higher in the outermost layer of the sample; the second is the uneven distribution of the liquid phase in the whole sample. The solid-liquid segregation in these two aspects is studied. In the experiment, the outermost layer of the sample is defined as the area of 02500 um from the outside of the sample to the inside, that is, the area with about 40 grain sizes. Under the 25X metallographic microscope, it is about half the whole metallographic picture or the width of the whole 50x metallographic picture. The observation and analysis of the overall solid-liquid segregation can be divided into two directions, axial direction and radial direction. The diameter of the upper metallographic sample is 27mm, the middle metallographic sample diameter is 33mm, and the lower metallographic sample diameter is the largest, which is 40mm. The sampling position is marked as shown in Figure 2. The influence of different process parameters on the two kinds of solid-liquid segregation is studied through design and experiment.
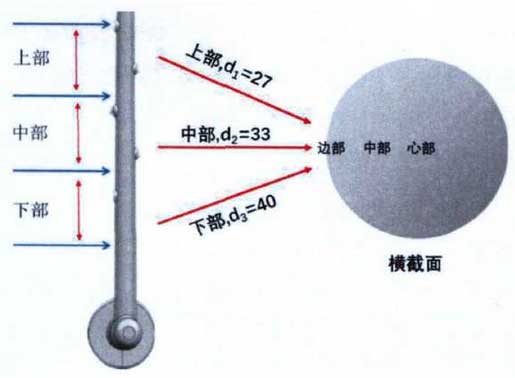
On the basis of studying the effect of process parameters on shrinkage and porosity, the basic experimental parameters for studying solid-liquid segregation were determined. By improving the mold (thickening the cylindrical part and increasing the diameter of the material handle), the feeding channel was widened during the filling process, and the shrinkage and porosity defects of the sample were significantly reduced. The improved die is shown in Fig. 3. Based on this die, the influence of different parameters on solid-liquid segregation of 319s aluminum alloy during semi-solid die casting was studied.
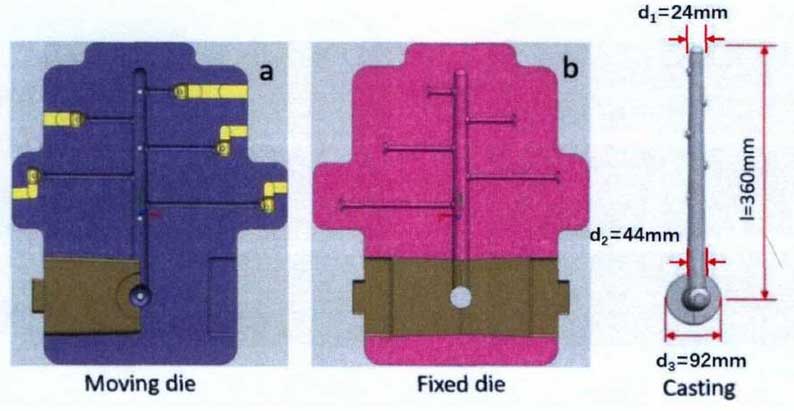