The figure shows the primary austenite structure of nodular cast iron with different wall thickness. Among them, figures (a) – (c) are the primary austenite structure diagrams in samples with thickness of 20, 40 and 60mm respectively.
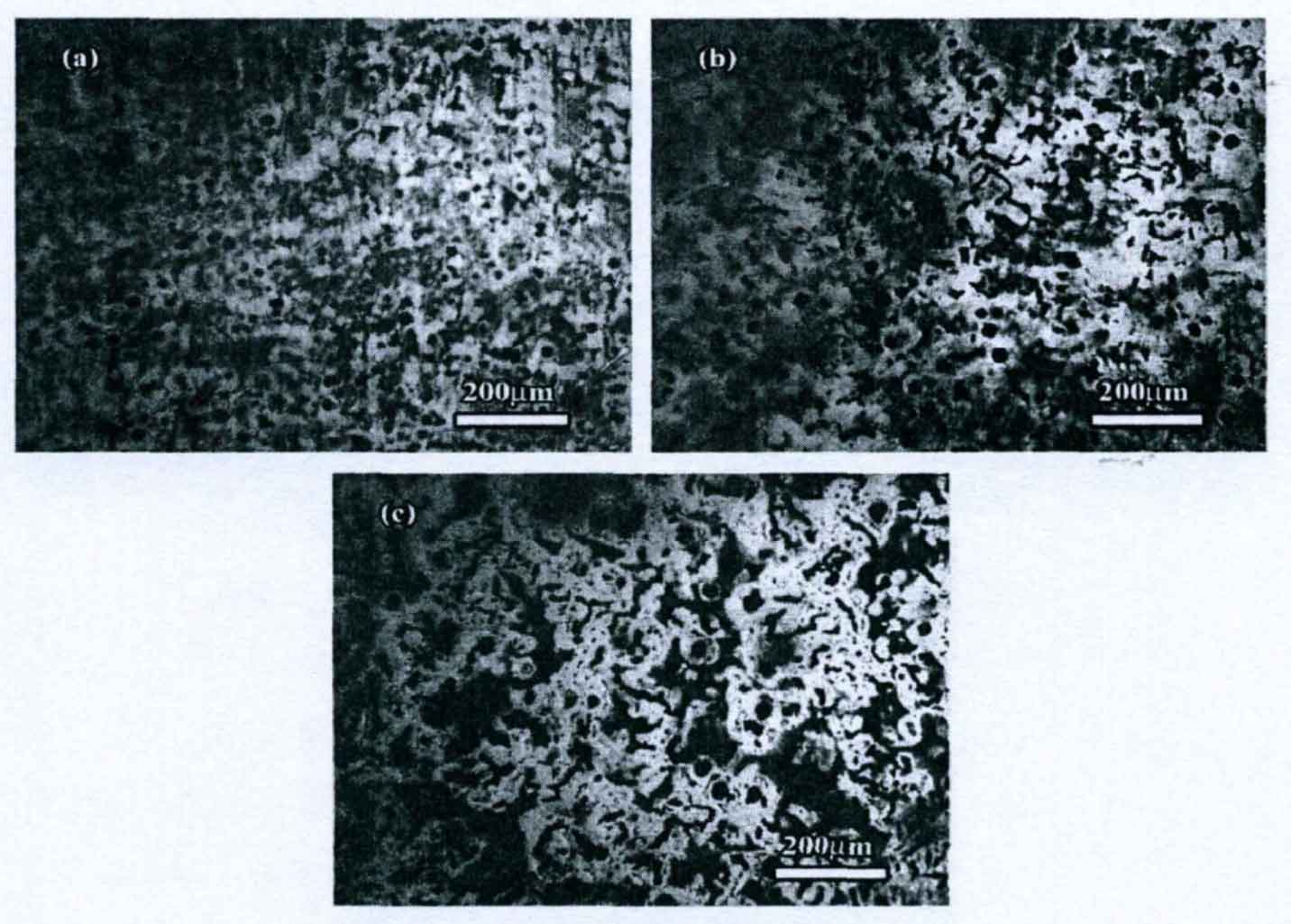
It can be seen from the figure that in the sample with wall thickness of 20mm, the primary austenite presents austenite dendrite morphology, and the primary dendrite arm is long and fine. When the wall thickness increases to 40mm and 60mm, the dendrite morphology of cast iron alloy is not developed, but the primary austenite appears coarsening. With the increase of sample wall thickness, the cooling rate of solidification process decreases, resulting in the decrease of solidification undercooling, the extension of grain growth cycle, and finally the formation of coarse structure.
On the other hand, the rare earth elements in the vermicularizing agent not only have a strong role in degassing (oxygen, hydrogen, nitrogen, etc.) and desulfurization in the metal melt, but also can selectively adsorb on the surface of the grown grains, which will hinder the growth of the grains and refine the grains. At the same time, some of the high melting point desulfurization products left in the metal melt too late to be discharged to the slag surface can serve as the morphological substrate of graphite and play a certain role in inoculation and modification. When the wall thickness of the sample increases, the vermicularizing agent burns seriously during the metal solidification process, and the residual rare earth content in the final cast iron decreases, which reduces the modification and refinement of the vermicularizing agent, so that the final austenite structure becomes coarse.