There are many factors that cause slag hole defects, such as raw material composition of gray cast iron, slag removal during smelting, parameter control during pouring, composition control of sand mold and sand core, etc. The combination of these factors magnifies the possibility of the occurrence of casting defects in the cylinder block slag hole. Therefore, in view of the formation factors of slag hole casting defects, the following elimination measures are proposed accordingly:
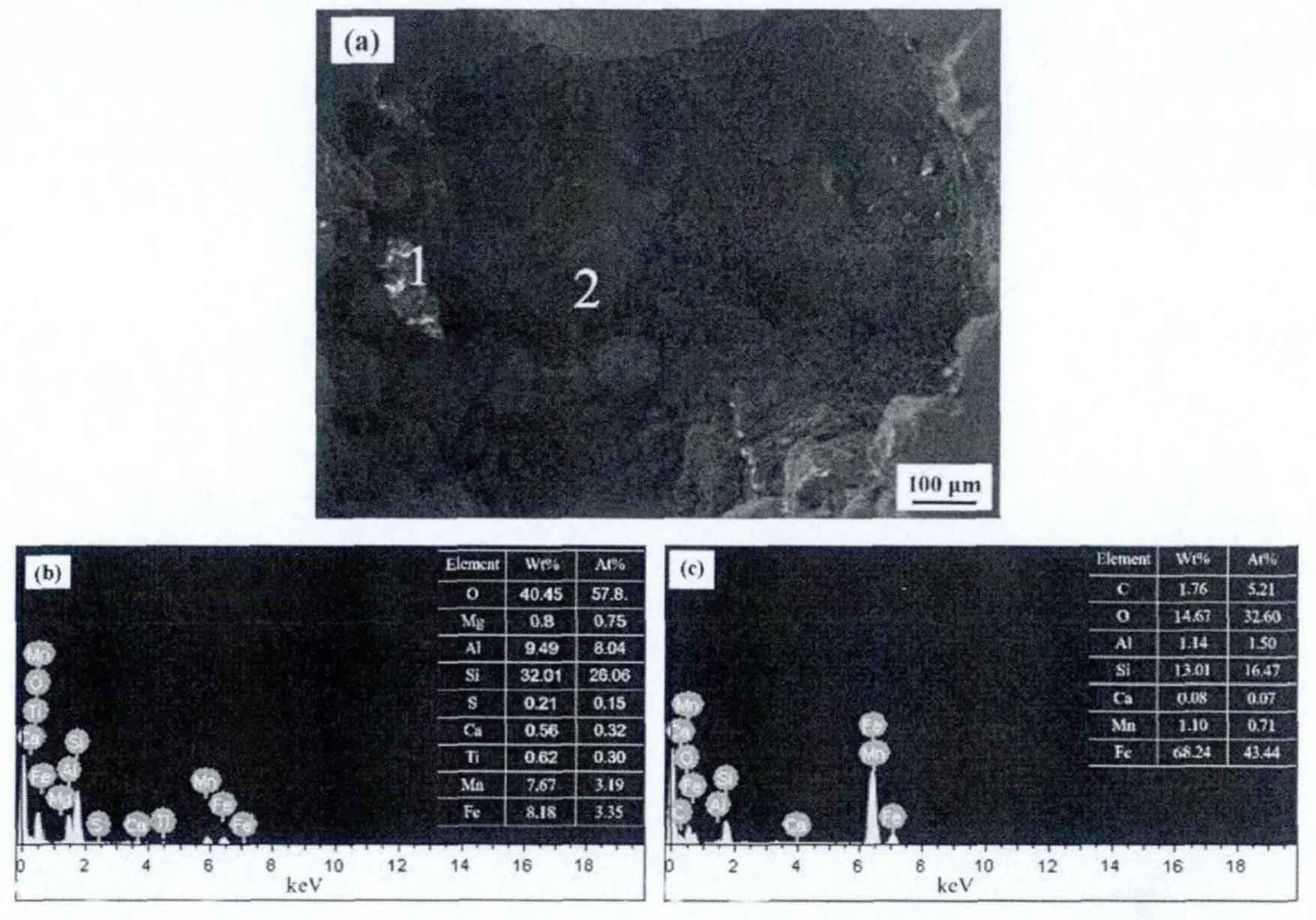
- Strictly control the composition of smelting raw and auxiliary materials, prevent the introduction of various inclusions, and strengthen the cleaning of returned materials.
- The slag removal process during the scorching process shall be complete and clean to prevent more residual scum from flowing into the pouring furnace and into the mold.
- The pouring riser shall be reasonably designed, the pouring speed shall be moderate, and the pouring process shall be stable, so as to prevent excessive impact of molten iron on the sand mold, resulting in slag falling from the sand mold and sand holes.
- The composition and forming process of sand mold and sand core shall also be strictly controlled. The repeated use of sand particles will change the water content, wet compressive strength and compactness of the sand mold, increase the brittleness of the sand mold, easy to fall and form sand holes.
It is worth noting that the defects in castings are not single, and often two or more types of defects exist at the same time and affect each other. Therefore, when analyzing the defect forming factors, we should integrate multiple factors and put forward reasonable defect elimination measures to provide theoretical basis and technical support for casting production.