The graphite morphology in gray cast iron has obvious influence on the fracture process and mechanism of gray cast iron. As shown in Fig. 1 (a), when the graphite sheet in the sample is perpendicular to the direction of external load (stress), the fracture of gray cast iron mostly originates from the tip of the graphite sheet, and its direction is parallel to the graphite sheet, and the sample is normal fracture. The straighter the graphite sheet, the greater the fracture probability of the sample according to the above mechanism. At this time, the stress at the crack tip is the largest and the main crack propagation path is the shortest. On the contrary, as shown in Figure 1 (b), when the orientation of the graphite sheet is at a certain angle with the direction of the applied stress (the state of the bent graphite sheet tip), under the action of the applied stress, the crack propagation direction at the graphite tip is at an included angle with the direction of the main crack θ , At this time, the force on the graphite tip changes.
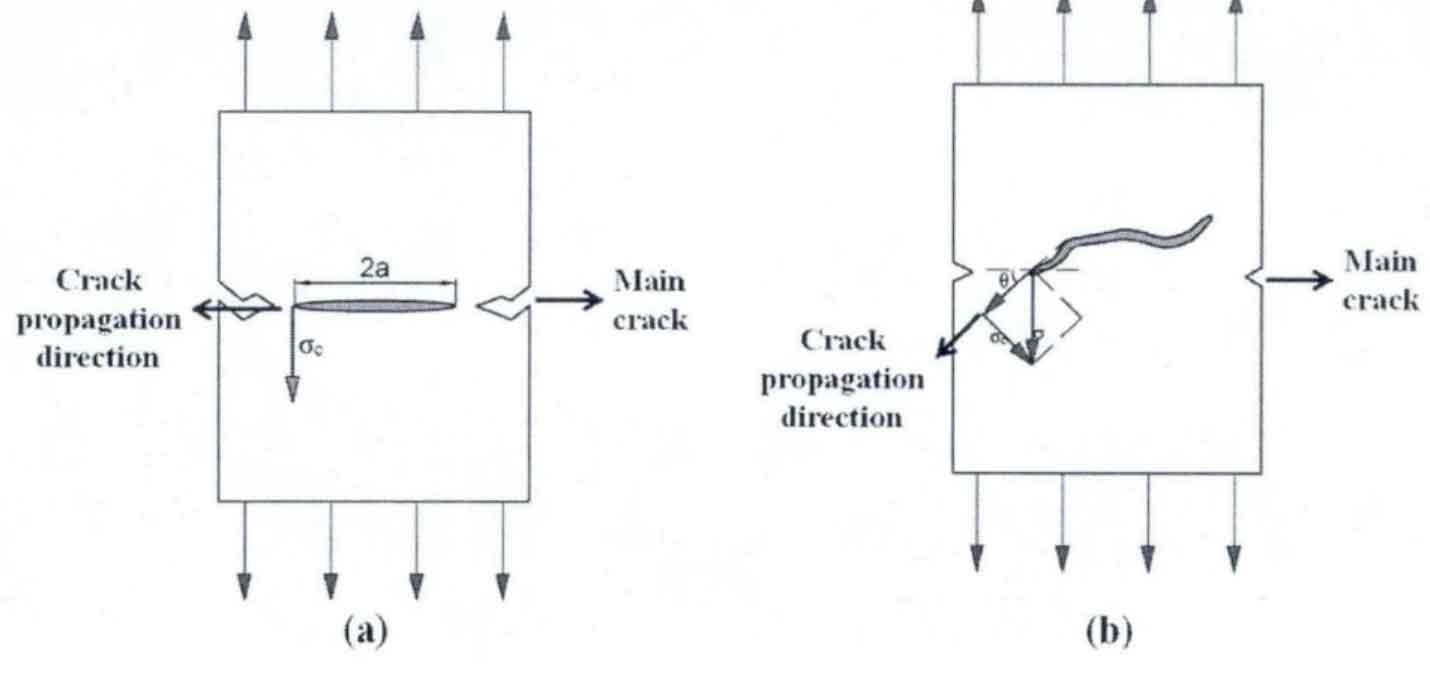
According to Griffith fracture theory, fracture stress of brittle materials:
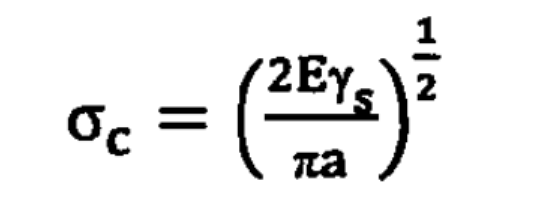
Where: e is young’s modulus, ys is crack surface energy, and a is half of the effective length of fracture crack. That is to say, the fracture stress at the graphite tip increases with the decrease of the graphite sheet size. When the graphite sheet is bent, the fracture stress at the graphite tip:
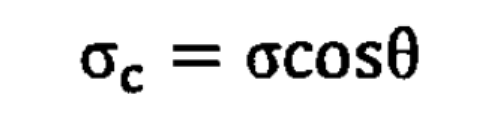
At this point, σ c < σ , That is to say, in order to make the crack at the tip of bent graphite expand, it is necessary to apply greater external stress, that is, the strength of the material increases.
The graphite in Fig. 2 (a) is parallel to the fracture direction of the main Cai grain (as shown in Fig. 1 (a)). The binding force between this kind of graphite and the matrix is relatively poor, which plays a role in promoting the growth of the main crack during fracture. The graphite tip in Fig. 2 (b) is at an included angle with the main crack (as shown in Fig. 1 (b)). This kind of tip crack mainly changes its propagation path during the propagation of the main crack, and the resistance to crack propagation will also change.
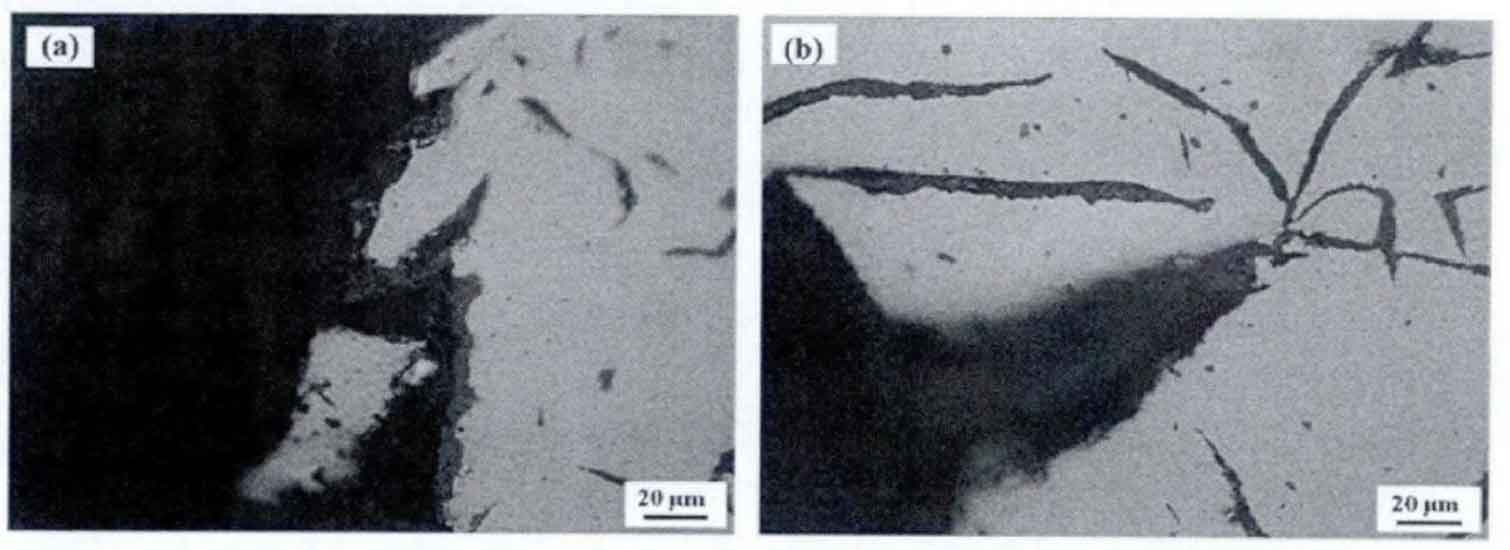
Figure 3 shows three forms of intersection between pearlite and crack; Type a means that the crack intersects with multi-layer pearlite, and these pearlites will be crosscut at the same time when the crack propagates; Type B is that the crack intersects with a layer of pearlite lamella, but when the crack propagates, it will cross cut the subsequent layer of pearlite in turn; The mode C crack only propagates along a layer of ferrite sheet or its interface. As type A and type B cracks will cross cut multiple layers of pearlite, they will suffer a large resistance. According to the structural form, type B resistance should be the largest, and the possibility of fracture is slightly small. However, the C-type crack only propagates along a layer of ferrite sheet or its interface, and the resistance to the crack propagation should be the minimum. However, when the pearlite structure is refined, the lamellar spacing of pearlite will become smaller and the number will increase significantly. The decrease of lamellar spacing will increase the resistance of C-mode crack propagation. The increase of the number will also significantly increase the possibility of the occurrence of mode a and B cracks, and will also increase the resistance to crack propagation.
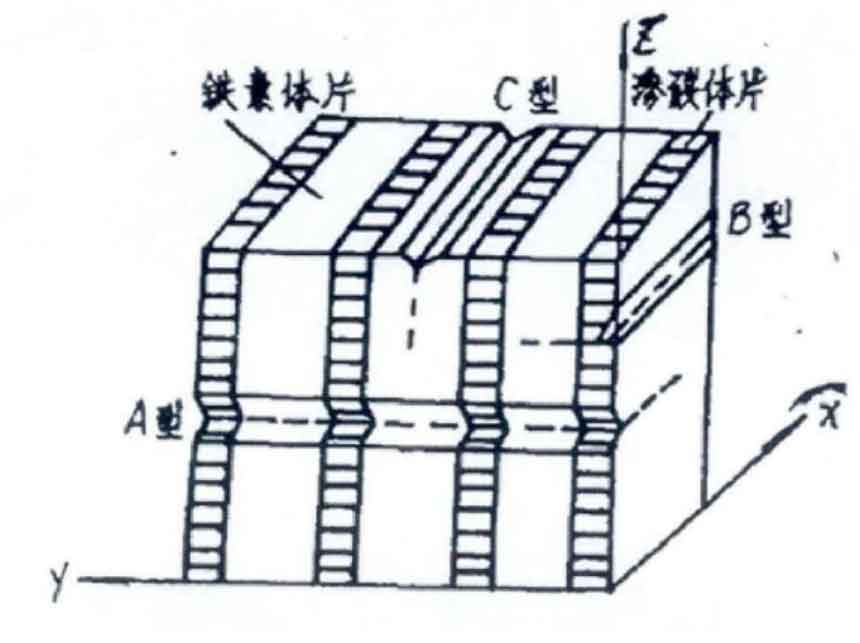
In gray iron castings with 100% scrap added, the improvement of graphite nucleation and growth conditions leads to the refinement of graphite sheet, bending and pearlite. According to the formula, a becomes smaller θ When the value becomes larger, the fracture stress of gray iron castings σ C increase or apply stress σ The tensile strength increases with the increase of. The refinement of pearlite lamellae in gray cast iron matrix leads to the diversification of crack propagation modes, the resistance of crack propagation is increased, and the mechanical properties of castings are improved.