1.Forming process scheme
The filling temperature of the large wheel hub composite squeeze casting method is 720 ℃, the moving speed of the filling head is 25mm/s, the holding time is 30s, and the mold temperature is 250 ℃. The experimental steps are as follows: (1) preheat the mold to 250 ℃, melt the aluminum alloy material and move it into the air pressure holding furnace, keep the temperature at 720 ℃, measure the composition of the alloy melt and make appropriate adjustments; (2) Clean the upper and lower mold surfaces and spray paint; (3) The side hydraulic cylinder drives the moving coil cushion block to reset; (4) The main hydraulic cylinder of the casting machine drives the upper mold downward until the moving ring is close to the moving ring cushion block; (5) Shunt cone downward; (6) The gas transmission system fills the relatively closed filling space with inert gas, and the air pressure in the filling space is in a slightly positive pressure state, i.e. 1010hpa; (7) Set the pressure parameter curve, and the pneumatic conveying system transmits the aluminum melt to the mold filling device; (8) The upward speed of the filling head is set to 25mm/s to push the aluminum alloy melt to fill the mold cavity; (9) Side hydraulic cylinder pressure relief; (10) The main hydraulic cylinder of the casting machine drives the upper mold downward and applies 1600t pressure to the molten metal; (11) The main hydraulic cylinder is depressurized after maintaining the extrusion pressure for 30s, and the casting solidifies for 2 minutes and 30 seconds; (12) The shunt cone goes up to the top; (13) The main hydraulic cylinder of the casting machine drives the upper mold upward to open the mold; (14) Ejector rod ejects the casting.
2.Test results and analysis
The trial produced castings are shown in Figure 1. The products have good forming effect and no defects in appearance. After the castings are cut open, they are basically free of shrinkage and porosity.
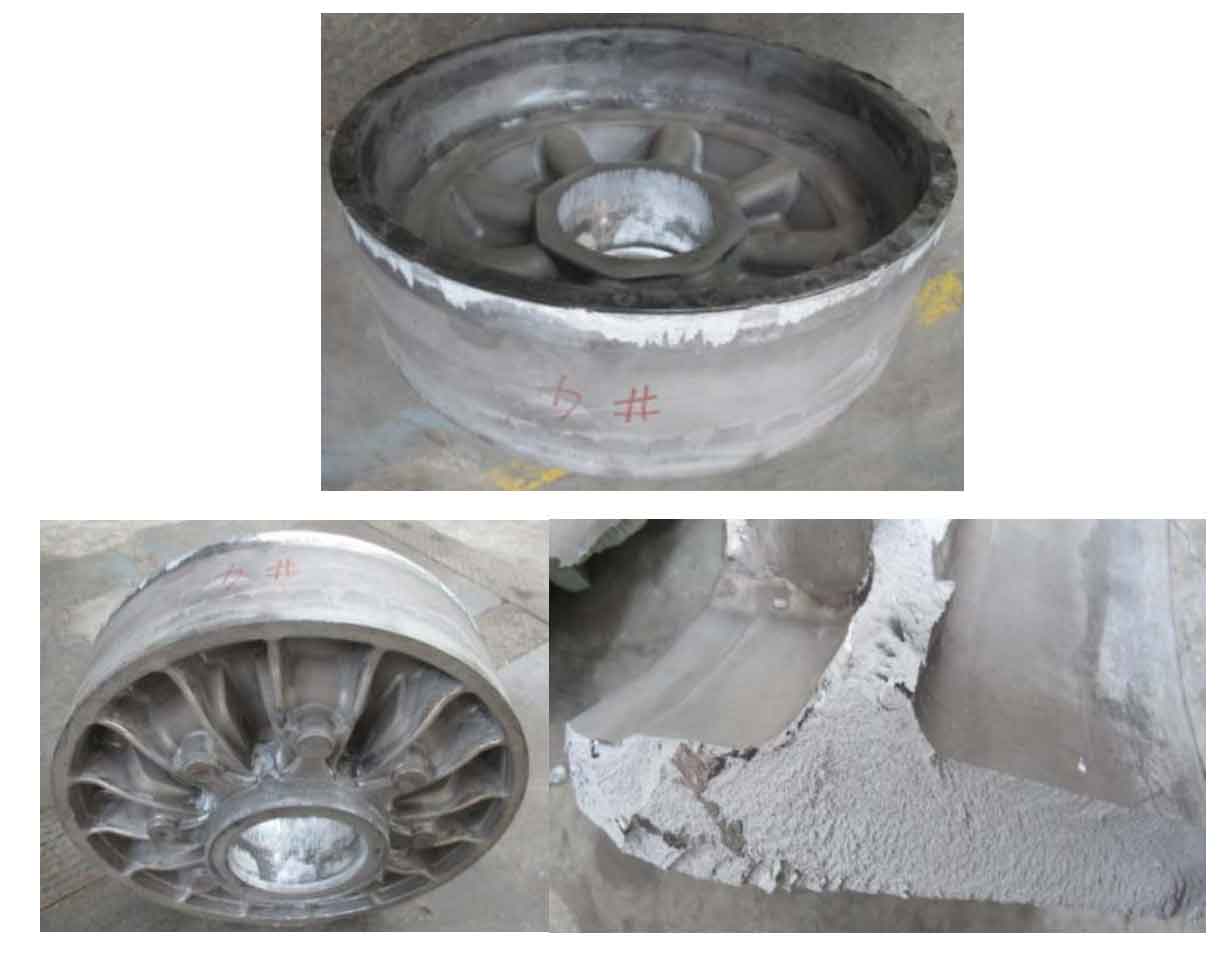
2.1 Hardness and strength analysis
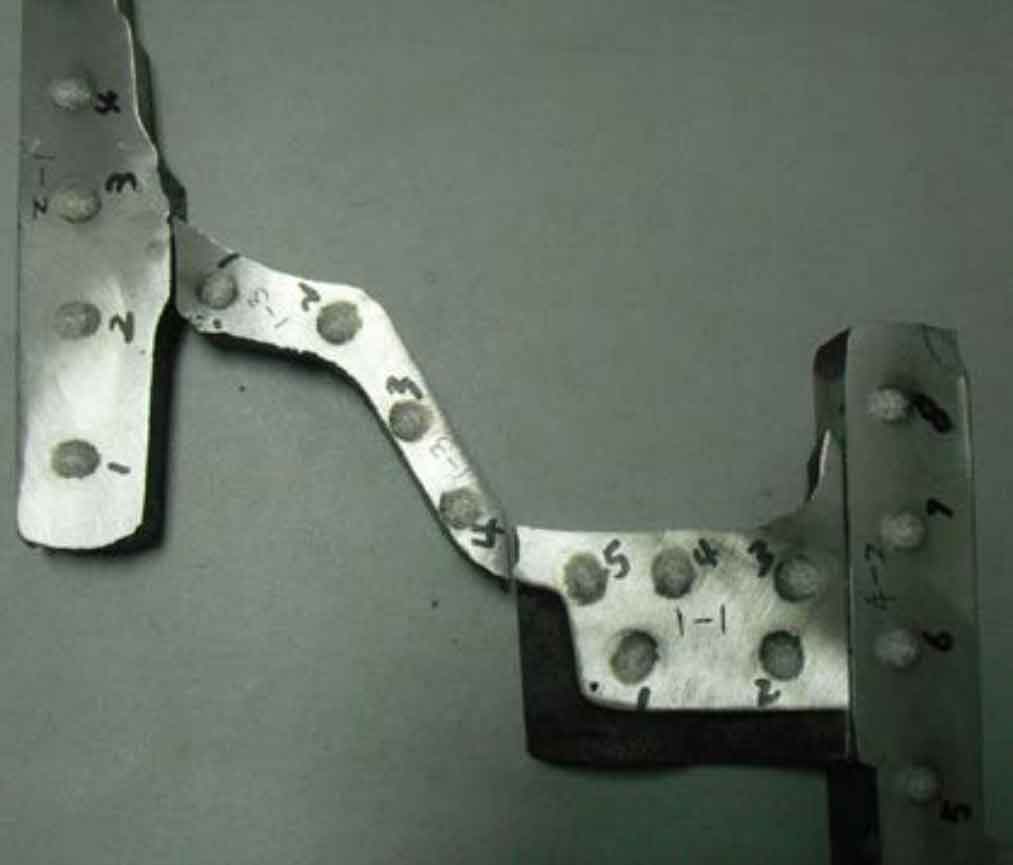
After the formed test piece is cut open, the profile is processed with a milling machine, and the internal hardness of the trial parts is analyzed with a Brinell hardness tester, as shown in Figure 2, and the corresponding test point positions are shown in Figure 3.
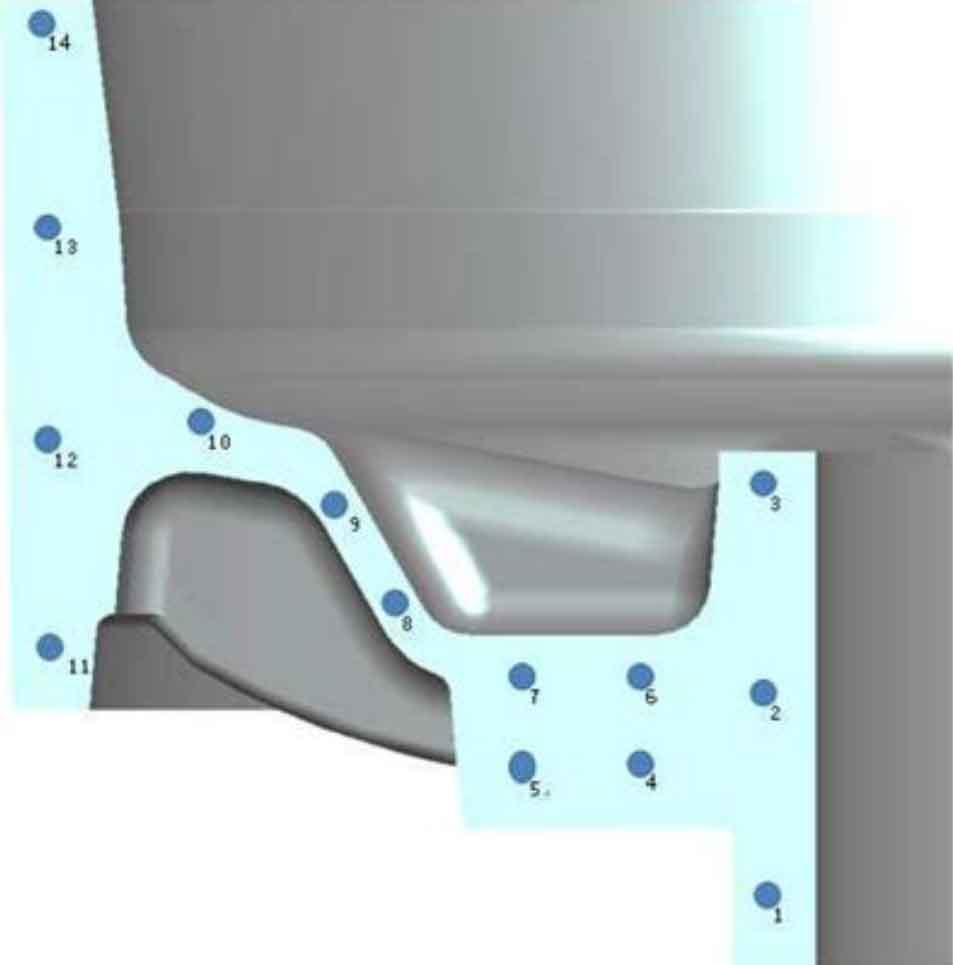
The hardness distribution of the formed test piece is very uneven, as shown in Figure 4. The minimum hardness is 48.6hb and the maximum hardness is 62.4 Hb, with an average value of 56.1hb. There are two points lower than 50hb. The non-uniform distribution of hardness of formed specimens is mainly related to the non-uniform distribution of components caused by segregation during solidification of large parts, especially the distribution of Cu in castings.
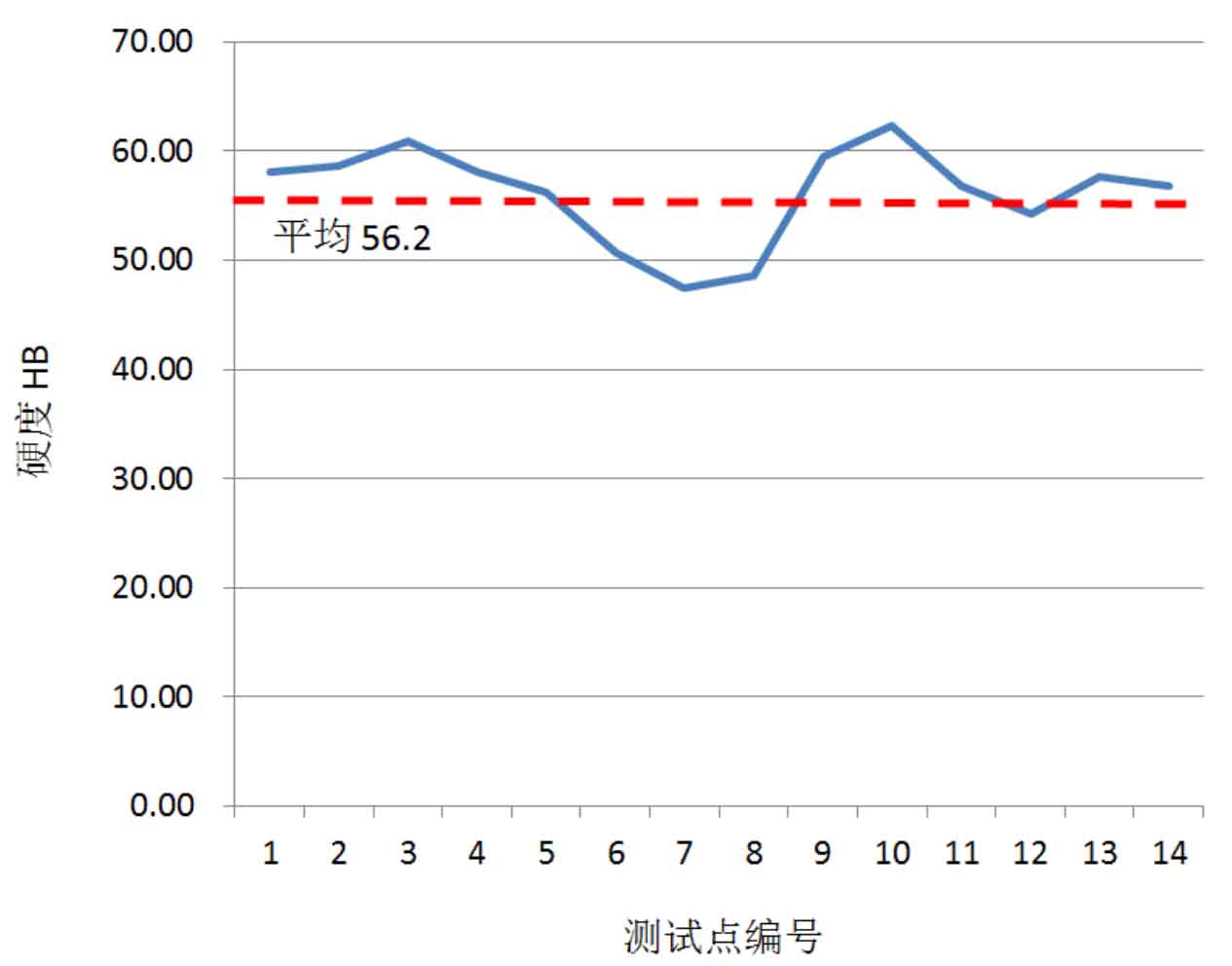
According to the national standard gb/t228.1-2010, the tensile strength of formed castings is tested by using the sanscmt 5105 electronic universal test platform. The tensile speed is 1.5mm/min. The tensile sample is a circular section, and its size is shown in Figure 5. Set a gauge distance of 25mm on the tensile specimen to determine the elongation.
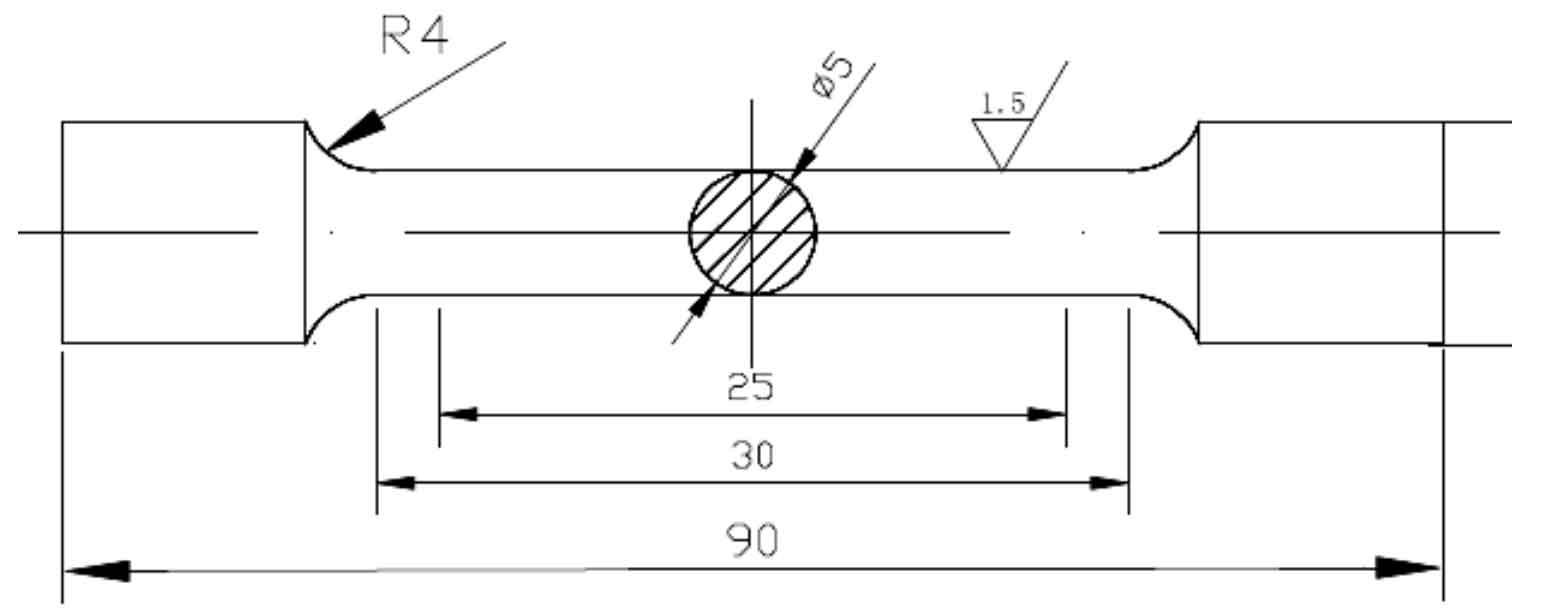
The large wheel hub is divided into three parts: axle, spoke and rim. Five samples are taken from each part for tensile test. The tensile strength test results of each part are shown in Figure 6, the elongation test results are shown in Figure 7, and the average tensile strength of each part is shown in the table.
It can be seen from the data that the mechanical properties of the spoke part are the best. The as cast tensile strength of the casting can reach 230MPa and the maximum elongation reaches 17%. However, due to the complex structure of the spoke part, the measured tensile strength at different parts of the spoke fluctuates greatly. The overall tensile strength of the rim part is relatively low, with an average of 194mpa, but the fluctuation of the data at each part of the rim part is small. This is mainly because the shape of the rim part is regular, and there is a certain gap between the thickness of the rim part and the thickness of the spoke part. Therefore, the extrusion effect of the upper die on this part is different. The tensile strength and elongation force of the axle are between the spokes and rims, and the data of each part are relatively uniform. From the above data, it can be seen that the composite squeeze casting method has a good effect on forming large parts, so the composite squeeze casting system is suitable for forming large parts.
Project | Unit | wheel axle | Spoke | Rim |
Tensile strength | Mpa | 204.92 | 230.42 | 194.02 |
Elongation | % | 7.34 | 13.68 | 5.54 |
2.2 Discussion on motion characteristics of upper die
The external characteristic of the squeeze force exerted by the compound squeeze casting die on the molten metal is the reduction of the axial dimension, that is, the downward displacement of the upper die. During the descending process, the upper die is subjected to the reaction force of the hard shell layer condensed by the molten metal and the isostatic pressure of the molten metal. If the extrusion pressure is insufficient or the direction of the applied force changes, the molten metal will be subject to unstable stress. Therefore, for the composite extrusion forming technology of large parts, due to the large pressurized area, the analysis of the upper die displacement curve is helpful to make an intuitive judgment on the extrusion effect, At the same time, it can also verify whether the floating die works normally and whether the molten metal is extruded smoothly.
During the extrusion of the upper die, the displacement sensor is used to record the displacement of the movable beam during the squeeze casting process, and the real-time display is shown in Figure 8. The accuracy of the sensor is 0.01mm.
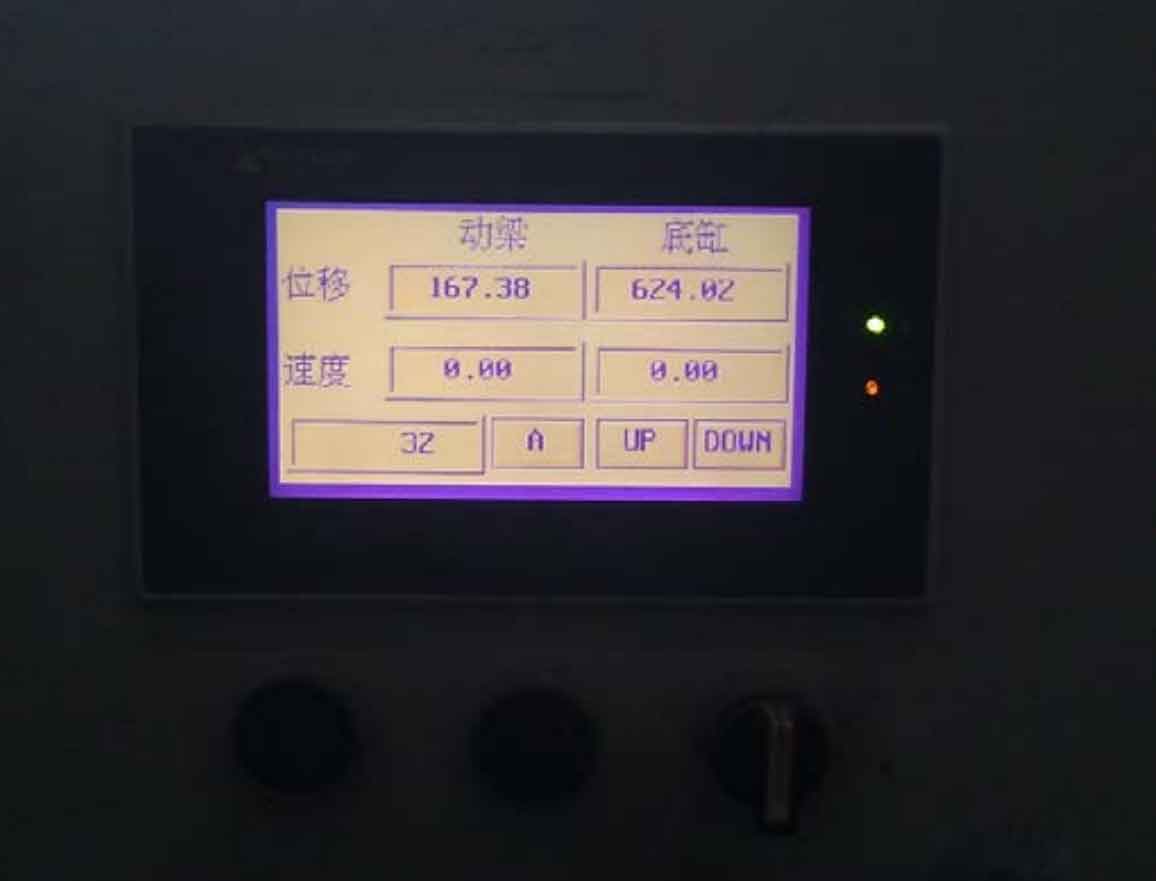
Since the upper mold is fixedly connected with the movable beam through the upper mold base, the displacement of the movable beam is equal to the displacement of the upper mold. The curve of the downward displacement of the upper die versus time from the completion of molten metal filling to the end of extrusion is obtained, as shown in Figure 9.
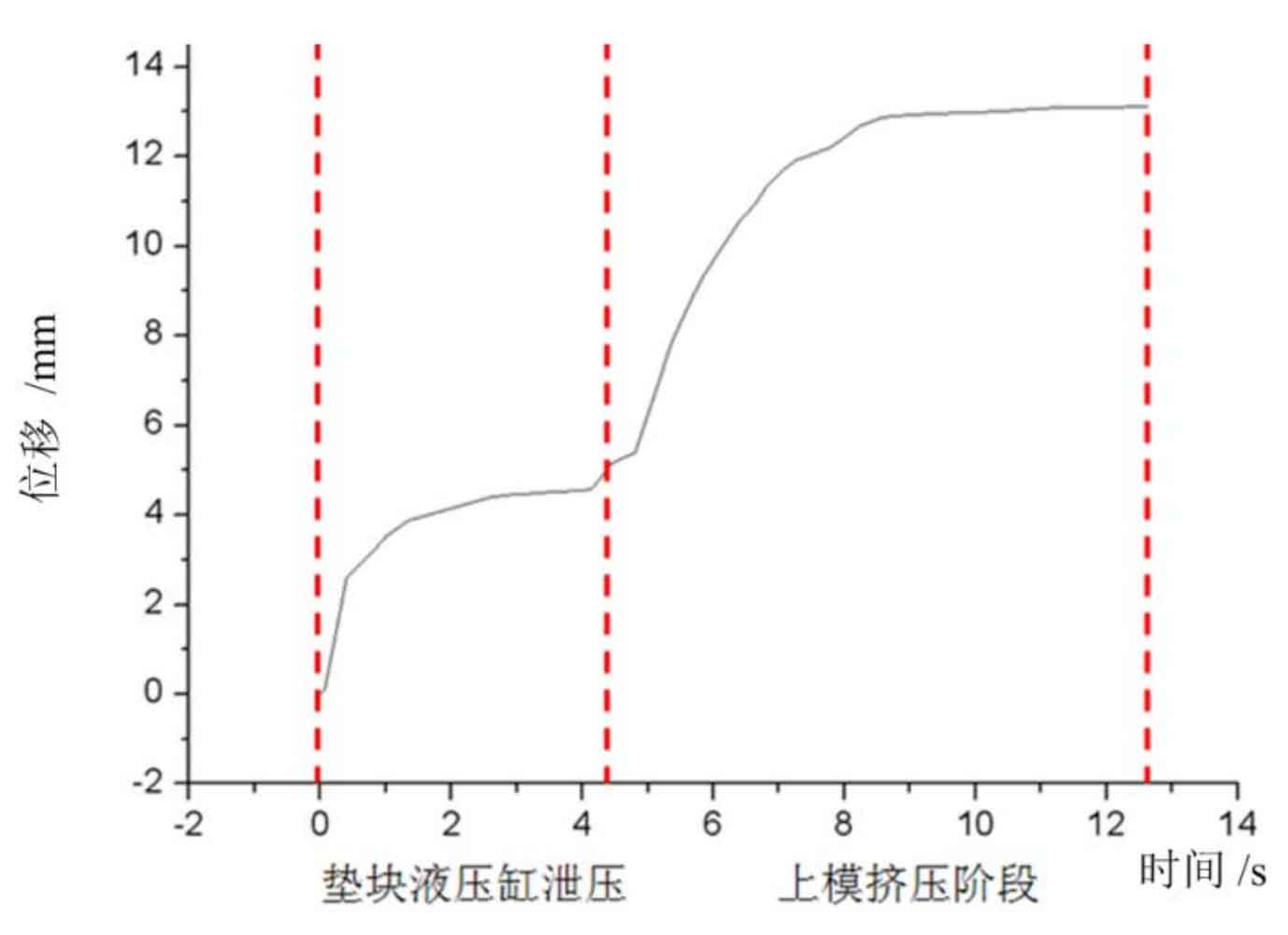
Luoshoujing et al. Analyzed the relationship between upper mold displacement and time for pure copper with a diameter of 70mm and a height of 77mm in squeeze casting. H is the absolute displacement of the punch and H is the height of the metal melt before pressing. The curve between upper mold displacement and time is shown in Figure 10. Curves 1 and 2 are the experimental results of applying 50MPa and 100MPa to the upper mold respectively.
Compared with the displacement curve of ordinary direct squeeze casting, the extrusion process presents the characteristics of composite squeeze casting. When the hydraulic cylinder at the side of the floating rigid support mold releases pressure, the front part of the extrusion curve is formed due to the downward pressure of the movable beam of the casting machine and the weight of the upper mold itself; Then the main hydraulic cylinder drives the upper die to press down to form a partial extrusion curve, but the overall pressurization process is similar to that of direct squeeze casting. Therefore, the forming method of composite squeeze casting basically has the characteristics of direct squeeze casting, such as fast pressure building speed, large area and long time.
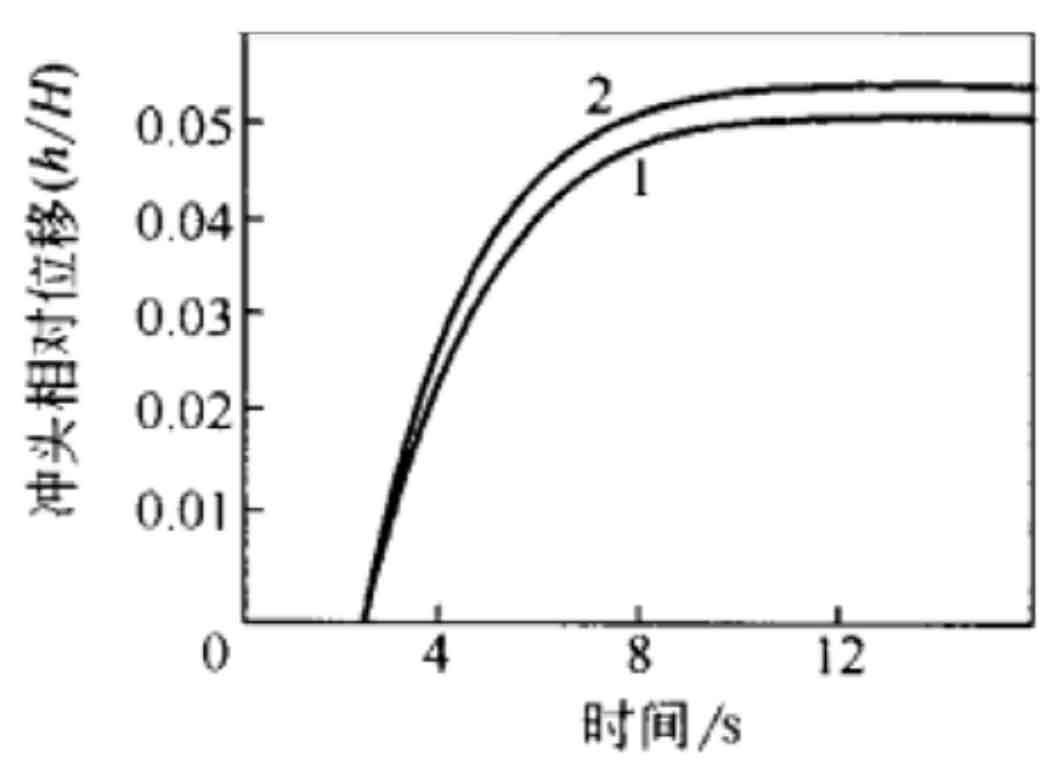
Because the upper die and the moving coil always maintain rigid contact during the extrusion process. Therefore, the curve also reflects the displacement and time curve of the moving coil. From the actual extrusion displacement curve, it can be seen that the floating rigid support mechanism operates smoothly and causes little disturbance to the molten metal.
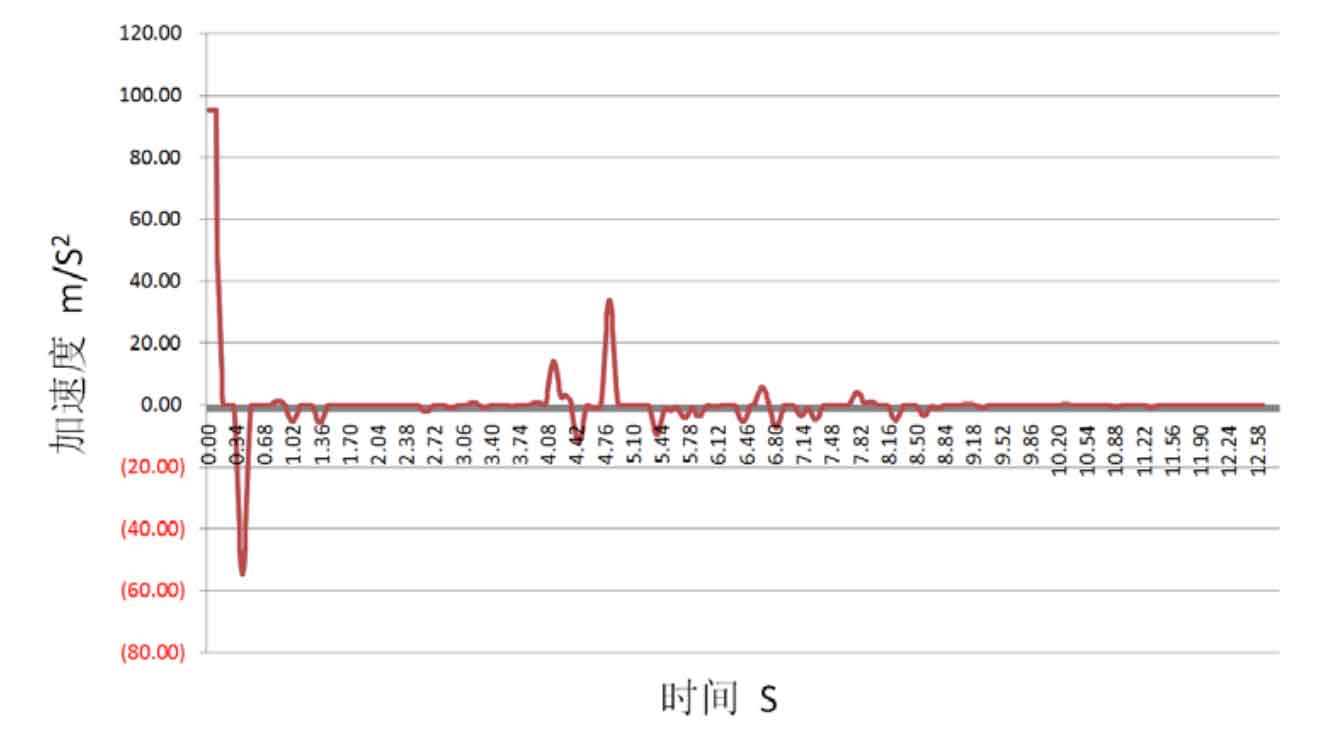
The relationship between time and acceleration can be obtained by quadratic derivation of the obtained displacement and time curve, as shown in Figure 11. It can be seen from the figure that the resultant force on the upper mold is the largest within a short time after the hydraulic cylinder releases pressure, and the acceleration is also the largest at this time, which indicates that the composite squeeze casting method has a faster pressure building speed on the molten metal, while the molten metal only forms a thin shell, and the resistance to the upper mold is relatively small, so the downward speed of the upper mold continues to increase. However, with the passage of time, the acceleration of the upper die decreases continuously. When it decreases to zero, the upper die receives a reverse resultant force, resulting in a negative acceleration, which is mainly due to the increase of the rebound force under the impact of partially solidified metal melt on the upper die. At about the 4th second, the main hydraulic cylinder of the hydraulic press began to pressurize, so the resultant force received by the upper die increased significantly again. Then, as the pressure maintaining stage entered, the resultant force of the upper die kept changing alternately, but the range of change gradually decreased. Finally, the resultant force received was zero, and the upper die also stopped descending. It can be seen from the analysis that the molten metal is always subject to high extrusion force during solidification, which is helpful for the feeding and grain refinement of castings. Therefore, the composite squeeze casting forming system with floating rigid support mold has a good effect on the forming of large parts.