Impact toughness is an important index of large wear-resistant plate. It refers to the ability of material to absorb plastic deformation work and fracture work under a certain impact load. It reflects the micro defects and impact resistance of material. Hardness and toughness have their own effects on the wear resistance. Only when the hardness is improved and enough toughness is provided to support the surface of the workpiece, the wear resistance can be improved.
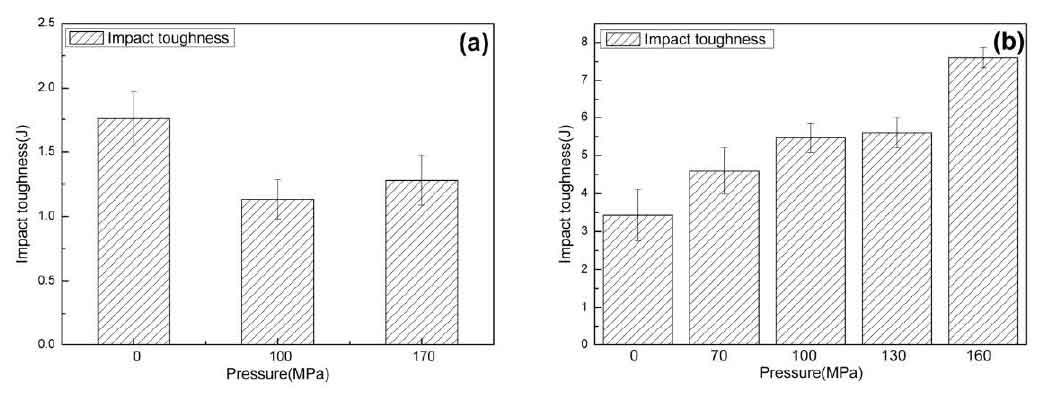
For hypoeutectic alloy 1, as shown in Fig. 1 (a), the increase of solidification pressure does not improve the impact toughness of the alloy, but further reduces it. For alloy 2 with near eutectic composition, as shown in Fig. 1 (b), by comparing the results of impact energy absorption of samples under different pressures, it is found that the sample with the best toughness is the one with pressure of 160MPa, followed by the sample with pressure of 100MPa and 130Mpa, and the toughness improvement of metal mold sample is relatively low. This shows that with the increase of pressure, the toughness of the sample will be improved, but it does not always increase, but reaches the best toughness in a certain state under a certain pressure.
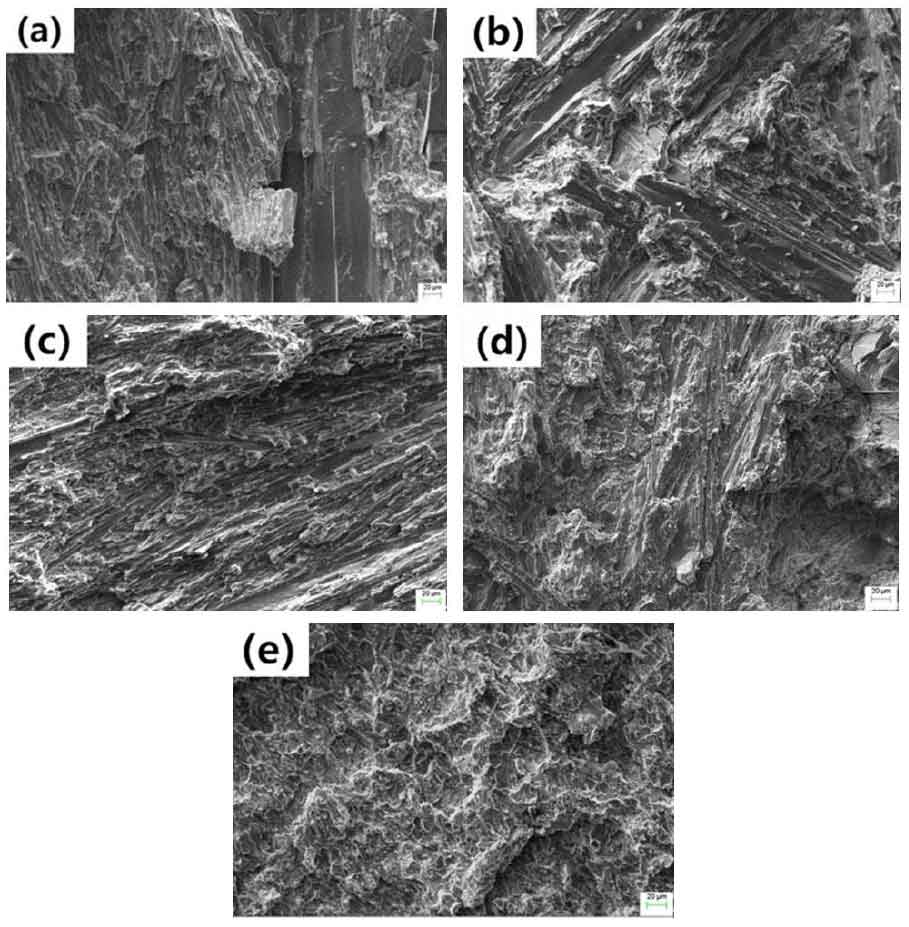
Because chromium white cast iron belongs to brittle material, there is obvious cleavage fracture from the fracture morphology, that is, there is no obvious plastic deformation. It can be observed from Fig. 2 (a) (b) (c) that there is no obvious plastic deformation before carbide fracture, the morphology of the end is bright crystalline, while the austenite part of the matrix has obvious plastic deformation before fracture, and the fracture morphology is dark gray fibrous. Although the carbides are isolated during solidification at atmospheric pressure, their size is large and their combination with the matrix is not very close. During the solidification of pressure casting, the carbide is isolated phase, and its size and shape change greatly. The austenite is continuous phase, so the toughness of the sample is obviously improved compared with that of the sample with large size continuous carbide under normal pressure. In addition, because the metal mold casting is used in the experiment, the heat dissipation is faster, the volume shrinkage rate of the alloy is larger, and the casting can not supplement the holes formed by the shrinkage, which leads to the loose connection between the carbide and the matrix, and a large number of shrinkage porosity and other defects in the matrix structure itself. It can be clearly seen from the SEM picture in Fig. 2 (E) that the carbide is well bonded with the matrix. The carbides in the fracture surface are cleavage fracture morphology, and there are obvious dimples in the matrix. Even at the fracture surface, there is no obvious separation between the matrix and carbides. This is the reason why the strength and toughness of pressure casting samples are higher than that of normal pressure samples.
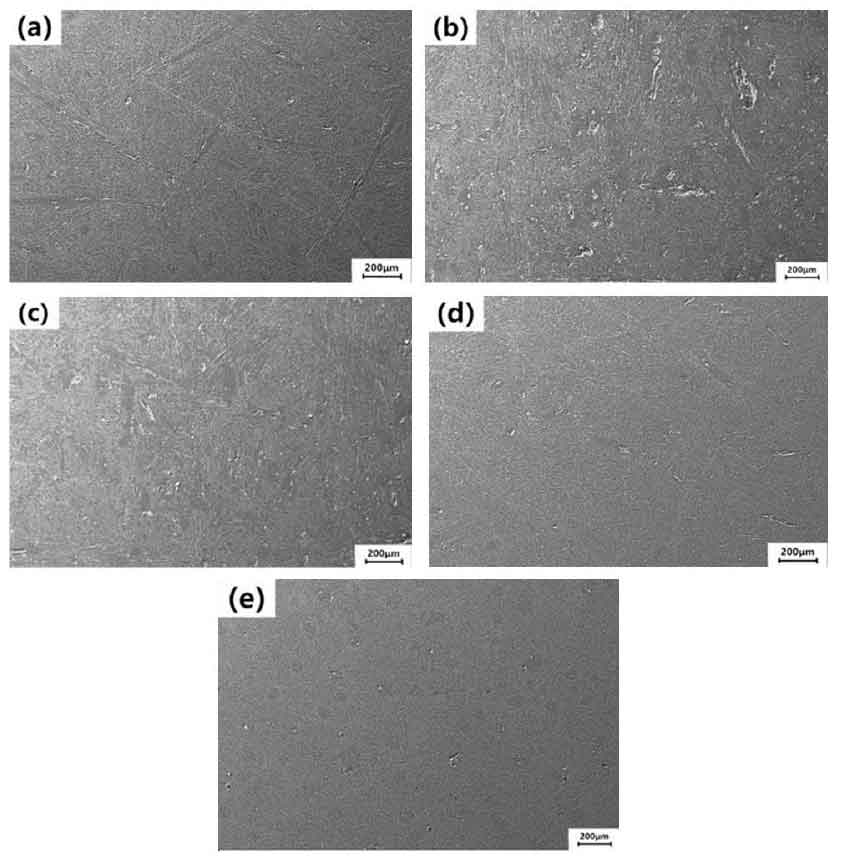
While discussing the reason of impact toughness change, it is necessary to discuss the influence of macrostructure defect of alloy sample, because it directly determines the impact toughness of sample. The casting defects in the solidification structure of brittle chromium white cast iron are the source of cracks in the casting, which greatly reduces its strength and toughness. In the pouring process, the filling speed of the alloy liquid is faster, and the phenomenon of entrapment occurs, so the smaller round pores appear on the surface of all samples. In addition, because the sampling position of the sample is at the top of the sample, the alloy liquid can not complete the feeding in a short time due to the influence of the cooling effect of the upper indenter, so the dispersed shrinkage porosity appears on the surface of the sample. In Fig. 3 (a) (b) (c), that is, under normal pressure and low pressure casting conditions, there are many shrinkage cavities and porosity. These defects lead to the densification of the structure. With the increase of pressure, the number and size of shrinkage cavities and porosity gradually decrease. In Fig. 3 (E), except for the gas pores, other defects basically disappear, and the structure presents a flat and dense state. This phenomenon shows that the pressure can promote the feeding effect on the solidification structure of chromium white cast iron, and the higher the pressure is, the better the feeding effect is, and the denser the structure is.