Because the chromium white cast iron used in the experiment is brittle material and has not been heat treated, the strength is not high, which is easy to cause the material peeling off at the edge of the sample during the impact wear test, which affects the experimental results. Therefore, the selected impact energy is small, which belongs to low energy wear. This kind of wear mainly belongs to cutting wear, but because of the large size and high hardness of quartz sand, it can directly act on carbide, so the carbide spalling will be similar to carbide skeleton disintegration.
According to the wear weight loss curve of alloy 1 under 1J impact energy in Figure 1, the following conclusion can be drawn: under different pressures, the wear rate of as cast sample increases with the increase of wear time, and the wear weight loss of atmospheric pressure sample is the largest, and the wear resistance is the worst. The wear loss of the samples obtained under the other two experimental conditions (100 and 170 MPa) is relatively small, and the wear resistance of the samples is about 1.5 times higher than that of the non pressurized metal. The comparison of the curves at 100 MPa and 170 MPa shows that the wear rate of the sample reaches its peak at 100 MPa, while the further increase of pressure has no effect on the improvement of wear resistance, and may even have a negative effect.
According to the analysis of carbide size, the coarsening of carbide under pressure will lead to more contact with abrasive particles, which will lead to fracture and shedding of carbide, which is different from the wear mechanism under normal pressure. As shown in Figure 2, wear is dominated by cutting due to the low impact work of 1J. Therefore, the wear performance of the impact abrasive is positively correlated with the hardness of the material, and the sliding of the impact abrasive will lead to the grooves and peeling pits of the material. In Figure 2 (a), the ground surface has many cuts and grooves at atmospheric pressure. Due to the concentration of carbide in the matrix, the depth of the cutting groove is very high, and the carbide does not play a good supporting role to protect the matrix, which leads to the direct contact between the abrasive particles and the soft matrix. These factors cause a large number of matrix materials to be torn. Therefore, the continuity of wear will increase with the continuous wear. In Fig. 2 (b), no carbide and matrix spalling pits are found, because the carbide and matrix are refined by pressure, and the hardness is fully matched, so that the sample has good wear resistance. In Fig. 2 (c), there are peeling pits and grooves on the worn surface, but the depth is less than that of the normal pressure sample.
Because chromium white cast iron belongs to brittle material, 1J impact energy is selected to test at first. However, it can be seen from the experimental results in Fig. 3 (a) that under the action of low impact energy, the samples of gravity casting in metal mold and pressurized samples show good wear resistance, and it is impossible to distinguish whether the wear resistance is improved from the weight loss.
It can be seen more intuitively from Fig. 3 (b) that under the premise of increasing the impact energy, no matter what kind of process, with the increase of wear time, the weight loss of wear increases continuously, but the increase degree is different. Firstly, when the pressure is 160 MPa, the wear loss of the sample is obviously less than that of the other three cases. In general, the above results can prove that pressure casting can significantly reduce the weight loss caused by impact wear and improve the wear resistance of high chromium cast iron. Compared with the weight loss of normal pressure metal mold casting samples, the wear properties of samples under 160 MPa pressure are more than doubled.
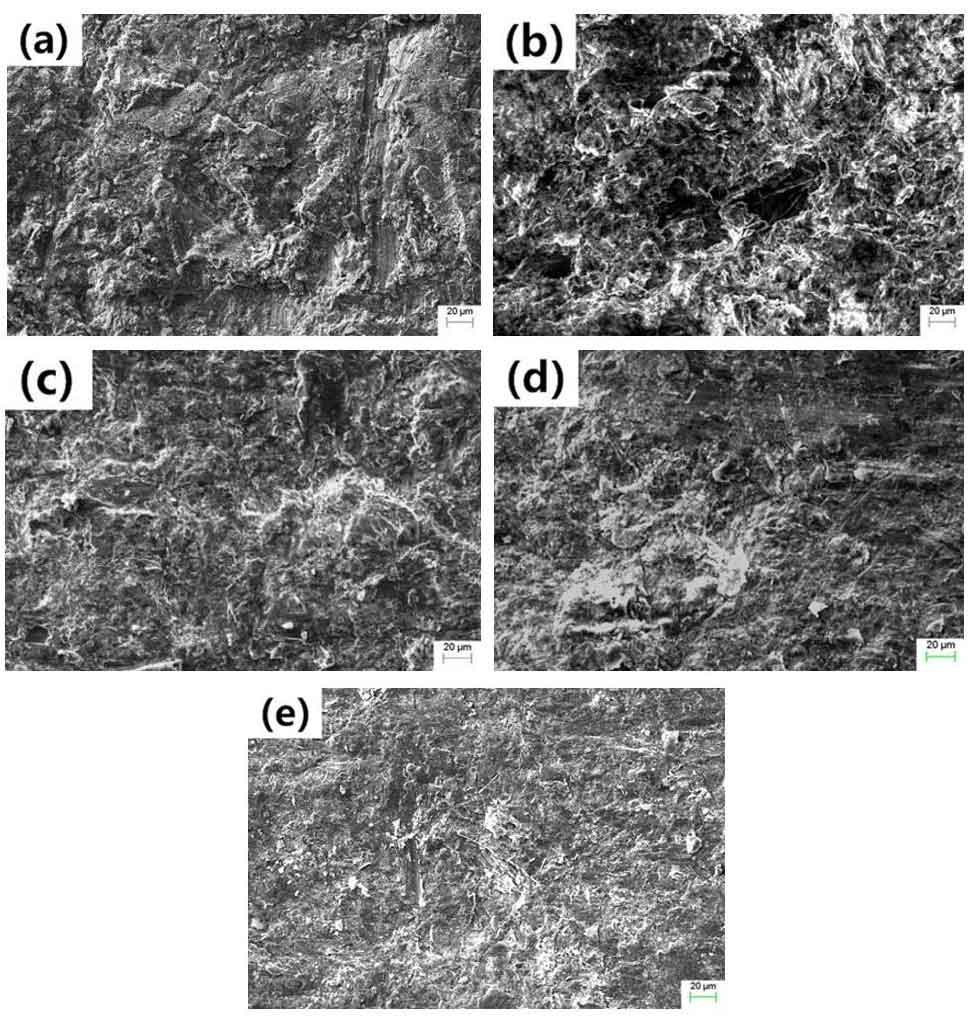
Because the impact energy of 1 / 2J is used in the experiment, cutting is the main wear mode under the condition of low energy impact. The short-range sliding of abrasive particles on the worn surface results in furrow on the worn surface, which leads to wrinkles and spalling of the material and separation of the metal from the substrate. In Fig. 4 (a), there are many cutting and gouging marks on the worn surface of the gravity casting specimen, and the relatively high cutting groove depth indicates that a large amount of matrix material is torn off. There is no obvious plastic deformation on the worn surface, but the furrow is relatively deeper and longer, and some broken or broken hard phase particles fall off the worn surface. The hardness of abrasive quartz sand is high. Under a certain impact condition, these abrasive grains are easy to embed into the matrix structure, and the matrix will form pits under continuous impact; On the other hand, quartz sand can also plough the material on the surface of the sample, leaving scratches on the surface of the sample, and there are furrow marks on the surface of the sample after impact wear. The carbides in Fig. 4 (a) and (b) all show signs of whole block shedding, which is mainly due to the absorption of impact energy in the process of impact wear. The surface of carbide is smooth and the color of carbide edge is bright, but the wear surface in Fig. 4 (b) is obviously plastic deformation. Fig. 4 (c) shows that there are shallow micro cutting gouges on the worn surface, which are slight spalling, and the edge of carbides can be seen vaguely. However, the depth of spalling pits is obviously shallower than that of carbide spalling in low pressure casting. In Fig. 4 (d) (E), when the pressure is above 130 MPa, spalling pits and furrows are also found, but the depth is shallower under the first few pressure conditions, and the carbide and the edge of the matrix can not be distinguished, which proves that the matrix provides good protection for the carbide and reduces the fragmentation and shedding of the carbide.
Combined with the previous analysis of microstructure, hardness and impact toughness, it can be concluded that:
When the sample collides with the abrasive particles, the matrix structure with lower hardness is the first to be exfoliated. With the increasing amount of exfoliation deformation, the carbide will be exposed and directly contact with the abrasive particles. When the size of carbide is large, if the hardness of abrasive grains is greater than or equal to the hardness of carbide, brittle spalling will occur when carbide and abrasive grains collide and collapse directly. In addition, if the distance between carbides is large, the abrasive particles will insert into the carbides and damage the matrix. If the distance between carbides is small, this situation can be avoided, so as to reduce the weight loss of wear.
Under the condition of impact wear, the alloy is mainly subject to the cutting caused by the quartz sand tip penetrating into the matrix structure, which makes the structure separate from the material. Under the action of large impact energy, the impact and extrusion force between the ring and the wear ring further expand the cracks generated in the wear process, deform the impact surface, absorb the impact energy, and soften, fracture and fall off locally at high temperature. Compared with one-time impact, the impact energy of 2J used in this experiment belongs to small energy multiple impact, and the improvement of sample hardness is beneficial to the improvement of impact wear performance.