Gray cast iron is often used to manufacture engine block and other smart car parts because of its unique properties. In the long-term research on gray cast iron, many scholars have taken improvement measures from the aspects of branding process, alloying treatment and inoculation treatment to improve the comprehensive properties of Engine Castings, including casting properties, mechanical properties and processability. In order to better improve the casting structure and stabilize the casting properties, people have paid a lot of attention to the morphology, size and distribution characteristics of inclusions in gray cast iron and the influence of its structure on various properties of castings.
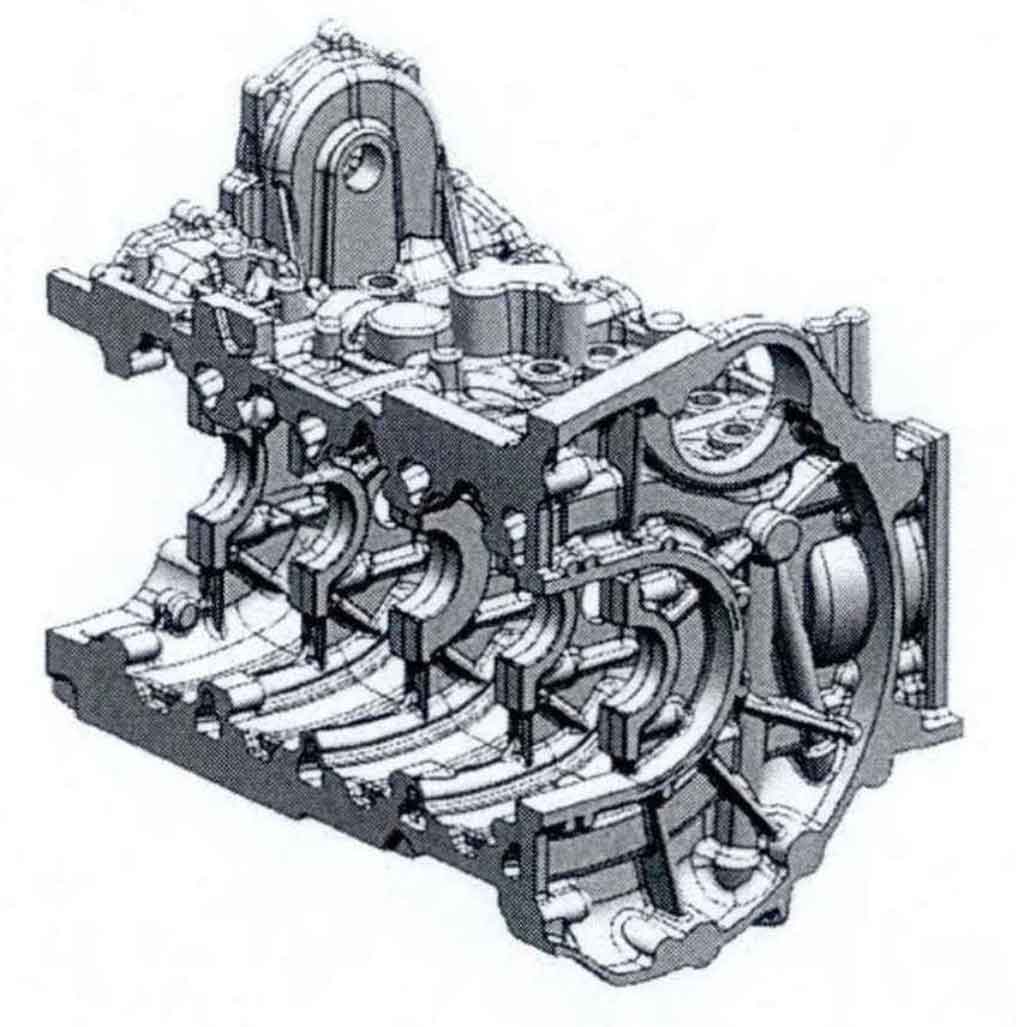
According to the study on the microstructure and composition of gray cast iron, the inclusions in gray cast iron mainly include oxides, carbides, sulfides and nitrides of various alloy elements, such as SiO2, (Cr, Fe3) C, MNS, tin, tie, etc. One part of the whole inclusion phase is infiltrated by the addition of raw and auxiliary materials from the cast iron smelting village, and the other part is formed by the crystallization of various alloys during solidification. The role of Ti in gray cast iron is diverse. When a small amount of Ti is used, it has a certain refining effect on the microstructure of cast iron. However, when the content is too high, except a small amount of Ti will be dissolved in the ferrite in the matrix, others mostly exist in the cast iron matrix in the form of tin or Ti (C, n) (later unified as tin). In such studies, scholars at home and abroad have carried out a very comprehensive study on the morphology of tin inclusions in steel castings and their impact on the microstructure and properties of castings. The amount of Ti in steel castings has a great impact on the size, content and distribution of tin inclusions, which usually changes the as cast microstructure of steel castings, Furthermore, the casting properties, mechanical properties and processability of the composite were affected. However, there are few reports on the nucleation and growth process of tin and its influence on the microstructure and properties of gray iron castings during pouring and solidification.
Taking a certain type of automobile engine block casting (HT250) as the research object, the heredity of tin in the raw and auxiliary materials of gray cast iron melting, the thermodynamics and growth mechanism of tin formation during solidification and crystallization, and the influence of tin structure and distribution on the casting properties were studied. Through these researches, we can have a preliminary understanding of the morphological characteristics and nucleation and growth process of tin inclusion phase in gray cast iron, and analyze and understand its influence mechanism in combination with the influence of tin inclusion phase distribution and size on the mechanical properties and processability of castings, Thus, the production of gray cast iron cylinder block can be further stabilized by improving the composition and microstructure of the castings.
- Tin in gray cast iron mainly comes from tin particles in scrap and reheating materials or tin particles formed by the reaction of Ti in steel matrix and N in cast iron soldering body.
- The heredity of tin in the returned material will lead to the existence of large tin particles with the size of thousands of microns in the gray cast iron, but the number is very small, and the tin particles with this size have a very adverse impact on the mechanical properties and processability of the gray cast iron.
- There are two forms of tin particles crystallized from gray cast iron melt: Tin crystallized from the melt is usually distributed at the austenite grain boundary, and the size is about 4-8 μ m. The tin precipitated from the undercooled austenite is distributed in the austenite, and the size is only 1-2 μ m。
- In gray cast iron, with the increase of Ti content, the content of tin particles also increases, and the size will become larger, which has relatively little impact on the hardness of gray cast iron, but will reduce the tensile strength and cutting performance of gray cast iron.
- Tin in gray cast iron is mainly crystallized during solidification of undercooled melt of molten iron, and this crystallization process mainly depends on [%ti]. [% Solubility product of n 〕. Thermodynamic calculation shows that when the liquid iron is undercooled to 1368 ° C, [%ti] When [%n]=0.000247, tin starts to crystallize.
- A considerable number of tin particles in cast iron also crystallize with MNS as the core. The reason is that both MNS and tin belong to face cubic structure, the mismatch degree of lattice constants between them is low (only 0.05), and the surface of tin and MNS forms a semi coherent interface, which is conducive to the heterogeneous nucleation process.