The influence of alloying elements on the microstructure of cast iron mainly occurs in two stages:
- solidification stage, in which alloying elements mainly affect the formation of austenite, Eutectic Transformation Mode and eutectic structure;
- solid phase transformation stage, in which alloy elements will affect the rate, mode and morphology of austenite transformation. The influence of various elements on cast iron matrix is shown in the table.
There are many kinds of alloying elements in cast iron, and their action mechanisms are also different. According to the demand, some elements can be added separately, but most of them need to add a variety of elements to improve the properties of cast iron. Each alloy element exists in different ways in liquid phase and solid phase cast iron alloys, so the action mechanism and synergistic effect of alloy elements are very complex. The commonly used alloy elements in grey cast iron include Cr, Ni, Cu, Sn, Sb, V, Mo, etc. their functions in grey cast iron are as follows:
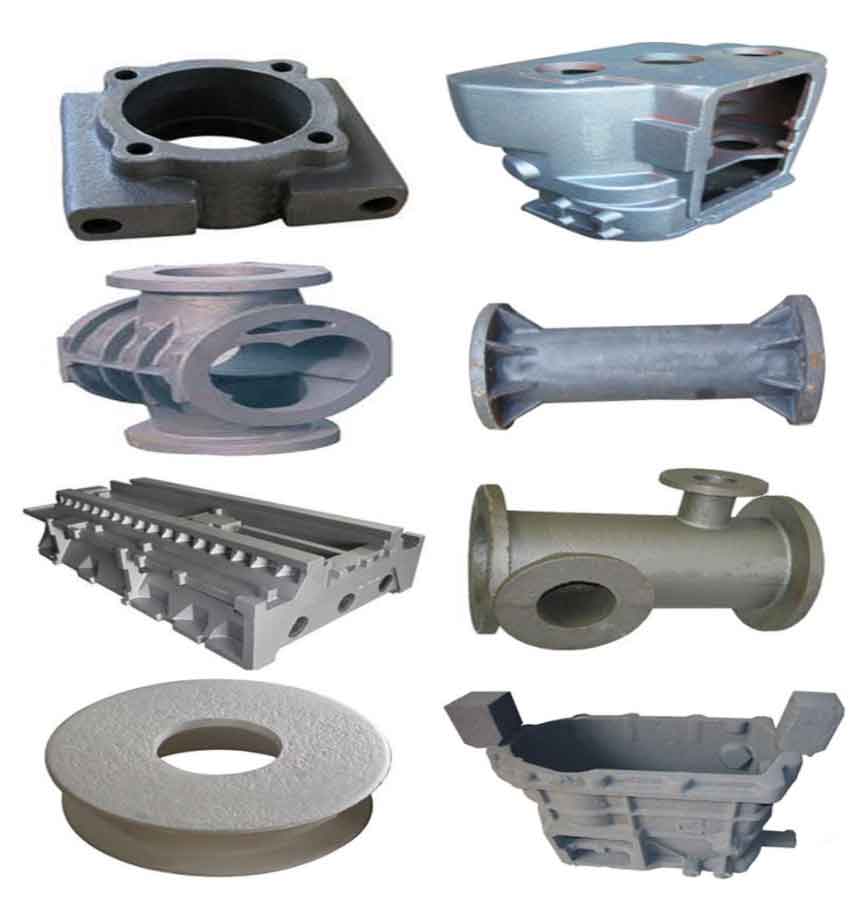
CR mostly exists in the form of solid solution in the solidification process of grey cast iron. The addition of CR will increase the solubility of carbon in austenite. At this time, the carbon content and activity in molten iron will decrease. With the increase of Cr content, the tendency of carbide formation in molten iron increases. However, Cr dissolved in austenite can stabilize austenite, which is mainly reflected in the decrease of free ferrite content and the increase of pearlite content; The eutectoid transformation of austenite is delayed, the inoculation process of pearlite is prolonged, and the hardening property of the body is improved. Adding CR in an appropriate range can effectively improve the tensile strength and hardness of grey cast iron. Generally, when Cr is lower than 1.0% and is still grey cast iron, a small amount of free Fe3C may appear, but the mechanical properties and heat resistance are improved. When the Cr content is 2.0% – 3.0%, white mouth structure will appear.
Ni can form infinite solid solution between W and Fe, but it does not combine with carbon, but is dissolved in ferrite. Ni will increase the eutectic temperature of Fe-G and promote the graphitization of C in molten iron. At the same time, the austenite transformation temperature is reduced and the austenite zone is expanded, which makes the pearlite fine and the content increase, but has little effect on the graphite. The addition of Ni and Cr elements in grey cast iron can effectively prevent the precipitation of ferrite and counteract the tendency of white cast iron caused by CR.
The solubility limit of Cu in eutectic grey cast iron is about 3%. The addition of Cu can increase the eutectic transformation temperature of Fe-G, and it is a weak graphitization element. The solid solution Cu atoms accumulate near the interface between austenite and graphite, hindering the diffusion of carbon in austenite, making the incubation period of precipitation transformation longer, the eutectoid transformation temperature lower, and refining pearlite. The range of adding ferrite in grey cast iron is generally 5-1.5%, which mainly promotes the formation of pearlite, reduces the content of ferrite in the thick wall, and reduces the section sensitivity of castings.
Similar to Cu, Sn can also hinder the diffusion of carbon in austenite, reduce the ferrite content and increase the pearlite content. Figure 1.4 shows the eutectoid decomposition time of austenite in cast iron with SN of 0.02% and 0.14%. When the Sn content is high, the decomposition rate decreases and the eutectoid decomposition time increases. The eutectoid transformation temperature of fine grey cast iron is lower than that of grey cast iron with the same composition but without Sn, so it has the effect of refining pearlite, but the effect is weak. In addition, Sn can also reduce the section sensitivity of cast iron, promote the formation of pearlite without increasing the tendency of white cast iron. These effects are similar to the effect of Cu on the texture of grey cast iron. Therefore, in actual production, fine copper is often used to replace the addition of Cu, which can save costs.
Sb has a strong promoting effect on the formation of pearlite. Adding 0.025%sb can make the pearlite in the matrix of grey cast iron reach above 90%w. Melting will not increase the white tendency of gray cast iron, which is similar to Sn and Cu. In grey cast iron, only 015-0.025% Sb is usually added, which can refine graphite, reduce pearlite lamellar spacing, and improve the strength and hardness of cast iron. However, when the content of Kai is high, it will form a brittle mesophase with iron, which will increase the brittleness of cast iron.
V and Mo are rarely used in the actual production of grey cast iron, but they are also added in a small amount in some special cases. V and Mo are both strong carbide forming elements. During the solidification of cast iron, more component supercooling zones are formed in the molten iron due to the segregation of elements. V can promote the formation of pearlite and refine it, but the effect of Mo on increasing the content of pearlite is limited, and the effect of refining pearlite is stronger.
The reasonable combination of these alloy elements can obviously improve the graphite morphology, size and distribution of grey cast iron, refine the lamellar spacing and increase the content of pearlite in the matrix, and effectively improve the mechanical properties of castings.