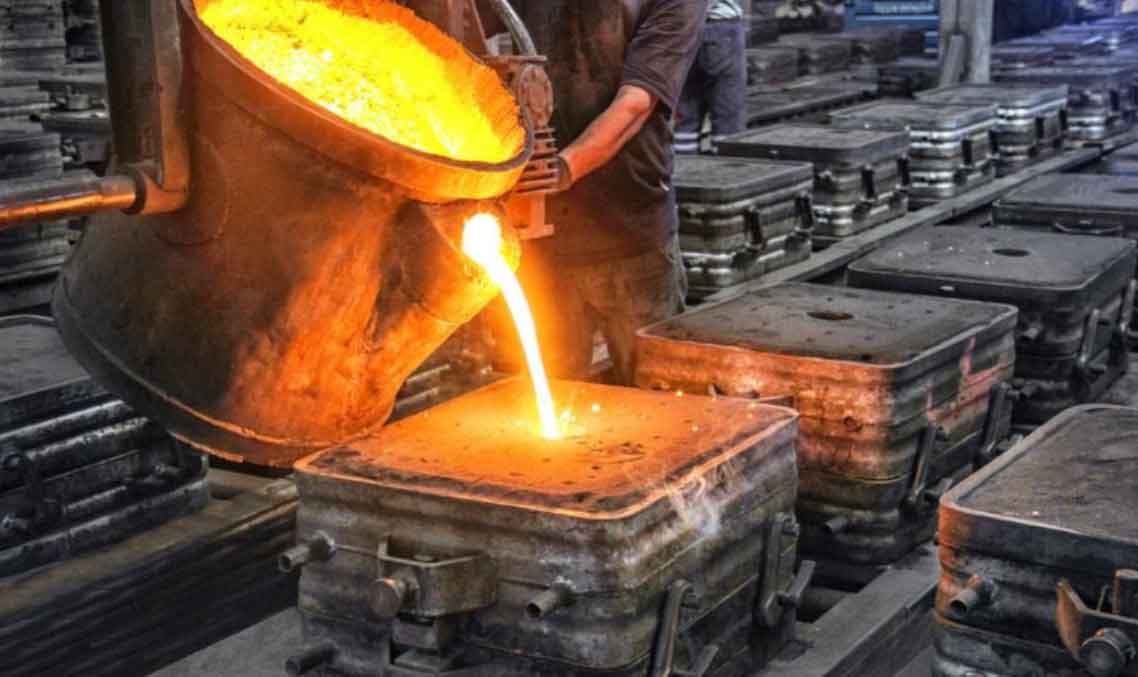
Sand casting offers several advantages that make it an attractive choice for various industrial applications:
- Cost-Effectiveness: Sand casting is a cost-effective method for producing complex shapes and large parts, making it suitable for industrial applications that require large quantities of components. The materials used in sand casting, such as sand and mold binders, are relatively inexpensive, making the process economical for mass production.
- Versatility: Sand casting is highly versatile and can accommodate a wide range of materials, including ferrous and non-ferrous metals, as well as alloys. This flexibility allows for the production of components with varying mechanical properties, ensuring that they meet the specific requirements of different industrial applications.
- Complex Geometries: Sand casting can create intricate and complex shapes with high precision. The use of sand molds allows for the production of components with undercuts, internal cavities, and intricate details that might be challenging to achieve using other casting methods.
- Minimal Material Waste: Sand casting produces minimal material waste since excess sand can be reclaimed and reused for future molds. This sustainable aspect of sand casting aligns with the growing emphasis on environmentally friendly manufacturing practices.
- Rapid Prototyping: Sand casting is an excellent method for rapid prototyping and iterative design changes. With relatively short lead times, designers and engineers can quickly produce prototypes and test the functionality and form of the component before committing to large-scale production.
- Large Component Size: Sand casting can accommodate large-scale components, such as engine blocks, wind turbine components, and industrial machinery parts. This capability makes it ideal for heavy machinery and equipment used in industrial applications.
- Heat Resistance and Mechanical Properties: Cast components can exhibit excellent heat resistance and mechanical properties, depending on the material used. This is crucial for applications in industries like aerospace, automotive, and power generation, where components are subjected to extreme conditions and high stresses.
- Quick Production Turnaround: The sand casting process allows for relatively quick production turnaround times, making it suitable for time-sensitive industrial applications that require fast component production.
- Proven Technology: Sand casting is a well-established and time-tested casting process that has been used for centuries. As a result, the process is reliable and widely adopted in various industries, ensuring confidence in its ability to deliver quality components.
The advantages of sand casting, including cost-effectiveness, versatility, precision, and rapid production, have made it a prevalent manufacturing method across diverse industrial sectors, ranging from automotive and aerospace to construction and heavy machinery. By leveraging the efficiency and precision of sand casting, manufacturers can produce high-quality components to meet the demands of modern industrial applications.