Engineering complexities in the fabrication of large steel castings involve a range of challenges, each requiring specialized knowledge and technology to overcome. Some of the key complexities include:
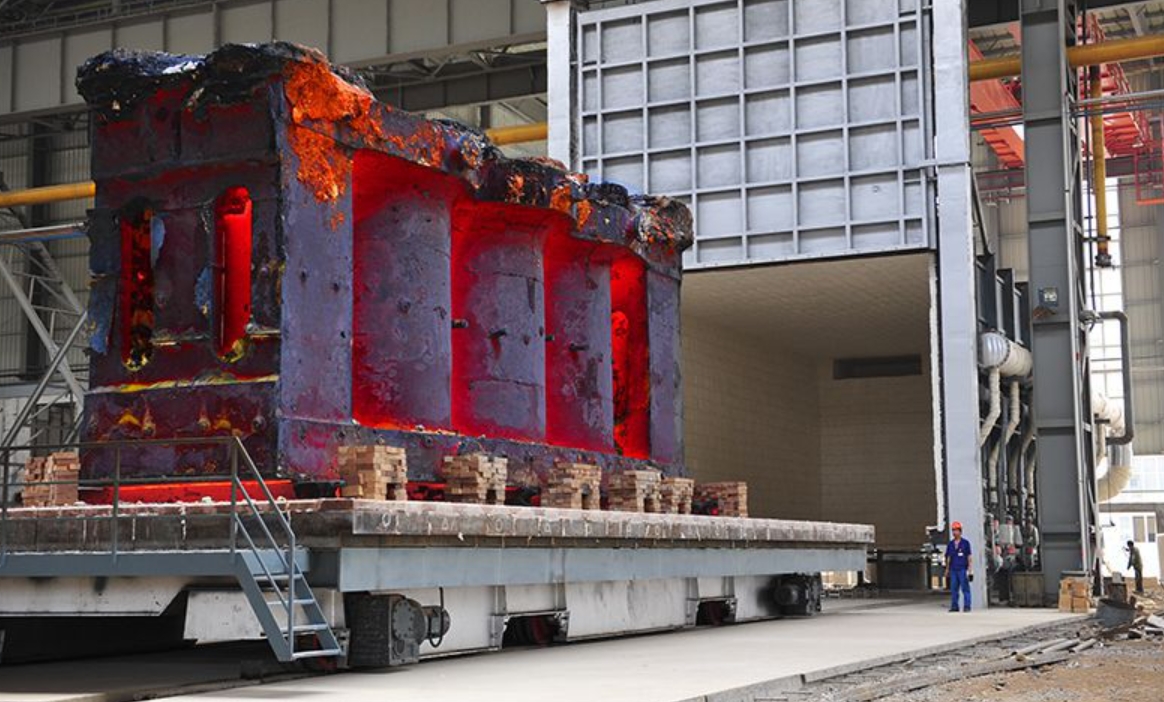
- Material Selection: Choosing the right steel composition is crucial for the casting’s intended use. The alloy must have the appropriate strength, toughness, and resistance to wear, corrosion, or heat, depending on the application.
- Design Challenges: Large castings require precise design to ensure structural integrity. This includes considerations for shrinkage, thermal expansion, and stress distribution to avoid defects like warping or cracking.
- Mold Making: For large castings, creating a mold that accurately reflects the design, maintains its shape during casting, and can be removed afterwards, is a complex task. The mold material and design are critical to the casting’s success.
- Melting and Pouring: Melting large quantities of steel and maintaining the correct temperature and composition throughout the pour is challenging. The pouring process must be controlled to minimize turbulence and prevent defects like porosity or inclusions.
- Solidification Control: Managing how the steel cools and solidifies is vital to prevent internal stresses and structural weaknesses. Techniques like directional solidification and controlled cooling are often used.
- Heat Treatment: Large steel castings usually require heat treatment to achieve desired mechanical properties. Uniformly treating a large casting without introducing stresses or distortions is a complex process.
- Quality Control and Inspection: Non-destructive testing (NDT) methods like ultrasonic testing, radiography, and magnetic particle inspection are essential to detect any internal or surface defects. However, inspecting large castings thoroughly is time-consuming and technically demanding.
- Machining and Finishing: Large castings often require extensive machining to achieve the final dimensions and surface finishes. Handling and machining such large and heavy components pose significant challenges.
- Handling and Transportation: The sheer size and weight of large steel castings make handling and transportation a complex logistical challenge, requiring specialized equipment and planning.
- Environmental and Safety Concerns: Ensuring environmental compliance and worker safety during the casting of large steel components is also a significant challenge, given the high temperatures and heavy materials involved.
Overcoming these complexities often requires a combination of advanced technology, skilled workforce, meticulous planning, and strict adherence to quality and safety standards. The ability to successfully fabricate large steel castings is a testament to the engineering and technological capabilities of a manufacturing facility.