The sand casting process of lining plate castings was simulated and analyzed using ProCAST numerical simulation software. Due to the use of one box with two pieces, the left and right parts are approximately symmetrical. To improve the accuracy of numerical simulation operations by increasing the number of volume grids divided into the model, and to avoid significant increases in computational complexity, a symmetry plane is set in the middle of the model, which uses half of the model for simulation analysis. The distribution of flow field, temperature field, and shrinkage porosity is shown in Figures 1-3.
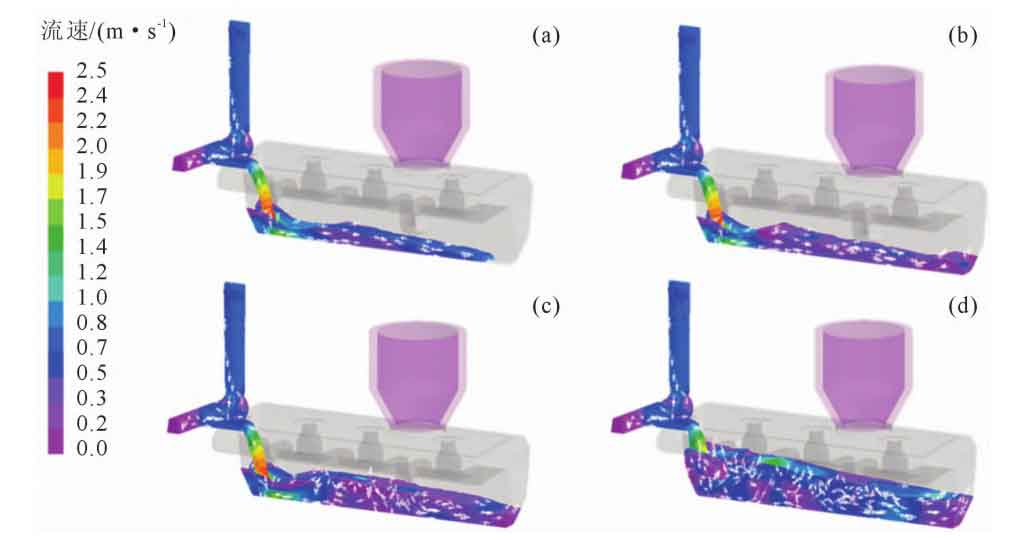
Figure 1a shows the rapid and stable flow of molten metal into the mold cavity through the pouring system. When the molten metal approaches the end of the mold, the flow rate of the molten metal is 0.5-0.7m/s. Afterwards, there was a slight collision between the molten metal and the end of the mold, and the magnitude and direction of its velocity vector changed as shown in Figure 1b. Subsequently, the metal liquid undergoes reflux, but the stratification of the liquid flow is not obvious as shown in Figure 1c. During the filling process, the flow of the metal liquid inside the mold tends to be generally smooth, with no disturbance on the free liquid surface. The liquid surface steadily rises until the filling is completed, effectively avoiding oxidation inclusions caused by the disturbance and turbulence of the metal liquid in the mold cavity, as shown in Figure 1d.
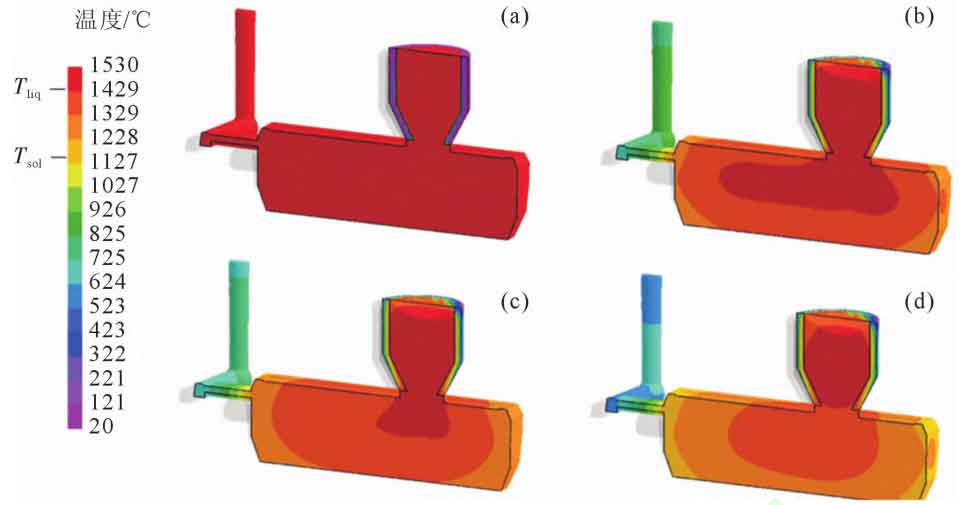
The temperature change during the solidification process of sand castings is shown in Figure 1. At the end of 75 seconds of filling, the temperature at various parts of the lining plate is higher than the liquidus temperature. There is no cold insulation or insufficient pouring inside the sand castings. At the same time, the heating riser is ignited by the high-temperature metal liquid and begins to release heat, as shown in Figure 2a. As the cooling time increases, the lining sand casting gradually solidifies from the edge to the thicker part of the center, and the solid content gradually increases. The liquid phase area that has not solidified in the sand casting gradually shrinks towards the heating riser, while the metal liquid in the heating riser continues to be in liquid state due to heat acquisition, as shown in Figures 2b-c. When cooled to 7 130 seconds, the liquid phase area that has not solidified in the sand casting basically shrinks to the inside of the heating riser. The center of the heating riser is the highest temperature part. During the subsequent cooling and solidification process, the inside of the heating riser will become the final solidification area of the mold cavity, as shown in Figure 2d. The metal liquid inside the mold solidifies sequentially from the end of the mold cavity to the heating riser. Through this solidification sequence, the heating riser can continuously provide liquid compensation for the liquid shrinkage and condensation shrinkage of sand castings. At the same time, it also ensures that the sand casting is always under positive pressure during the solidification process. When the shrinkage is completed, there is still a certain amount of remaining metal hydraulic head in the riser. Based on this, it can be inferred that as the solidification process progresses, shrinkage and porosity will ultimately form in the pouring system and riser. When the negative pressure sand box cools to 2.5×10’s, the temperature of each part of the lining sand casting is below 1107 ℃.
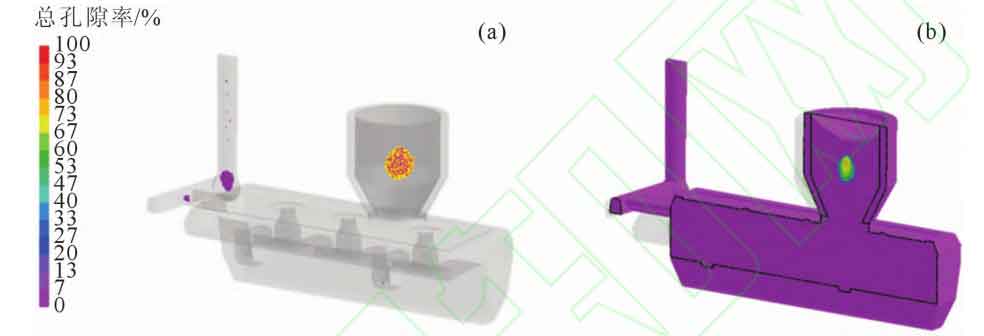
The highlighted yellow area in Figure 3a shows shrinkage porosity and shrinkage defects with an internal porosity greater than 1% in the heating riser, while no shrinkage porosity or shrinkage porosity greater than 1% occurs in the sand casting of the lining plate.
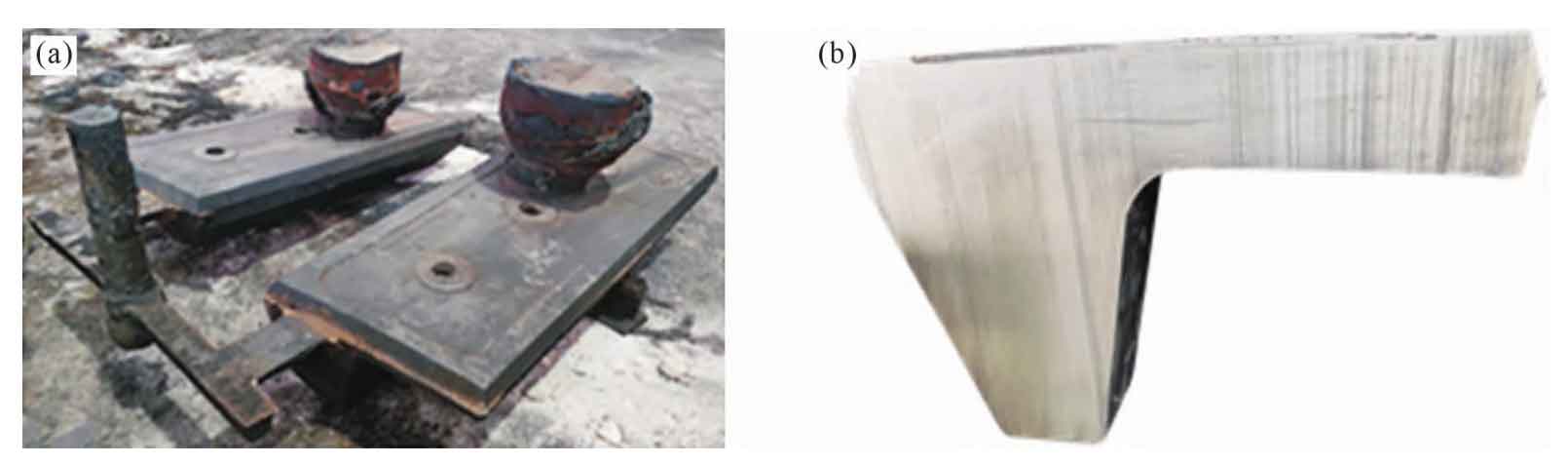
In order to fully verify the sand casting process design scheme, the factory has conducted multiple production trials on this, and the production rate of the lining sand casting process produced is all above 85%. The lining sand casting and its representative cross-section are shown in Figure 4. After careful inspection, no casting defects such as shrinkage, porosity, porosity, and slag inclusion were found in the sand casting.
(1) This article presents a numerical simulation of the original casting process for the liner plate of a semi-automatic mill in a sand casting plant. The distribution and size of internal shrinkage porosity and shrinkage defects in the liner plate were accurately predicted. The cause of this was the blockage of the feeding channel between the riser and the sand casting during solidification cooling, and the formation of an isolated liquid phase zone in the central area of the sand casting. In the subsequent cooling process, due to the liquid shrinkage and solidification shrinkage that occurred in the isolated liquid phase zone, which could not be compensated by foreign metal liquid, shrinkage porosity and shrinkage defects eventually occurred inside the lining lifting strip.
(2) A new design for the sand casting process of the lining plate was carried out using the “Intelligent Design of Casting Process (Cast Steel)” software independently developed based on Basic language. PrOCAST numerical simulation showed that during the solidification and cooling process of the sand casting, the feeding channel between the riser and the sand casting remained unobstructed until the casting was fully solidified, and the internal part of the heating riser became the last solidified part of the metal liquid in the mold cavity. Shrinkage and porosity defects are mainly distributed inside the pouring system and heating riser, and the structure of the lining sand casting is dense.
(3) Multiple production tests have shown that the representative cross-section of the lining sand casting does not exhibit shrinkage or porosity defects. Through simulation and experimental verification, the sand casting process design scheme has successfully eliminated the internal shrinkage and porosity defects of the lining plate sand casting, and increased the process yield of the lining plate sand casting from 65% to over 85%, providing a new idea for the sand casting process design of the lining plate casting in the sand casting plant.