Abstract: This article focuses on the development of the shell forming process for engineering jacket sets in vacuum lost foam casting. It begins with an introduction to the importance of the wheel-side jacket set as a crucial safety component in vehicle systems and the quality issues faced in its production using the traditional lost foam casting process. The article then delves into various experimental processes aimed at reducing or eliminating EPS white pattern materials before pouring, including pre-ignition before pouring, burning before pouring, and shell forming processes. After a detailed comparison, the vacuum negative pressure shell forming process is determined to be the optimal solution. This process not only forms a cavity without EPS pattern materials before pouring but also isolates sand and water, enhancing the filling and solidification feeding abilities of the liquid metal under vacuum conditions. The article further elaborates on the implementation details of this optimized process, covering aspects such as EPS foam white pattern production, modification and reinforcement, shell making, boxing and pouring, cleaning, and detection verification. The final results show that this process effectively improves product quality, reduces overall costs, and has significant practical application value.
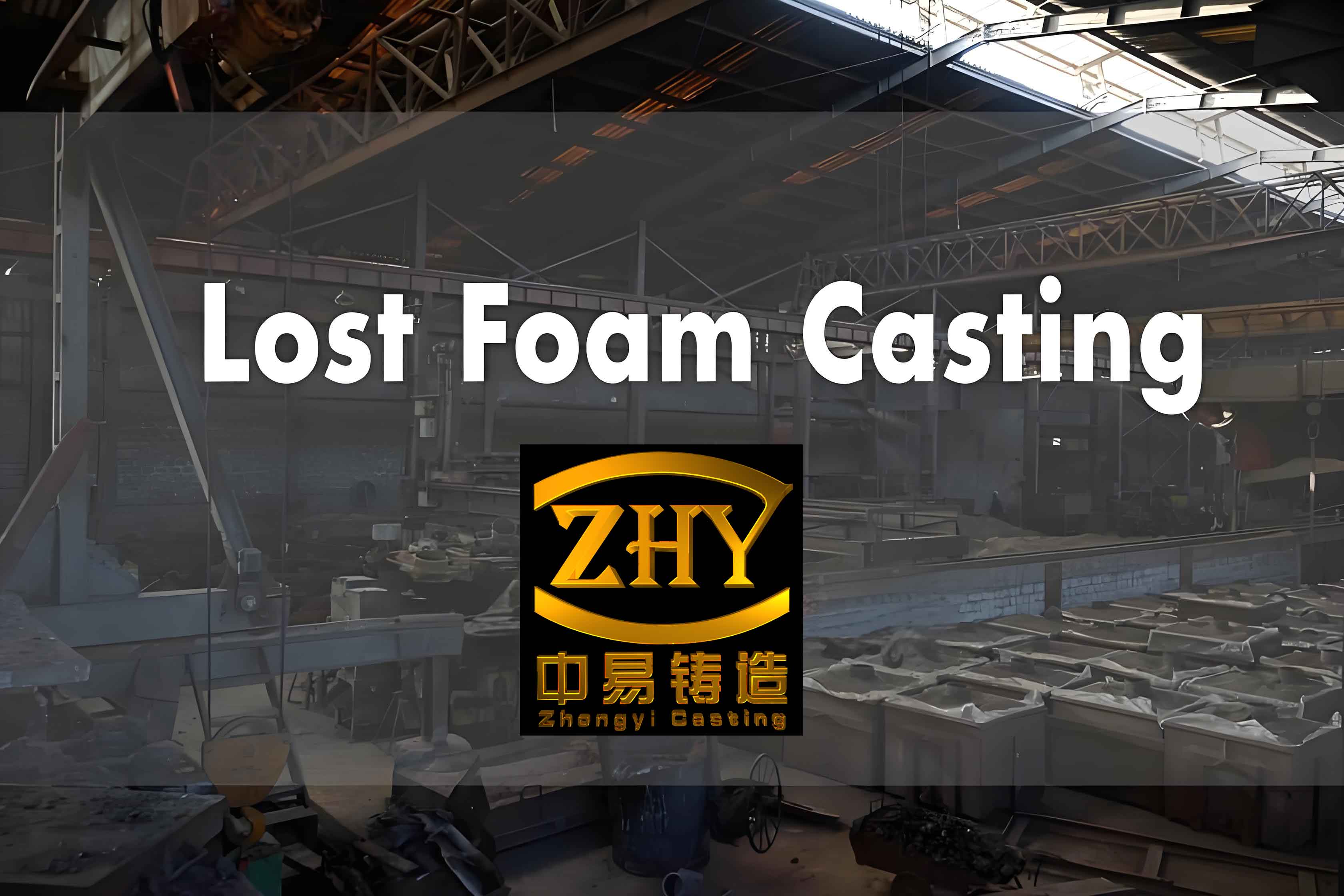
1. Introduction
The wheel-side jacket set, also known as the wheel-side reducer shell, is a vital safety component in the driving systems of heavy-duty trucks and engineering vehicles. Due to its importance, high requirements are imposed on its mechanical and operational properties, as well as on its material and internal quality. The material of this product is QT550 – 06, and its structure is a hollow cylindrical thin-walled part with a flange, having a height-to-diameter ratio ≥ 1.15 and an average wall thickness of 10 – 15 mm. Generally, both the inner and outer surfaces are fully machined.
Traditionally, the lost foam casting process using EPS materials has been employed for the production of this wheel-side jacket set. However, in actual production, quality defects such as slag holes and air holes frequently occur. Given that the product requires full machining of both inner and outer surfaces, the rejection rate due to these defects once reached 15% – 30%, leading to strong customer complaints.
2. Analysis of Lost Foam Casting Process
In the typical lost foam casting process, several factors contribute to various defects. The gasification and decomposition process of the EPS white pattern during pouring generates viscous asphalt re-polymers, foamed plastic gas emission, microscopic immersion and fusion of carbon and iron in the gasification atmosphere, vacuum negative pressure, coating performance, and specific operations. The combined influence of these factors results in defects such as carbon slag inclusions, air holes, carbon increase, wrinkling, and even collapse of the mold box and sand sticking.
To address these quality defects in the wheel-side jacket set production and fully utilize the advantages of the process, a solution approach was devised to reduce or remove the EPS white pattern material as much as possible before pouring. This led to the experimentation with different processes: pre-ignition before pouring, burning before pouring, and shell forming process. The aim was to create a forming cavity without EPS pattern material before pouring, isolate sand and water, and improve the environment for forming. By leveraging vacuum negative pressure or vibration physical conditions, the filling and solidification feeding abilities of the liquid metal could be enhanced, thereby resolving the aforementioned defects.
3. Experiments on New Forming Processes Based on Removing EPS White Pattern Material
3.1 Pre-ignition Before Pouring
The pre-ignition before pouring process involves igniting the EPS white pattern from the gate before pouring. Under the suction of vacuum negative pressure, the EPS foam plastic burns a certain distance into the mold from the gate, and then pouring is carried out immediately. This process was developed through years of practical experience in lost foam casting enterprises.
The method utilizes the lost foam coating to form an isolated space, burning part of the EPS white pattern in the cavity before pouring as much as possible. This reduces the gas emission and liquid phase re-polymer generated after the white pattern decomposes during pouring. With the help of vacuum negative pressure physical conditions, the filling and solidification feeding abilities of the liquid metal are improved, creating a favorable forming environment. This has led to a certain reduction in the rejection rate due to slag inclusions, air holes, and wrinkling.
However, it should be noted that this method can only burn part of the EPS white pattern near the gate and inside the cavity. Due to the lack of oxygen deeper in the cavity, the burning gradually stops. Therefore, although this method can significantly improve the defects, it cannot completely solve all the casting defects.
3.2 Burning Before Pouring
The burning before pouring process refers to the process of fully burning the EPS white pattern under oxygen blowing conditions before pouring the liquid metal. Compared with the pre-ignition method that cannot fully burn the white pattern in the cavity, this process can completely burn the EPS white pattern in the cavity under sufficient oxygen blowing conditions, thereby eliminating and reducing defects such as carbon defects, slag inclusions, and air holes.
The key to this process lies in the “burning” step. Firstly, the coating used must have sufficient high-temperature resistance and strength. Secondly, factors such as vacuum negative pressure, coating thickness and permeability, whether the coating is fully covered, coating cracks, and sand mold airtightness need to be well controlled. Since the process involves burying the mold cluster in dry sand and then starting to enrich and blow oxygen to burn the EPS white pattern, if these conditions are not coordinated, it is easy to cause mold collapse.
This process also utilizes the lost foam coating to form an isolated space. By burning the EPS white pattern in the cavity before pouring under oxygen-rich (or forced oxygen blowing) conditions, there is no white pattern left in the cavity during pouring. With the help of vacuum negative pressure physical conditions, the filling and solidification feeding abilities of the liquid metal are improved, creating a favorable forming environment and solving the rejection rate due to slag inclusions, air holes, and wrinkling.
In actual production, although the EPS white pattern in the cavity is burned under oxygen-rich (or forced oxygen blowing) conditions before pouring, due to the structure of the wheel-side jacket set determining the cavity structure, there are still phenomena or problems such as incomplete burning, insufficient burning, and non-through burning. Under the suction of vacuum negative pressure, there is an obvious wall-attaching phenomenon. The gelatinous re-polymer after the white pattern melts and re-solidifies can be flushed and carried to the top of the cavity or the riser by the injected liquid metal. Therefore, this process is not suitable for thin-walled castings but is more suitable for thick-walled castings. However, for thick-walled castings, the problem of mold collapse still needs to be paid special attention to.
3.3 Shell Forming
The shell forming process combines lost foam casting with investment casting shell-making technology. Its main feature is to produce independent shells offline. Specifically, a higher-density EPS white pattern of the wheel-side jacket set is first formed by foaming. Then, several layers of inorganic slurry are coated on both sides. After drying and multi-stage roasting to remove the EPS white pattern, a “shell” with high strength, good permeability, clean inner wall, and complete contour is produced. This shell is then buried in ceramsite sand, compacted under negative pressure, and the liquid metal is poured under vacuum conditions to obtain a precise metal casting with a dense structure and a smooth appearance.
This lost foam shell forming casting technology coats the foam pattern with slurry to make a shell and removes the EPS white pattern before pouring to avoid quality defects such as slag holes and air holes caused by the decomposition of the EPS white pattern during pouring. This process is different from investment casting in that the produced shell can be made with or without sand scattering.
After comparing the pre-ignition before pouring, burning before pouring, and shell forming processes for the wheel-side jacket set, due to the shell forming process having the advantages of thoroughly removing the EPS white pattern material, significantly improving product quality, and facilitating flexible production organization by making shells offline, the vacuum negative pressure lost foam shell forming process was finally determined as the optimal solution.
4. Implementation of Vacuum Negative Pressure Lost Foam Shell Forming Process Optimization Scheme
4.1 EPS Foam White Pattern
EPS (polystyrene foam plastic) has good filling and forming properties, good surface quality, requires a small initial investment in molds, and has a fast development cycle. According to the structure of the wheel-side jacket set and the requirements for appearance quality, an EPS foam white pattern is adopted. A foaming forming mold is developed, and considering the subsequent quality requirements for almost full machining, the EPS white pattern is designed as a whole structure.
4.2 Modification, Anti-deformation Reinforcement, and Bonding of Pouring System
For the EPS white pattern of the wheel-side jacket set produced by foaming, if there are surface defects such as pits, missing parts, or bumps, surface modification is carried out using modification paste or agents. At the flange opening, a “cross” -shaped anti-deformation reinforcement is made. According to the material of the wheel-side jacket set (QT550 – 06), its hollow, flanged, and thin-walled structure characteristics, and considering the influence of the product structure on the flow and filling of sand under the condition of appropriately increasing the vacuum negative pressure, a top injection process with two symmetric inner gates injecting upward is designed, following the usual lost foam process. After the process is determined, the pouring system is bonded to form a white pattern cluster as a whole mold.
4.3 Shell Making
After the completion of the white pattern cluster mold of the wheel-side jacket set, the shell is made by dipping, brushing, or a combination of both to coat the slurry. This shell precision forming process borrows from the investment casting shell-making process and further optimizes it by improving the sand scattering shell-making method of investment casting to a method suitable for EPS white patterns, which is to coat several layers of inorganic slurry on both sides. The steps of shell making are as follows:
Step | Description |
---|---|
1 | Mix and prepare the inorganic slurry for the front and back layers, and stir the slurry evenly. |
2 | Coat the EPS white pattern cluster of the bonding pouring and feeding system with 1 layer of front layer slurry first, and dry it at a low temperature of 35 – 65°C. |
3 | Coat 3 – 4 layers of back layer slurry, sprinkle sand between layers to increase thickness (or use a non-sand scattering slurry shell-making method), and dry it at a low temperature in turn. |
4 | At this time, the initial shell contains an EPS white pattern. Drill a discharge hole at an appropriate part at the bottom of the shell with the gate facing down. |
5 | Place the shell with the gate facing down in the furnace and heat and roast it in multiple stages (medium temperature 150 – 300°C, high temperature 650 – 850°C) to produce a complete empty shell with strength and permeability meeting the requirements and a clean inner cavity. |
6 | Use refractory cotton to dip and coat the slurry to close the discharge hole. |
7 | Use a plastic film to tie the pouring gate. |
4.4 Boxing and Pouring
The wheel-side jacket set shell with the pouring gate tied with a plastic film is buried in ceramsite sand. The bottom sand is laid and vibrated to be flat and compact. The shell is firmly supported and placed vertically. When adding sand, especially for the inner cavity, dead corners, and shadow areas that are not easily compacted by negative pressure, the sand is filled in place until it is level with the upper surface of the sand box. At the same time, three-dimensional vibration is carried out for compaction. A plastic film is laid to cover the upper opening of the sand box, and a certain thickness of dry sand is laid on top to press and protect the plastic film.
The sand box filled with sand and shaped is placed in the pouring area. Before pouring, the plastic film tied at the pouring gate is cut open. The negative pressure valve is opened for negative pressure compaction. When the negative pressure vacuum degree reaches 0.03 – 0.05Mpa, the liquid metal of nodular cast iron is poured. After seeing the liquid metal at the pouring gate solidify, the negative pressure is closed and the vacuum is removed.
4.5 Cleaning
The wheel-side jacket set casting is kept in the sand box for 2 – 2.5 hours for heat preservation. After cooling to below 200°C, the sand is removed and the casting is taken out of the box. After the casting cools, the pouring system and slag collection bag are removed. After shot blasting and sand blasting cleaning, a complete casting is further cleaned up.
4.6 Detection Verification
The wheel-side jacket set produced by the vacuum negative pressure shell forming process optimization scheme has been tested through dissection, machining, and batch production verification. There are no slag holes or air holes quality defects, and the yield has been greatly increased. At the same time, due to the vacuum adsorption effect and the chilling effect of the pouring cavity of thin-walled parts, the filling and solidification feeding abilities of the liquid metal during pouring are enhanced, the internal structure of the product is dense, and the shrinkage cavity and porosity defects are effectively solved. The product has passed customer size inspection, mechanical property inspection, flaw detection and dissection detection, and surface quality inspection.
Although the material cost of making the shell in this vacuum negative pressure shell forming process optimization scheme is slightly increased, due to the increase in the yield and process output rate, the overall cost is reduced. Moreover, making shells offline facilitates flexible organization of production and can be accepted by actual production, having industrialization promotion and application value.
5. Conclusion
The wheel-side jacket set adopts the vacuum negative pressure shell forming process optimization scheme. By removing the EPS pattern material before pouring and making a shell without EPS pattern material, the filling and solidification feeding abilities of the liquid metal are enhanced under vacuum conditions. This fully utilizes the combined advantages of lost foam casting and investment casting, solves the quality defects such as slag holes and air holes that frequently occur in the production process, significantly improves product quality, reduces the overall cost, and has flexible organization of production by making shells offline. This process has a fast development cycle, stable control of vacuum negative pressure physical conditions, not only improves product quality but also uses binder-free spherical sand that can be recycled, which is environmentally friendly and has significant comprehensive benefits.