Enhancing casting quality requires implementing effective measures to minimize defects throughout the casting process. Here are some key measures that can help achieve this goal:
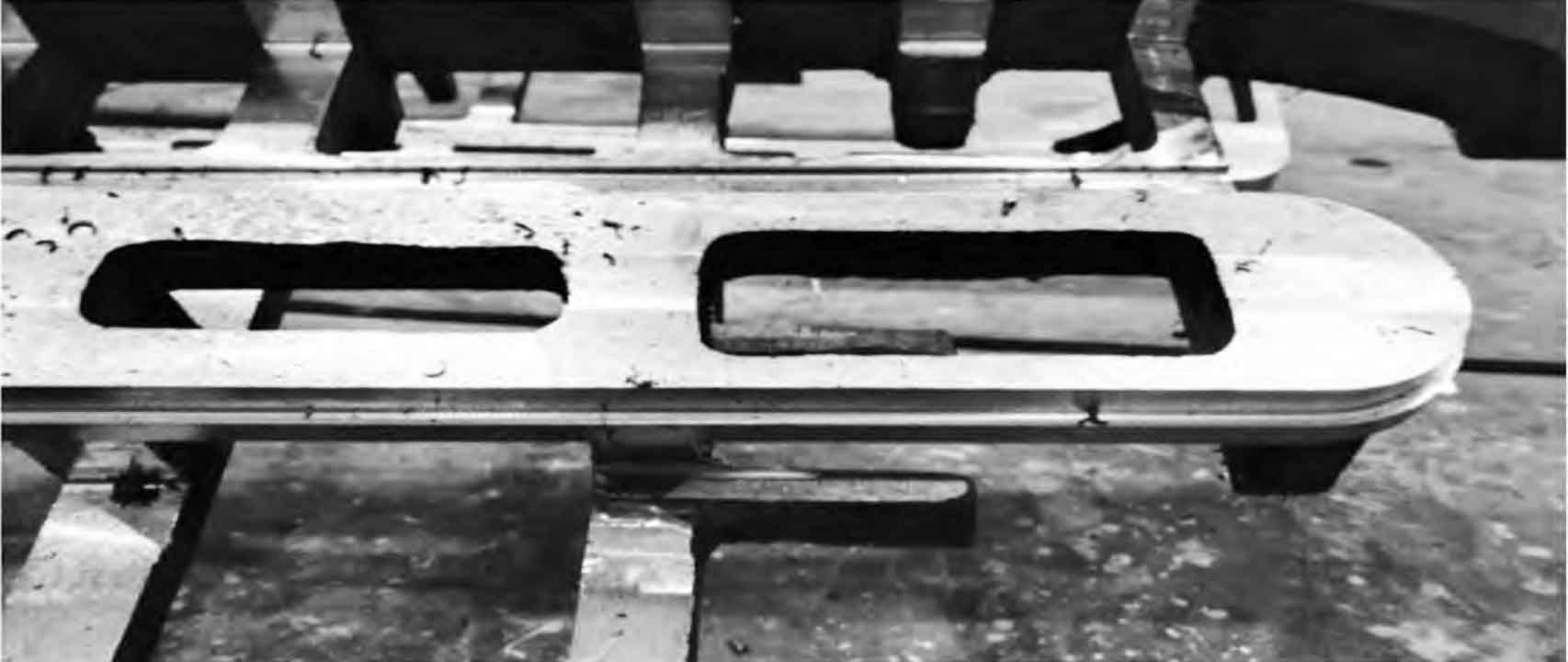
- Robust Process Control:
- Establish standardized operating procedures and work instructions to ensure consistency in the casting process.
- Monitor and control critical process parameters such as temperature, pouring rate, mold preparation, and solidification time.
- Implement real-time process monitoring systems to detect deviations and take corrective actions promptly.
- Proper Gating and Riser Design:
- Optimize gating and riser design to facilitate smooth metal flow, minimize turbulence, and ensure uniform solidification.
- Use computer simulation software to analyze and optimize gating and riser systems for improved filling patterns, reduced defects, and efficient use of molten metal.
- Quality Raw Materials:
- Work with reputable material suppliers to ensure consistent and high-quality raw materials.
- Perform regular material testing and inspection to verify compliance with specifications.
- Control the quality of additives, fluxes, and mold materials to prevent contamination and maintain casting integrity.
- Effective Mold Preparation:
- Implement rigorous mold preparation procedures, including proper cleaning, coating, and drying techniques.
- Ensure appropriate mold surface finish and texture to minimize defects and improve mold release.
- Use suitable mold coatings, refractories, and parting agents to protect against metal/mold interactions and ensure smooth casting surfaces.
- Process Optimization:
- Utilize computer-aided engineering (CAE) tools and simulation software to optimize casting parameters and predict potential defects.
- Analyze the solidification behavior, cooling rates, and shrinkage characteristics of the casting to identify potential issues and make process adjustments accordingly.
- Quality Control and Inspection:
- Establish comprehensive quality control procedures and inspection protocols to detect defects at various stages of the casting process.
- Implement visual inspection, non-destructive testing (NDT), and dimensional analysis techniques to identify and quantify defects.
- Conduct regular inspection and testing of incoming materials, during casting, and post-casting to ensure compliance with quality standards.
- Training and Skill Development:
- Provide training programs for operators, technicians, and engineers involved in the casting process to enhance their knowledge and skills.
- Promote a culture of quality awareness, emphasizing the importance of defect prevention and continuous improvement.
- Encourage cross-functional collaboration and knowledge sharing to leverage expertise and identify innovative solutions.
- Continuous Improvement:
- Establish a systematic approach to continuous improvement, such as Lean Manufacturing or Six Sigma methodologies.
- Conduct regular defect analysis, root cause investigations, and implement corrective and preventive actions (CAPA) to address underlying issues.
- Set up performance metrics and conduct regular audits to track progress and ensure sustained improvement.
By implementing these effective measures, manufacturers can minimize casting defects, improve overall casting quality, and enhance product performance and reliability. It is essential to foster a culture of quality throughout the organization and ensure active participation and commitment from all stakeholders involved in the casting process.