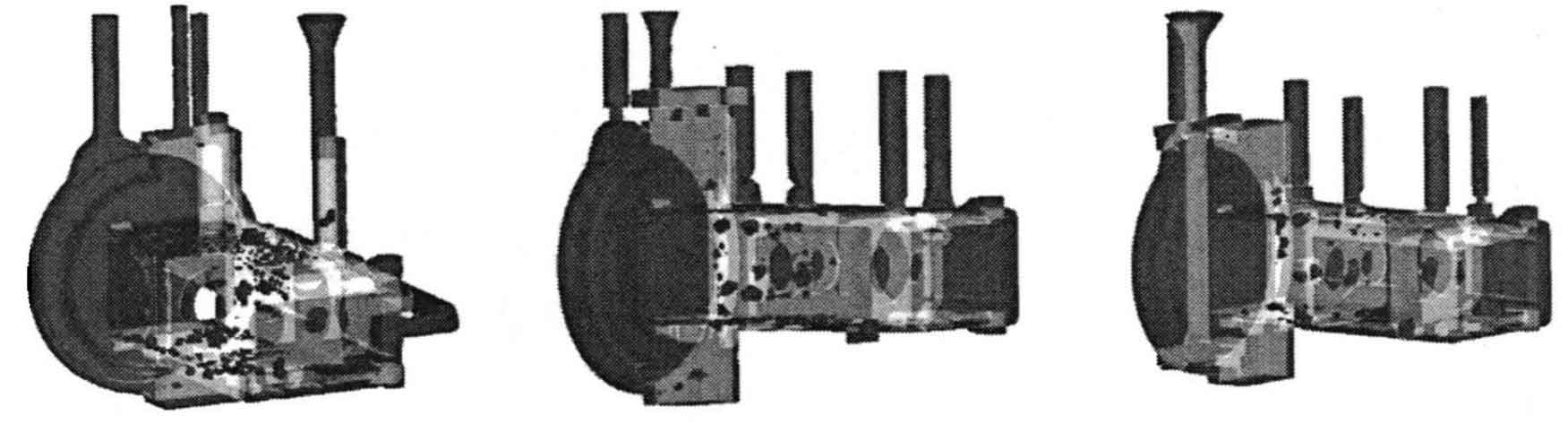
Casting shrinkage is a critical phenomenon that occurs during the solidification process of cast metals. It refers to the reduction in volume and size of the casting as it cools and solidifies. While some shrinkage is inevitable, excessive shrinkage can have a significant impact on the mechanical properties and structural integrity of cast components. This article explores the implications of casting shrinkage on the mechanical properties and structural integrity of castings.
- Dimensional Accuracy: Casting shrinkage can result in dimensional deviations from the intended design. Excessive shrinkage can lead to undersized or distorted castings, compromising the dimensional accuracy required for proper fit and function. This can affect the overall performance and reliability of the component.
- Residual Stress: Shrinkage-induced residual stresses can develop within the casting during solidification. These stresses can result in cracking, distortion, or even failure of the casting. Residual stresses can significantly reduce the fatigue life and load-bearing capacity of the component, compromising its structural integrity.
- Porosity and Inclusions: Shrinkage can create voids and porosity within the casting, particularly in regions with complex geometries or where molten metal feeding is inadequate. These porosities can act as stress concentration points and reduce the overall strength and ductility of the material. Inclusions or trapped gases can also form during shrinkage, further compromising the mechanical properties of the casting.
- Mechanical Strength: Excessive shrinkage can negatively affect the mechanical strength of castings. It can lead to decreased tensile, compressive, and impact strength, reducing the load-bearing capacity and structural integrity of the component. The presence of shrinkage-related defects such as microporosity or shrinkage cavities further exacerbates the reduction in mechanical strength.
- Surface Finish: Shrinkage defects such as shrinkage cavities or surface depressions can mar the surface finish of the casting. This can affect the functionality, aesthetics, and even the corrosion resistance of the component. Smooth surface finish is particularly crucial for applications where contact or sliding occurs between mating surfaces.
- Heat Transfer: Shrinkage-related defects can also affect the heat transfer characteristics of the casting. Irregularities in the casting’s geometry and localized porosity can disrupt the flow of heat, resulting in uneven temperature distribution and thermal gradients. This can lead to thermal stresses, dimensional instability, and reduced thermal efficiency of the component.
Addressing the implications of casting shrinkage on mechanical properties and structural integrity requires a comprehensive approach:
- Process Optimization: Optimizing casting parameters such as gating design, riser placement, mold material, and cooling rates can help minimize shrinkage defects and maintain dimensional accuracy.
- Quality Control: Implementing rigorous quality control measures, such as non-destructive testing and inspection techniques, can detect shrinkage-related defects early on and prevent their propagation.
- Material Selection: Choosing suitable casting alloys and ensuring proper metallurgical treatment can enhance the material’s resistance to shrinkage and improve its mechanical properties.
- Heat Treatment: Post-casting heat treatment processes like stress-relieving or annealing can help alleviate residual stresses and improve the mechanical properties of the casting.
- Simulation and Modeling: Utilizing advanced simulation tools can help predict and mitigate shrinkage-related issues during the design phase, allowing for optimization of the casting process and minimizing the risk of structural integrity concerns.
In summary, casting shrinkage can significantly impact the mechanical properties and structural integrity of cast components. By understanding the implications and implementing appropriate measures to minimize shrinkage defects, foundries can produce castings with improved dimensional accuracy, enhanced mechanical strength, and superior structural integrity. This ensures that the cast components meet the required performance and reliability standards for their intended applications.