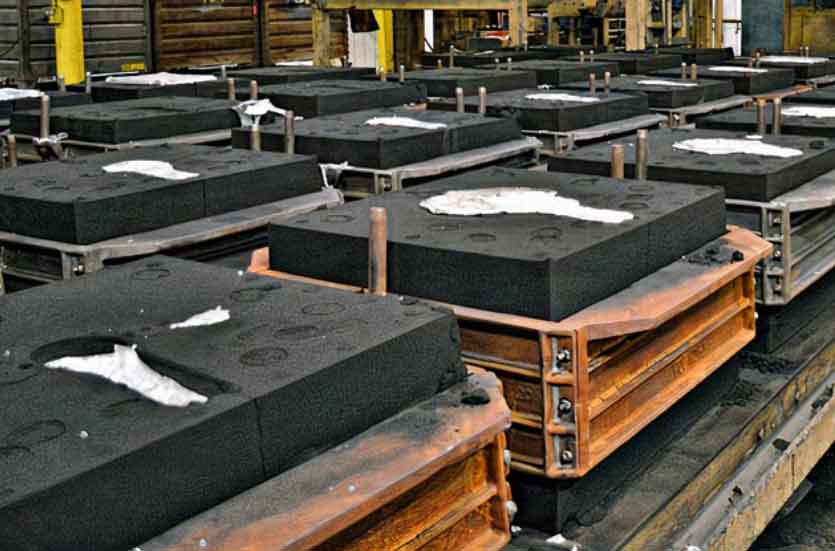
Enhancing productivity is a key goal in resin sand casting, and there are several techniques and best practices that can help achieve this objective. By optimizing various aspects of the process, manufacturers can improve efficiency, reduce costs, and increase output. Let’s explore some of these techniques and best practices for enhancing productivity in resin sand casting:
1. Efficient Mold Design:
Optimizing the mold design is crucial for productivity. Utilize advanced CAD and CAE software to design molds that minimize material usage, reduce the number of mold sections, and facilitate efficient filling and solidification of the metal. Consider the gating and risering system design to ensure proper metal flow and minimize the occurrence of defects. Efficient mold design contributes to faster mold preparation and improved casting quality.
2. Automated Mold Handling:
Implementing automation in mold handling can significantly improve productivity. Automated systems can handle tasks such as mold assembly, mold transportation, and mold flipping, reducing manual labor and saving time. These systems can be integrated with robotic arms, conveyor belts, or gantry systems to streamline the mold handling process and increase overall efficiency.
3. Optimized Sand Mixing:
Efficient sand mixing is essential for resin sand casting. Use well-calibrated sand mixing equipment to achieve consistent sand-to-resin ratios. Proper mixing ensures uniform sand distribution and adequate resin coverage, resulting in high-quality molds. Additionally, automate the sand mixing process to ensure accurate and repeatable mixtures, reducing variations and improving overall productivity.
4. Real-Time Process Monitoring:
Implementing real-time process monitoring systems allows for immediate detection of deviations or issues during resin sand casting. Utilize sensors to monitor critical parameters such as temperature, pressure, and flow rate. These sensors can provide real-time data, which can be analyzed to detect anomalies and make necessary adjustments promptly. By identifying and addressing issues early, productivity can be improved, and the occurrence of defects can be minimized.
5. Streamlined Casting Operations:
Optimize the casting operations to reduce cycle times and improve productivity. Proper coordination between mold preparation, metal pouring, solidification, and mold breakout is crucial. Minimize waiting times between different stages of the process to ensure a smooth flow of production. Additionally, consider batch processing for similar parts to maximize efficiency and minimize setup times.
6. Skilled Workforce and Training:
Invest in skilled workers and provide comprehensive training on resin sand casting techniques. Well-trained operators can perform tasks efficiently and effectively, reducing errors and minimizing downtime. Continuous training and knowledge sharing can help workers stay updated with the latest advancements and best practices, further enhancing productivity.
7. Continuous Improvement and Process Optimization:
Embrace a culture of continuous improvement and process optimization. Regularly review the resin sand casting process, identify bottlenecks or inefficiencies, and implement corrective actions. Analyze data, monitor key performance indicators, and utilize process improvement methodologies such as Lean or Six Sigma to streamline operations, reduce waste, and enhance productivity.
8. Collaboration with Suppliers and Partners:
Collaborate closely with material suppliers, pattern makers, and other partners in the casting process. Work together to identify opportunities for improvement, share best practices, and explore innovative solutions. Building strong relationships and open communication channels with suppliers and partners can lead to optimized material selection, reduced lead times, and enhanced overall productivity.
By implementing these techniques and best practices, manufacturers can enhance productivity in resin sand casting. The focus on efficient mold design, automation, process monitoring, streamlined operations, skilled workforce, continuous improvement, and collaboration can result in increased output, improved quality, and reduced costs, ultimately driving success in resin sand casting operations.