With the rapid development of the global manufacturing industry, the foundry industry, as an important foundation and one of the main industries of the manufacturing industry, has also been comprehensively improved. Based on the planning, design and intelligent application of modern foundry, this paper expounds how to build a smart factory with adaptability and high resource efficiency, and focuses on the content of mechanized molding process of green sand.
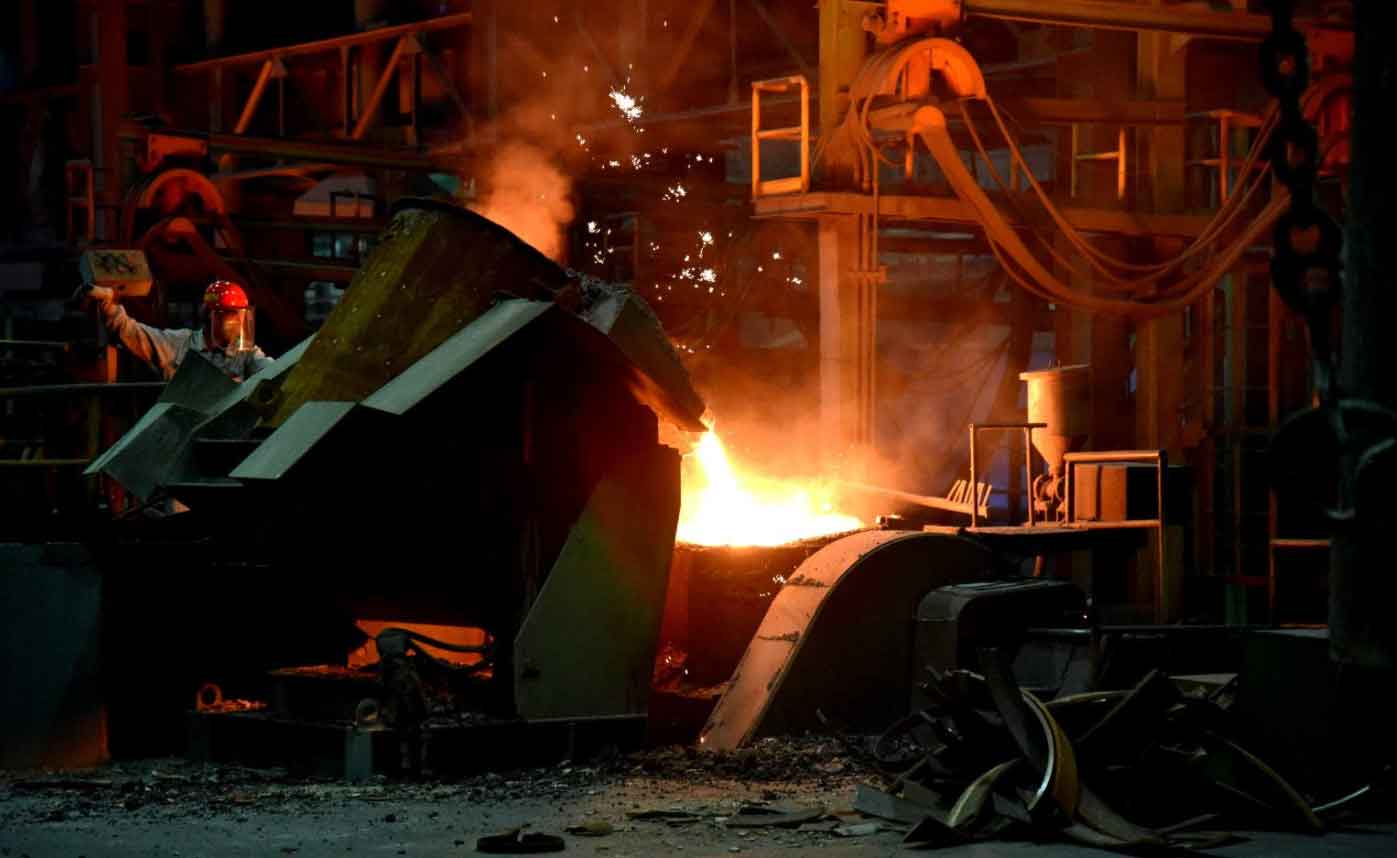
Industry 4.0 aims to use the IOT information system to digitize and intelligentize the supply, manufacturing and sales information in production, and finally achieve rapid, effective and personalized product supply. Therefore, a modern foundry should be built on the basis of having a smooth logistics production chain, data-based production information and intelligent process.
The construction of a foundry should produce more near net shape castings at the lowest possible cost on the premise of meeting the environmental protection requirements. This paper does not focus on the basic issues such as equipment selection for production capacity matching and the stability of production rhythm in the design of foundry factory. What is emphasized here is the organic integration of smooth logistics production chain and production information digitization in foundry factory under industry 4.0. The casting products produced by the casting factory can be roughly divided into two categories: one is a single product of pure casting (also including parts after machining), and the other is a semi-finished product assembled into parts. The mo of castings can be roughly divided into order type and inventory type, that is, the production of castings is completed according to the market order or inventory quantity.
1. Order production
In order production, most of them adopt flow logistics production chain. For foundry factories of this nature, the production task is basically determined by the orders of downstream factories, and rarely directly faces the primary market. Therefore, the factory adopts the near zero inventory production mode, that is, the production task is completed according to the order. For example, when a task order is to produce 10000 products, the foundry can assign specific production tasks to the workshop according to the general yield of the product. However, when the casting workshop completes the production task list, if the production capacity is affected by the molding or pouring problems of a single mold, the production line can automatically supplement the mold number through manual intervention to make up for the shortage caused by production defects and complete the production task. This is a preliminary application of modern factory data and intelligence.
2. Inventory production
Most of the inventory production uses the warehousing logistics production chain. If the products of the casting factory are relatively standard general products, such as various pipes (accessories), the factory can issue a full (quarterly) annual production order according to the market demand of the products, and the production order of the whole factory is completed by the central three-dimensional warehouse. The central three-dimensional warehouse records all the product information of the factory, and can automatically coordinate the work content of each process of the product according to the inventory status. The shuttle trolley (RGV or AGV) completes the transfer and storage of products between each production process and the central warehouse.
No matter what production mode is adopted, the production of foundry shall meet the organic integration of smooth logistics production chain and production information digitization. The establishment and production of modern foundry should try to reduce logistics detours and manual participation, so as to realize the non landing of castings and the single piece of product information, and finally realize intelligent casting production.