Bucket teeth are critical excavator casting parts mounted on the front edge of excavator buckets, functioning as cantilever components subjected to bending moments and intense impact-abrasive wear during rock, ore, and soil excavation. This article comprehensively analyzes wear mechanisms and material selection strategies for these essential excavator casting parts.
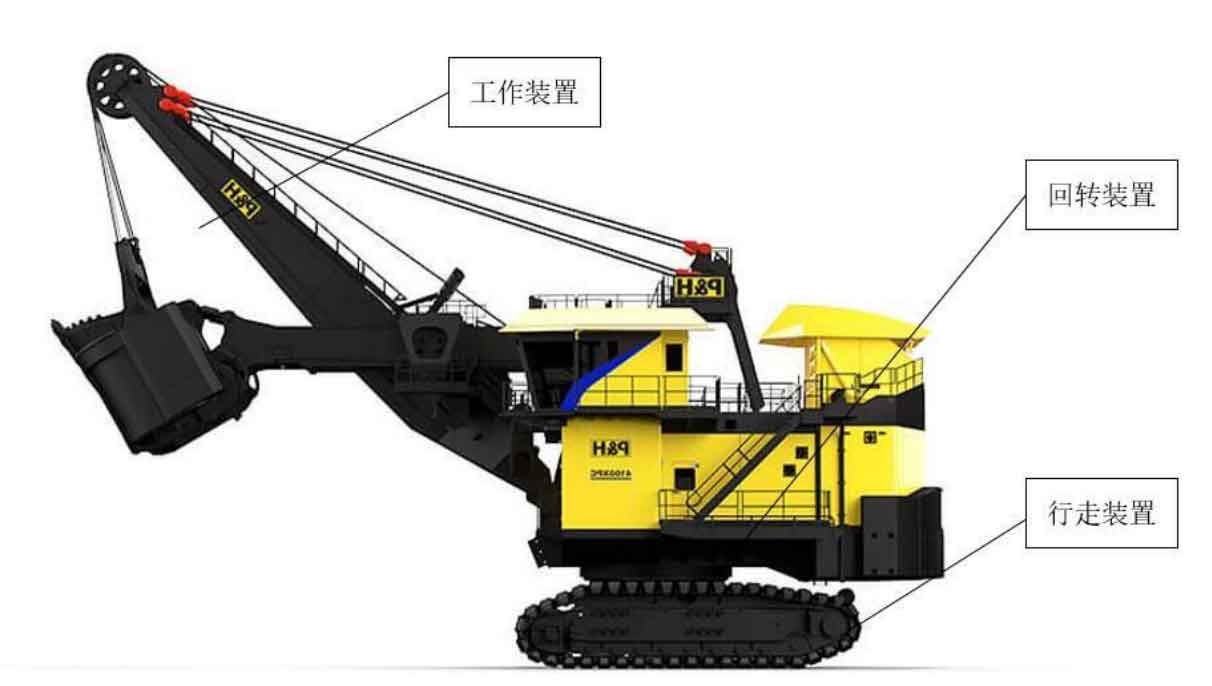
Wear Mechanisms
Primary wear mechanisms governing excavator casting part degradation include:
1. Cutting Mechanism: Under high-impact loading, abrasive particles penetrate the tooth surface when material hardness is lower than the excavated medium. This generates micro-cutting chips and plastic deformation grooves, described by the specific wear rate $W_s$:
$$W_s = \frac{k \cdot P \cdot v}{H}$$
where $k$ is the wear coefficient, $P$ is contact pressure, $v$ is sliding velocity, and $H$ is material hardness. Heat generation from deformation ($Q_d$) and friction ($Q_f$) causes localized temperatures exceeding 500°C, inducing dynamic recrystallization and phase transformations.
2. Fatigue Spalling Mechanism: Cyclic loading generates subsurface cracks that propagate according to Paris’ law:
$$\frac{da}{dN} = C \cdot (\Delta K)^m$$
where $da/dN$ is crack growth rate, $\Delta K$ is stress intensity factor range, and $C$, $m$ are material constants. Repeated stress cycles cause material fragmentation into flat flakes with radial cracks.
Mechanism | Dominance (%) | Material Response |
---|---|---|
Cutting | 70-80 | Increased hardness enhances resistance |
Fatigue Spalling | 20-30 | Requires optimal hardness-toughness balance |
Material Selection for Excavator Casting Parts
1. Austenitic Manganese Steels
Standard Hadfield steel (ZGMMn13) remains prevalent for excavator casting parts due to exceptional work hardening:
$$H = H_0 + K \cdot \epsilon^n$$
where $H_0$ is initial hardness (180-240 HB), $K$ is strengthening coefficient, $\epsilon$ is strain, and $n$ is work hardening exponent (~0.5). Composition optimization is critical:
Element | Function | Optimal Range (wt.%) |
---|---|---|
C | Wear resistance ↑ | 0.9-1.2 |
Mn | Stabilizes austenite | 10-15 |
P | Crack initiation ↓ | <0.05 |
Alloyed grades (e.g., ZGMMn13Cr2) enhance excavator casting part performance:
$$H_{max} = 380-400\ HB \ (\text{after explosive hardening})$$
Ultra-high Mn steels (16-22% Mn) demonstrate superior strain hardening for massive excavator casting parts under extreme impact.
2. Low Alloy Steels
Preferred for hydraulic excavator casting parts due to balanced hardness-toughness. Key systems include Mn-Cr and Si-Mn-Cr-Mo alloys. Heat treatment dictates microstructure:
Quenching & Tempering: Achieves tempered martensite with hardness-toughness trade-off:
$$K_{IC} \propto \frac{C}{H^{3/2}}$$
where $K_{IC}$ is fracture toughness and $C$ is a material constant.
Isothermal Quenching: Produces carbide-free bainite (BF + AR). A representative composition:
C | Cr | Mo | Hardness (HRC) | Impact (J/cm²) |
---|---|---|---|---|
0.25-0.30 | 1.8-2.2 | 0.35-0.45 | 49.5 | 85-100 |
3. White Cast Irons
Used in low-impact excavator casting parts. High-Cr irons (Cr15) offer optimal carbide morphology:
$$V_C = \frac{\%C \cdot \rho_{Fe}}{\%C \cdot \rho_{Fe} + \%Cr \cdot \rho_{Cr}/6.97}$$
where $V_C$ is carbide volume fraction, $\rho$ denotes density. Property variations with carbon content:
Cr15 Grade | C (wt.%) | Hardness (HRC) | Fracture Toughness (MPa·m½) |
---|---|---|---|
Low-C | 2.0-2.5 | 55-58 | 18-22 |
High-C | 3.0-3.6 | 62-65 | 12-15 |
4. Composite Structures
Hybrid designs enhance excavator casting part economics and performance:
Cast-in Inserts: High-Cr iron tips (HV 1200-1600) embedded in Mn-steel bases increase service life 2.4×.
Hardfacing: Laser-deposited Cr-Mo alloys create metallurgically bonded layers with hardness gradients:
$$H(y) = H_0 + (H_s – H_0) \cdot e^{-ky}$$
where $H_s$ is surface hardness, $y$ is depth, and $k$ is attenuation coefficient.
Performance Enhancement Strategies
Extending excavator casting part longevity requires integrated approaches:
1. Composition Optimization: Computational thermodynamics guides alloy design:
$$\Delta G = \Delta H – T\Delta S < 0 \ (\text{for stable carbide formation})$$
2. Advanced Processing: Directional solidification reduces defects in critical excavator casting part sections:
$$G/R > \frac{\Delta T}{D_L}$$
where $G$ is thermal gradient, $R$ is solidification rate, $\Delta T$ is freezing range, and $D_L$ is liquid diffusivity.
3. Differential Heat Treatment: Tailored phase transformations across tooth geometry:
Tooth Region | Target Microstructure | Treatment |
---|---|---|
Tip | Martensite + Carbides | Water-jet quenching |
Root | Lower Bainite | Step-quenching at 300°C |
4. Ceramic-Reinforced Composites: TiC/WC particles (15-30 vol.%) in steel matrices yield hardness exceeding 800 HV.
Conclusion
Optimal excavator casting part performance requires synergistic consideration of wear mechanisms and material properties. High-Mn steels remain indispensable for high-impact conditions, while advanced low-alloy steels offer superior hardness-toughness balance for hydraulic applications. Composite designs and localized hardening provide the next frontier for extending service life. Continuous innovation in computational alloy design, defect-controlled processing, and functionally graded treatments will further enhance these critical excavator components.