As shown in the figure, the die structure of squeeze casting includes upper and lower die, die base, die core, secondary extrusion forming punch, slag collecting ladle, exhaust channel, injection hammer head and ejection mechanism, and die cooling and temperature measuring hole. The structural characteristics of the vertical semi-solid extrusion die are as follows:
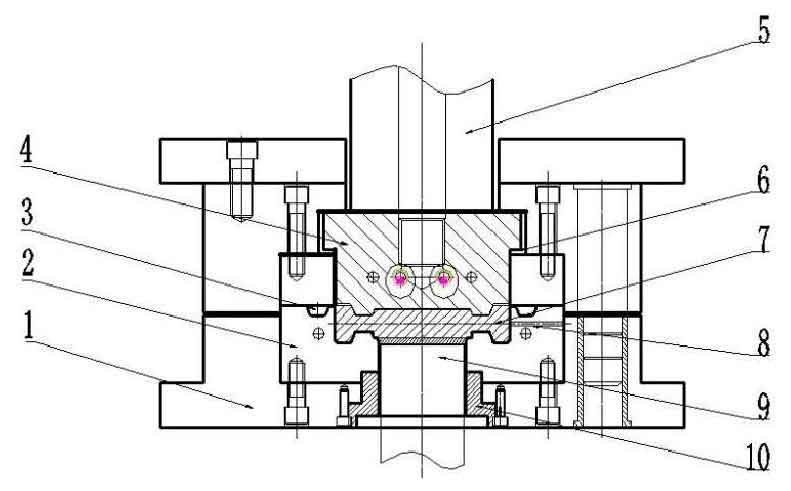
(1) Injection hammer head
The injection hammer head is fixed in the barrel of the injection mechanism and connected with the piston of the injection cylinder. After the barrel is butted with the gate sleeve of the lower die base, the injection program is started, and the injection cylinder pushes the injection hammer to press the metal liquid in the barrel into the mold cavity. There is a certain amount of material cake between the injection hammer head and the forming workpiece. The bottom-up injection design is conducive to exhaust, avoid the air in the pressure chamber getting involved in the liquid metal, and improve the quality of squeeze casting parts.
(2) Secondary cavity extrusion (forging) forming punch
One end is fixed on the top extrusion cylinder, and the other end is directly connected with the upper die. After the injection molding, a certain cooling time is set according to the cooling experimental data, and then the secondary extrusion program is started. The extrusion (closing) cylinder pushes the punch to extrude the upper die, and the secondary extrusion molding is carried out on the workpiece, which achieves a certain forging effect. The maximum reduction is generally controlled within 3 ~ 5mm, and it is directly extruded to the upper die. The whole workpiece is extruded twice, and the forming effect can be guaranteed.
(3) Die cavity structure
The bottom of the die is designed with a large gate, and the liquid metal is injected into the die cavity from bottom to top for forming. A number of slag collecting ladles and exhaust channels are evenly arranged at the edge of the formed part to avoid excessive splashing and entrapment of liquid metal in the injection process, which is conducive to mold filling and solidification feeding of liquid metal. The design of mold cavity is based on the principle of local quality. Because the liquid metal directly impacts the upper mold cavity during squeeze casting, it is easy to cause damage in the form of welding, impact and so on, so the upper mold is designed with a core insert. In this way, if the upper die insert is damaged, just replace the insert. The die cavity and insert are made of H13 hot working die steel with high strength and toughness.