1. As cast microstructure

The microstructure of the experimental steel as cast is shown in Figure 1 (a, b), which is composed of a ferrite matrix and a large number of small granular carbides distributed on it. The spacing between adjacent grain boundaries is 20-40 μ M. Under scanning electron microscopy (see Figure 1 (c, d)), granular or short strip carbides can be observed on the ferrite matrix structure, with some short strip carbides connected into chains. The EDS results (see Figure 2) also showed that the carbides with short rod-shaped shapes along the grain boundaries were rich in C, Cr, and Fe elements, and mainly contained M23 C6 phase, corresponding to (Cr, Fe) 23C6 carbides with varying sizes and uneven distribution. The matrix contained a large amount of smaller and denser particle like M23C6 phase. The ferrite as the matrix phase is at high temperature δ- The rapid cooling of ferrite is due to the high chromium content in GX40CrSi17 heat-resistant steel. Chromium, as a stabilizing element for ferrite, promotes the formation of ferrite.
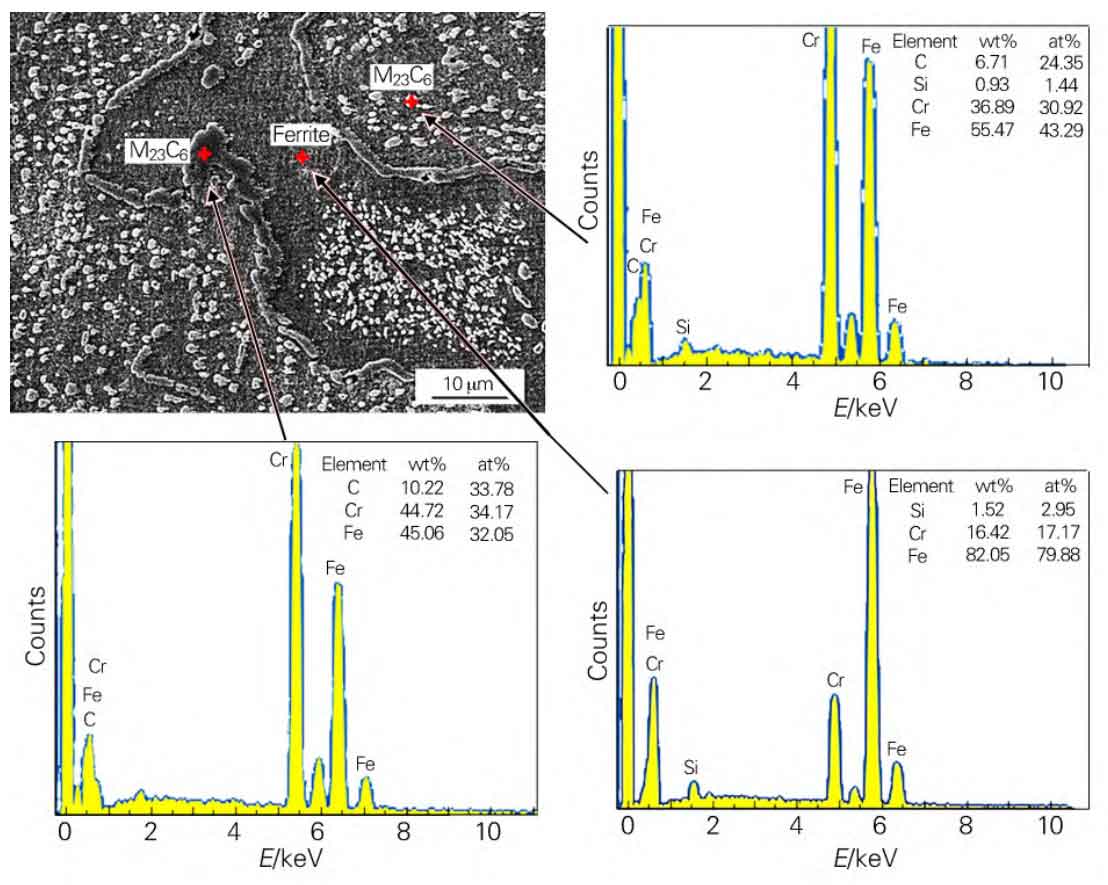
2. Thermodynamic simulation
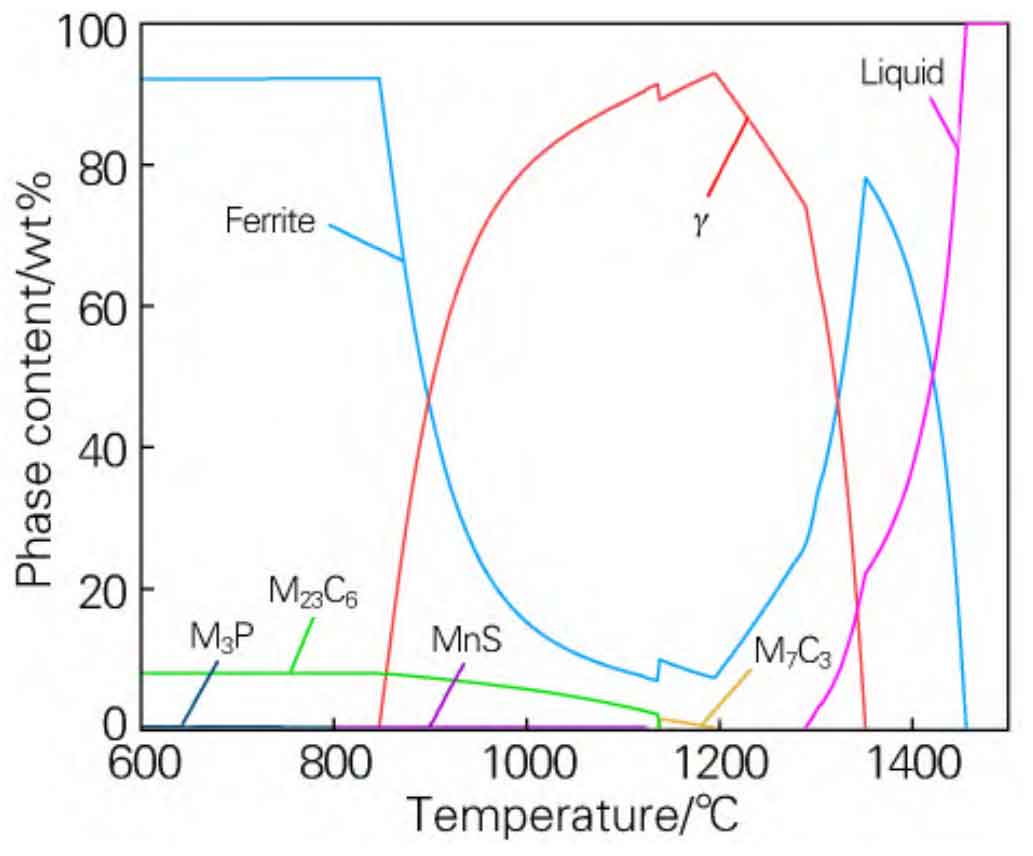
According to the chemical composition in Table 1, an equilibrium phase diagram was simulated within the temperature range of 600-1500 ℃ (see Figure 3). It can be seen that the melting point of the steel used in this experiment is 1459 ℃, which crystallizes from the liquid phase as the temperature decreases δ- Ferrite, and at 1354 ℃ δ The maximum amount reached 78.06%. In solids with temperatures below 1290 ℃, ferrite mainly exists (above 1200 ℃) δ- Ferrite, M23 C6 type carbides, austenite, etc. When the temperature exceeds 1200 ℃, the austenite content significantly decreases, and the matrix structure gradually transforms into δ- Ferrite phase; The austenite content reaches its maximum at a temperature of 1197 ℃, approximately 92.94%; When the temperature is below 1140 ℃, M23C6 type carbides appear, and their content decreases with increasing temperature. At 840 ℃, the highest M23C6 content is about 7.73%. The content and chemical composition of these phases within the range of 850~1050 ℃ are listed in Table 2. M23 C6 is mainly composed of alloy carbides composed of Cr, Fe, C elements and a small amount of Ni and Mn elements. With the increase of temperature, the Cr content in M23C6 phase gradually decreases, while the C and Cr content in the matrix phase increases, indicating that some Cr rich carbides dissolve into the matrix phase. As a cast matrix phase, ferrite has almost the same main elements as austenite, and the two phases undergo mutual transformation and content changes with temperature.
Elements | C | Si | Mn | P | S | Cr | Ni | Fe |
Actual measured value | 0.43 | 1.16 | 0.58 | 0.03 | 0.01 | 16.66 | 0.26 | Bal. |
Standard value | 0. 3 ~ 0. 5 | 1. 0 ~ 2. 5 | 0. 5 ~ 1. 0 | ≤ 0. 045 | ≤ 0. 030 | 16. 0 ~ 18. 0 | — | Bal. |
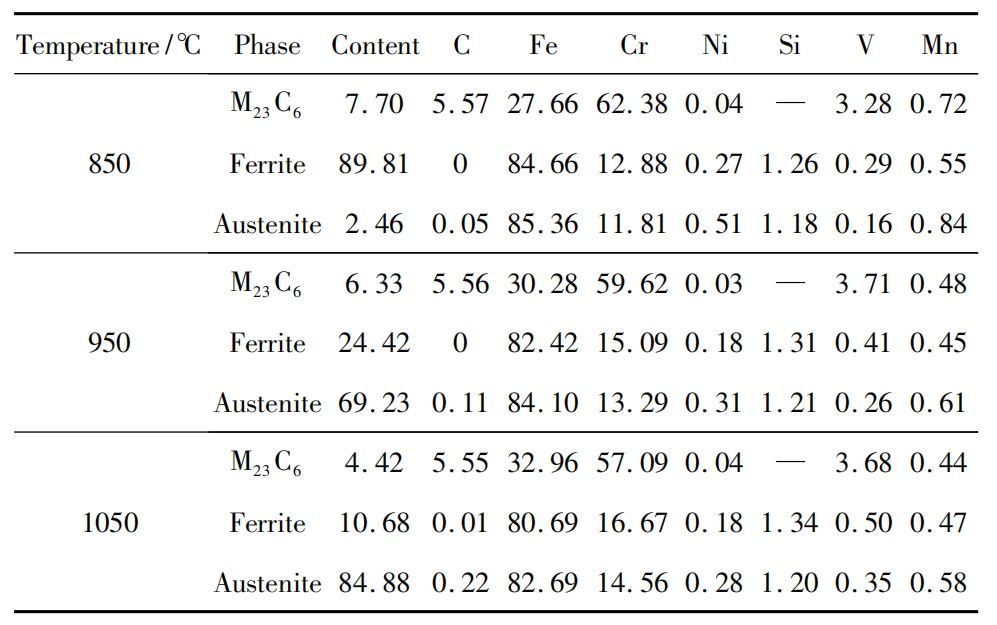
Simulate the variation of the content of the main precipitates with temperature at different temperatures, as shown in Figure 4. There is a certain amount of M23C6 type carbides rich in Cr at 600-1100 ℃, with the highest content at 840 ℃, accounting for about 7.73%. When the temperature rises to above 860 ℃, the content of M23C6 phase begins to decrease, but it can still maintain a content of over 7% at 950 ℃. When the temperature further increases to 1050 ℃, the content of M23C6 phase in the tissue decreases by nearly half, to about 4.2%; When the temperature reaches 1120 ℃, there is no M23 C6 carbide in the tissue, and it is completely dissolved in the matrix. Gola ń Ski et al. [8] conducted microstructure analysis on HR3C heat-resistant steel after long-term service and found that M23C6 improved its tensile strength and creep resistance through precipitation strengthening mechanism during the precipitation process. Given the significant impact of the precipitation of M23C6 type carbides on the high-temperature performance of steel, further research was conducted on the changes in precipitated phases and microstructure at different temperatures through high-temperature aging.
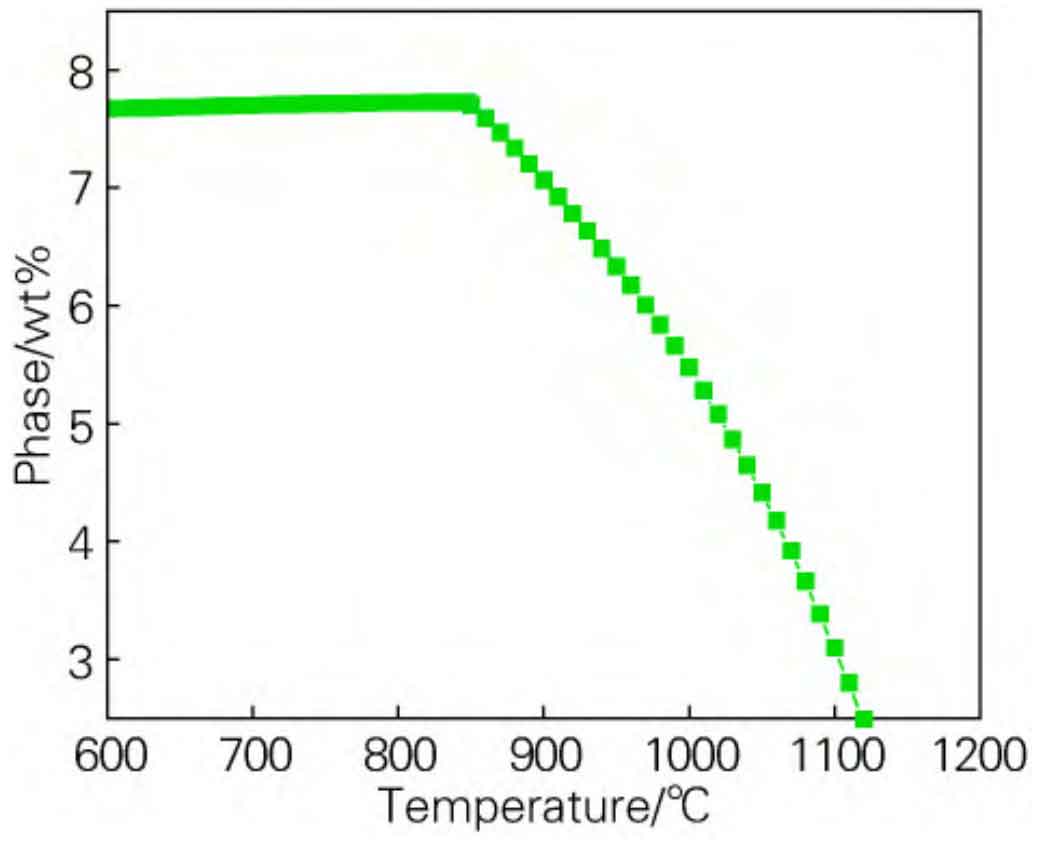
3. Analysis of microstructure after high-temperature aging
3.1 Analysis of Aging Structure at 850 ℃
The OM and SEM images of the sample aged at 850 ℃ are shown in Figure 5. From Figure 5 (a, b), it can be seen that the microstructure is a block like ferrite matrix with a large number of granular carbides distributed. Compared with the as cast structure, the number of intragranular carbides slightly decreases, and the size slightly increases, showing a dispersed distribution and a more uniform distribution. This is due to a portion of smaller sized M23C6 carbides existing in the cast state re dissolving into the ferrite matrix at this temperature. Therefore, compared to the as cast structure, the number of carbides in fine particles decreases significantly and the size increases under aging at 850 ℃, resulting in a more uniform size and distribution of carbides. According to thermodynamic simulation results, during aging at 850 ℃, there are mainly ferrite matrix phases and M23C6 carbides. The EDS results in Figure 6 also indicate that a large number of fine particulate carbides are chromium rich M23C6 type carbides, and the chromium content of carbides on grain boundaries is slightly higher than that of carbides inside the grains, mainly related to the presence of primary carbides at grain boundaries. Due to the similar chemical composition and content of ferrite and austenite, it is difficult to distinguish. However, energy spectrum analysis results show that the gray white area below has a higher Si content than the dark area. According to simulation results, the silicon content in the ferrite phase is slightly higher than that in the austenite phase, suggesting that the gray white area is the ferrite phase zone. The small amount of Si element present in the ferrite phase can refine its grain size and promote the aggregation of granular M23 C6 carbides at grain boundaries, greatly reducing the possibility of dislocation slip.
3.2 Analysis of Aging Structure at 950 ℃
The OM and SEM microstructure of the sample aged at 950 ℃ is shown in Figure 7. Compared with the aged structure at 850 ℃, with the increase of aging temperature, most of the granular carbides in the grains dissolve back, and the quantity is greatly reduced. The carbides near the grain boundaries are still mostly retained. However, intermittent distribution was also observed due to the local dissolution of primary carbides at the grain, with a slight increase in grain size and a tendency for grain boundaries to flatten and develop. The significant reduction in the number of carbides weakened the pinning effect during grain boundary migration. According to thermodynamic simulation results, some ferrite phases undergo transformation at 950 ℃, resulting in an increase in austenite content. The EDS results in Figure 8 further indicate that the composition of the strip like precipitates near the grain boundaries at 950 ℃ is similar to that of the short strip like precipitates at 850 ℃ and the granular precipitates as cast, which are M23C6 carbides with increased size. The mass fractions of elements in the fused parts of carbides are 4.11% C, 0.98% Si, 20.78% Cr, and 74.14% Fe, with slightly higher Cr content than the matrix. Due to the gradual dissolution of intragranular carbides in the matrix, the amount of Cr rich carbides gradually decreases, and the content of Cr element in the matrix slightly increases compared to 850 ℃. At this temperature, atomic diffusion will intensify grain boundary sliding, and a flat grain boundary will have an adverse effect on the persistent strength. In addition, the aggregation and growth of M23C6 will also be detrimental to high-temperature performance. A study has found that in S31042 steel after long-term high-temperature service, the second phase M23C6 continuously aggregates and grows during service. As service time increases, especially the aggregation and growth of M23C6 near grain boundaries can lead to a decrease in high-temperature ductility and failure. The 3W-3Co ferrite blade steel promotes the aggregation of (Cr, W, Co) 23 C6 phases at grain boundaries and intragranular precipitation in the structure at high temperatures, leading to a decrease in plasticity and hardness. These studies all demonstrate the significant influence of M23 C6 carbides on high-temperature performance.
3.3 Analysis of aging microstructure at 1050 ℃
The microstructure morphology of the OM and SEM samples after aging at 1050 ℃ is shown in Figure 9. It can be seen from Figure 9 that as the aging temperature increases to 1050 ℃, most of the chain like and short rod like carbides at the original grain boundaries also dissolve back into the matrix and disappear. The granular M23C6 carbides inside the crystal are almost completely dissolved, and the grain boundaries are more straight, with an increase in grain size. The matrix structure shows two phases with different degrees of corrosion and colors, The dark gray area in the metallographic diagram represents the ferrite phase, while the light gray block like area represents the austenite phase. According to thermodynamic simulation results, at 1050 ℃, the matrix is mainly composed of ferrite and austenite phases, with a very small amount of M23C6 phase remaining. The EDS results in Figure 10 indicate that the elongated precipitates remaining along the grain boundaries are M23 C6 carbides, with the black area being the austenite phase. EDS measurements show a chromium content of 20.28%, and the gray area being the austenite phase, with a chromium content of 17.91%. This indicates that the Cr content in the ferrite phase zone is slightly higher than that in the austenite phase, indicating that the M23 C6 carbides in the original grains have dissolved back into the matrix phase. Comparing the microstructure morphology of Figures 5, 7, and 9, it is not difficult to find that with the increase of effective temperature, the content, morphology, and size of the matrix phase and M23C6 phase in the as cast structure have undergone significant changes.
4. Analysis of hardness changes
The Brinell hardness of GX40CrSi17 steel after aging at different temperatures for 100 hours is shown in Figure 11. The average hardness as cast is 259 HBW. As the aging temperature increases, the hardness value in the aging state shows a decreasing trend. The hardness values in the aging state at 850 ℃ and 950 ℃ are not significantly different. The hardness after aging at 850 ℃ is about 230 HBW, and the hardness after aging at 950 ℃ is 223 HBW. The changes in hardness are related to the content of M23 C6 carbides in the organization and the solubility of matrix carbon and alloy elements. The increase in effective temperature and the prolongation of time lead to an increase in the amount of carbides that dissolve back into the matrix, resulting in a decrease in the amount of M23C6 carbides retained in the original cast state and a decrease in hardness; At the same time, due to the dissolution of some carbides, the content of C and alloy elements in the matrix increases, and the effect of solid solution strengthening will also contribute slightly to the hardness, resulting in little difference in hardness values between the aged states at 850 ℃ and 950 ℃. The aging temperature reached 1050 ℃, and M23 C6 carbides were almost non-existent in the matrix. They all dissolved back into the matrix, resulting in an increase in the content of C and Cr in the matrix phase. Some ferrite transformed into austenite phase, further reducing the hardness to 206 HBW. Therefore, the hardness changes in the aged state at different temperatures are also consistent with the changes in its microstructure.
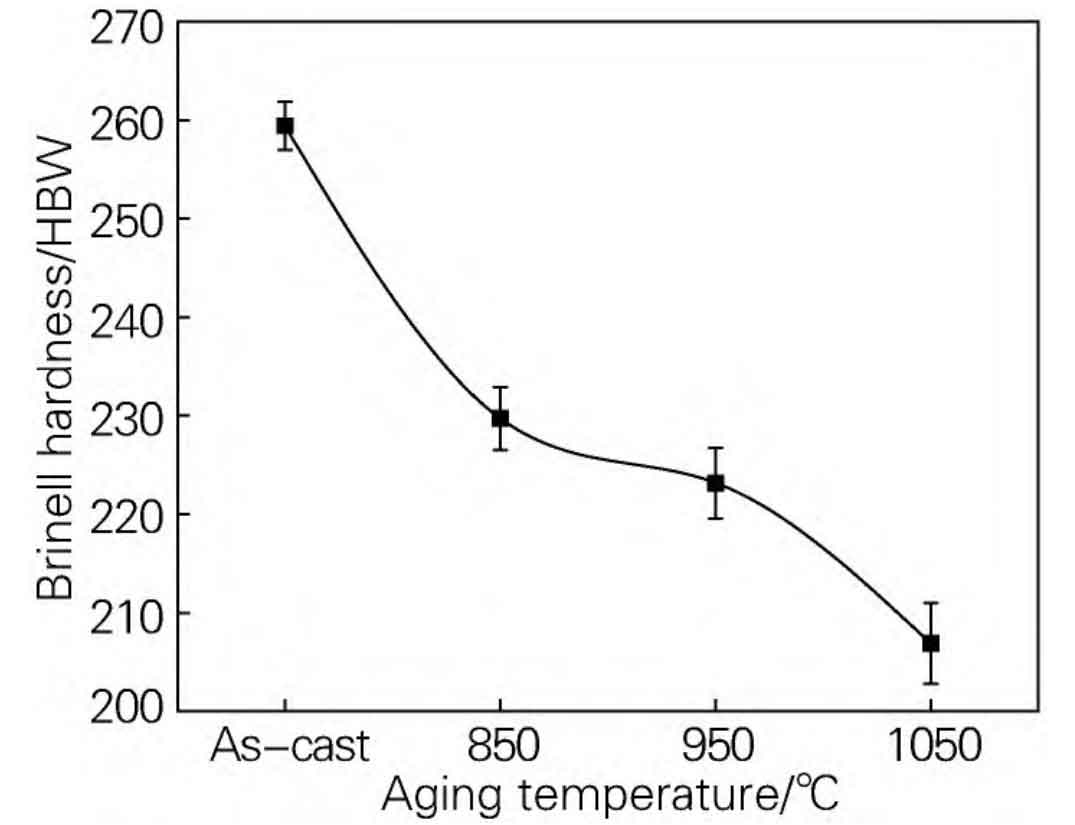
In summary, based on the analysis of microstructure and hardness after high-temperature aging, GX40CrSi17 heat-resistant cast steel is suitable for working temperatures below 900 ℃. Long term use above 950 ℃ will result in a decrease in high-temperature performance due to the significant re dissolution of M23C6 phase and grain size growth.