Exploring the root causes of casting defects is essential to implementing effective countermeasures and improving casting quality. Here are some common casting defects, their root causes, and corresponding countermeasures:
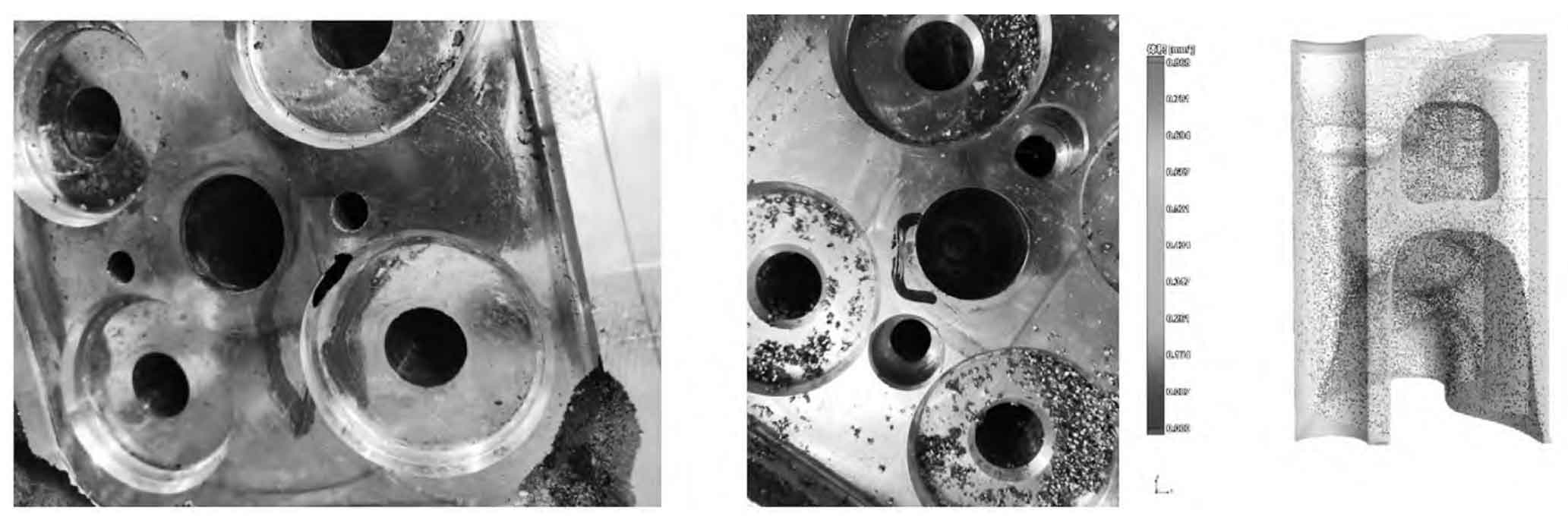
- Porosity:
- Root Causes: Entrapped gases during solidification, inadequate venting, excessive moisture in molds or cores, or improper gating design.
- Countermeasures: Optimize mold and core venting, control moisture content, use proper gating and riser design, utilize effective degassing techniques, and adjust pouring parameters to minimize gas entrapment.
- Shrinkage:
- Root Causes: Insufficient feeding, inadequate riser design, excessive cooling rates, or improper solidification characteristics of the alloy.
- Countermeasures: Improve riser design and placement to provide sufficient feeding, optimize cooling rates, modify alloy composition or inoculation techniques to promote favorable solidification characteristics, and consider the use of chills or insulating sleeves.
- Cold Shuts:
- Root Causes: Poor fusion between two sections of the casting due to inadequate metal flow, premature freezing, or misalignment of mold sections.
- Countermeasures: Optimize gating and riser design to ensure proper metal flow, improve mold filling conditions, optimize pouring temperature and rate, and ensure proper mold alignment.
- Misruns:
- Root Causes: Inadequate fluidity of the molten metal, improper gating or pouring techniques, insufficient mold temperature, or inadequate venting.
- Countermeasures: Optimize pouring temperature, optimize gating and riser design for improved fluidity, ensure proper mold preheating, and provide adequate venting to allow for air escape.
- Sand Inclusions:
- Root Causes: Sand or mold material being entrapped in the casting during mold filling, inadequate mold coatings, or improper mold handling.
- Countermeasures: Ensure proper mold coating and release agent application, control mold temperature and humidity, optimize pouring techniques to minimize sand disturbance, and implement effective shakeout and cleaning procedures.
- Cracks:
- Root Causes: Thermal stresses during solidification or cooling, improper part design or gating, excessive mold hardness, or inadequate feeding.
- Countermeasures: Optimize riser design for proper feeding, control cooling rates to minimize thermal stresses, consider the use of heat treatments or stress relieving techniques, and ensure proper mold hardness for reduced cracking susceptibility.
- Dimensional Inaccuracies:
- Root Causes: Inadequate mold rigidity, improper solidification or cooling rates, mold distortion or warping, or inaccurate pattern or core assembly.
- Countermeasures: Optimize mold design for rigidity and stability, control solidification and cooling rates, implement proper pattern and core assembly techniques, utilize dimensional control fixtures, and conduct regular dimensional inspections.
To effectively implement countermeasures, it is important to conduct thorough defect analysis, including visual inspections, non-destructive testing, and statistical analysis of process parameters. This helps in identifying the root causes specific to the casting defects observed. By addressing these root causes through process optimization, design improvements, and appropriate corrective actions, manufacturers can significantly reduce casting defects and improve overall casting quality.