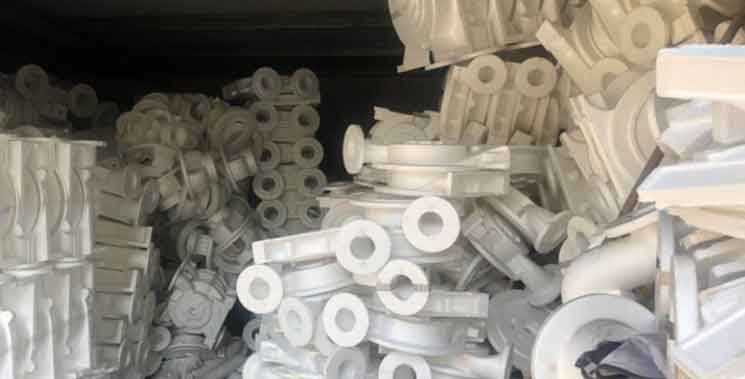
Lost foam casting is indeed a casting technique that has gained popularity due to its ability to minimize waste and produce complex metal parts with high precision. It offers several advantages over traditional casting methods, making it a promising and efficient manufacturing process.
Lost foam casting, also known as evaporative pattern casting or full mold casting, involves creating a foam pattern in the shape of the desired metal part. This pattern is then coated with a refractory material to form a refractory mold. The mold is then filled with molten metal, which replaces the foam pattern through the vaporization and combustion of the foam.
The main advantages of lost foam casting include:
- Minimal waste: Unlike traditional casting methods that require the production of a permanent pattern (usually made of wood or metal), lost foam casting eliminates the need for a pattern. The foam pattern is consumed during the casting process, leaving no waste behind. This greatly reduces material consumption and waste generation.
- Complex shapes and intricate details: Lost foam casting allows for the production of complex and intricate metal parts with high dimensional accuracy. The foam patterns can be easily carved or molded into intricate shapes, enabling the creation of parts with fine details that would be difficult or expensive to achieve with other casting methods.
- Reduced machining and assembly: Since lost foam casting produces near-net-shape parts, it often eliminates the need for extensive machining and assembly operations. This results in cost savings and reduced production time.
- Design flexibility: The foam patterns used in lost foam casting can be easily modified or replicated, offering design flexibility. This allows for rapid prototyping and the ability to make design changes quickly and cost-effectively.
- Improved casting quality: The absence of a parting line, as seen in traditional casting methods, reduces the risk of defects such as sand inclusions or misalignment. The molten metal fills the mold cavity more uniformly, resulting in better surface finish and dimensional accuracy.
However, it’s important to note that lost foam casting also has some limitations and considerations:
- Material limitations: Lost foam casting is primarily used for casting metals with low melting points, such as aluminum and certain alloys. It may not be suitable for casting high-temperature alloys or ferrous metals due to the limitations of the foam pattern material.
- Pattern and mold quality: The foam patterns used in lost foam casting must be of high quality to ensure dimensional accuracy and avoid defects. The quality of the refractory mold is also crucial to prevent mold degradation or failure during the casting process.
- Environmental considerations: While lost foam casting reduces material waste, the combustion of foam patterns may release potentially harmful gases or particulate matter. Proper ventilation and emission control measures are necessary to mitigate any environmental impacts.
Lost foam casting is a valuable technique for metal casting that offers significant advantages in terms of minimal waste, complex shape production, reduced machining, and improved casting quality. By leveraging this process, manufacturers can achieve cost savings, faster production times, and enhanced design flexibility, making it a compelling option for various industries.