Lost Foam Casting, also known as evaporative pattern casting, is a modern manufacturing technique that offers numerous advantages in the production of complex metal components. This innovative casting method has gained popularity in various industries due to its ability to create intricate designs, reduce production time, and improve overall cost-effectiveness.
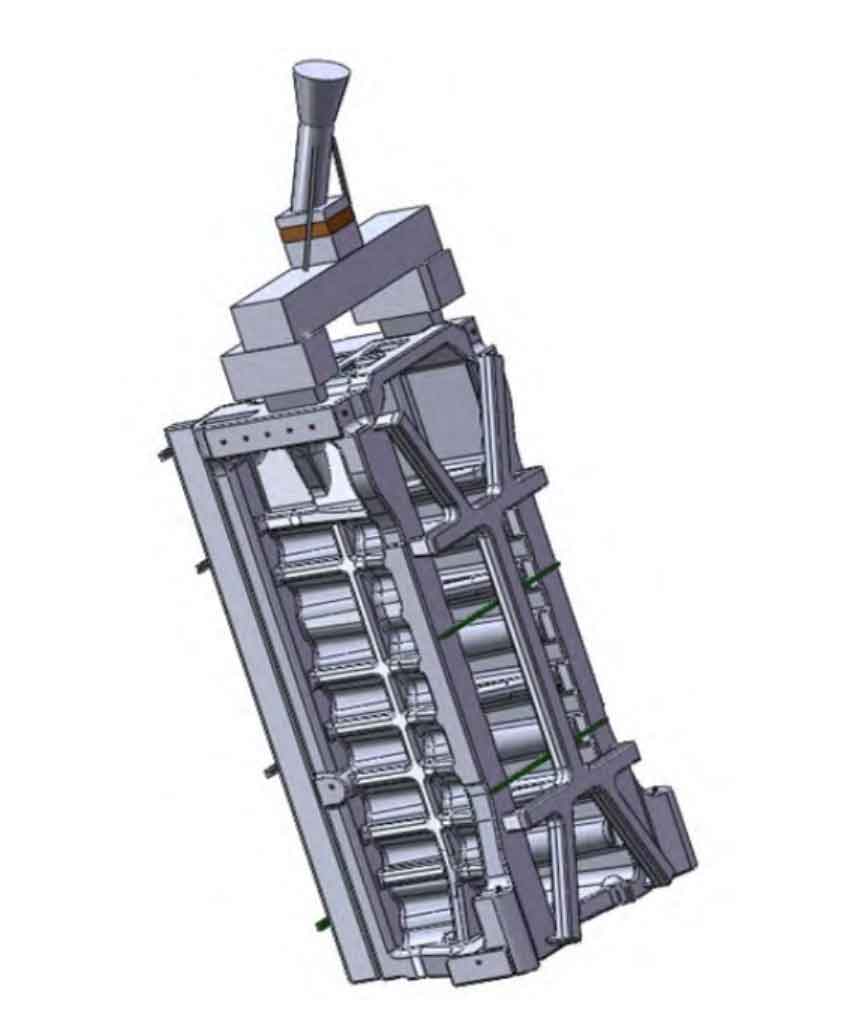
One of the primary advantages of Lost Foam Casting is its ability to produce complex geometries with ease. Traditional casting methods often struggle with intricate designs and internal cavities, leading to limitations in product design and functionality. However, Lost Foam Casting allows for the creation of intricate patterns and complex shapes with high precision, providing manufacturers with more design freedom and flexibility.
Furthermore, Lost Foam Casting eliminates the need for expensive and time-consuming pattern-making processes. Instead of using permanent patterns made from wood or metal, Lost Foam Casting utilizes expendable foam patterns. These patterns are created by molding expanded polystyrene (EPS) into the desired shape. The foam pattern is then coated with a refractory material, forming a refractory mold that will be used for casting.
The use of foam patterns offers significant advantages. Firstly, foam patterns can be easily shaped and manipulated, making it possible to create intricate and delicate features that would be challenging or impossible to achieve with traditional patterns. Secondly, foam patterns are lightweight, reducing the overall weight of the mold and making handling and transportation more convenient.
Another key advantage of Lost Foam Casting is its ability to eliminate the need for parting lines and cores. In traditional casting methods, complex components often require multiple parting lines and cores to create the desired shape. This increases the complexity and cost of production. With Lost Foam Casting, the foam pattern is the only pattern required, as it vaporizes when the molten metal is poured into the mold. This results in a seamless, coreless casting with a smooth surface finish.
Lost Foam Casting also offers advantages in terms of cost and time efficiency. By eliminating the need for multiple patterns, cores, and assembly processes, manufacturers can significantly reduce production time and costs. The simplified process also reduces the risk of defects and improves overall quality control.
Additionally, Lost Foam Casting is an environmentally friendly casting method. The foam patterns used in the process are made from recyclable materials, making them sustainable and reducing waste. The evaporative nature of the foam patterns eliminates the need for pattern disposal and reduces the environmental impact associated with traditional pattern-making processes.
In conclusion, Lost Foam Casting presents numerous advantages in modern manufacturing. Its ability to create complex geometries, reduce production time and costs, and provide design flexibility has made it a preferred choice in various industries. With its cost-effectiveness, efficiency, and environmental sustainability, Lost Foam Casting is shaping the future of metal component production.