Porosity in sand casting processes can significantly impact the quality and performance of the final product. It’s therefore essential to understand the key factors that contribute to this phenomenon. By identifying these factors, steps can be taken to mitigate their effects and improve the quality of the casting. This article explores the primary factors influencing porosity in sand casting processes.
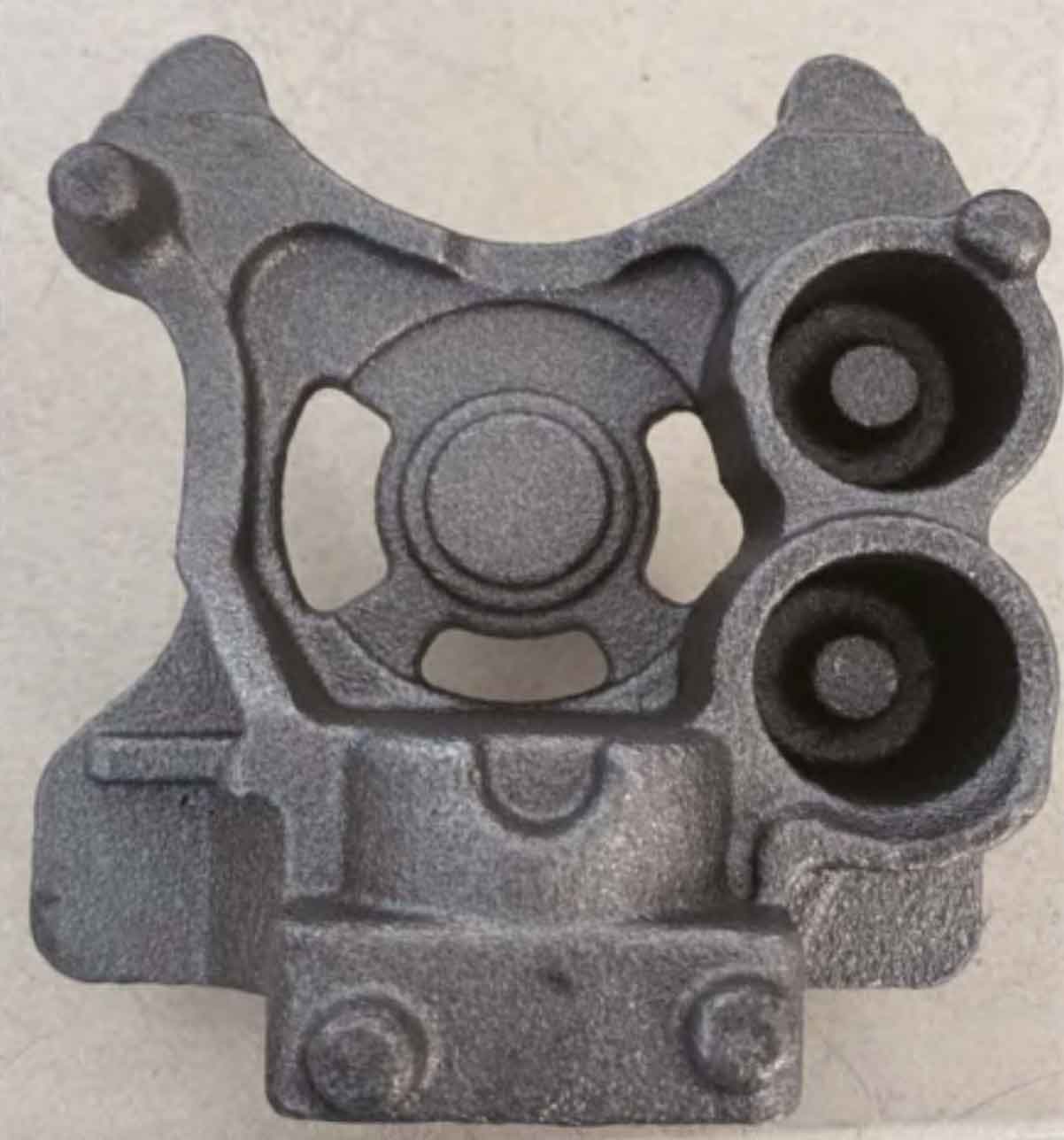
1.Gas Entrapment:
One of the primary causes of porosity in sand casting is the entrapment of gases within the molten metal during the pouring process. This can be influenced by several factors:
- Turbulent Pouring: Rapid or turbulent pouring can cause gas to become entrapped within the molten metal, leading to the formation of bubbles that become voids once the metal solidifies.
- Excessive Gas in Metal or Mold: The presence of excess gas in the molten metal or the molding sand can lead to gas being trapped in the casting. This can be due to improper degassing of the metal or excessive moisture in the sand.
2.Shrinkage:
As the molten metal cools and solidifies, it contracts. If the shrinkage isn’t properly compensated for, it can lead to the formation of voids in the casting. Several factors can influence this:
- Inadequate Riser Design: Risers are used to feed additional molten metal into the mold as the metal solidifies and shrinks. If the risers are not adequately designed or placed, they may not provide enough metal to compensate for the shrinkage.
- Rapid Cooling: If the metal cools too quickly, it can lead to uneven shrinkage and the formation of voids. The cooling rate can be influenced by the temperature of the molten metal, the temperature of the mold, and the thickness of the casting.
3.Inadequate Venting:
Proper venting of the mold is crucial to allow gases generated during the casting process to escape. If the mold is not adequately vented, these gases can become trapped in the casting, leading to porosity.
Several factors can influence the occurrence of porosity in sand casting processes, including gas entrapment, shrinkage, and inadequate venting. By understanding these factors and their effects, manufacturers can implement strategies to mitigate their impact, such as controlled pouring techniques, proper riser design, and adequate mold venting. By doing so, they can improve the quality of their sand castings and reduce the occurrence of porosity.