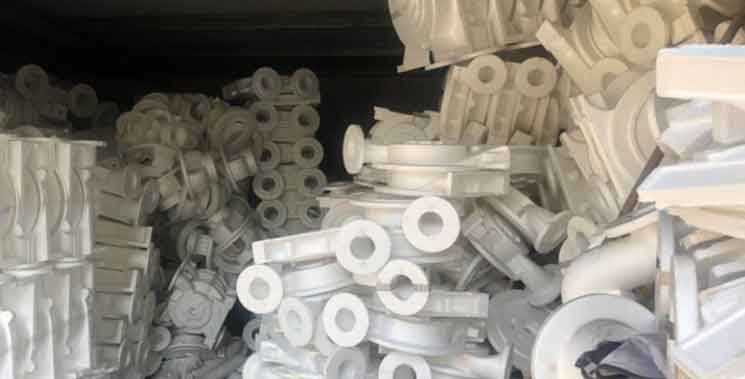
Lost foam casting, also known as evaporative pattern casting, is an innovative and precise casting technique that offers several advantages over traditional casting methods. Let’s explore some of the key advantages of lost foam casting:
1.Complex Geometries:
Lost foam casting allows for the production of complex and intricate geometries with high precision. The foam patterns used in this process can be easily shaped and manipulated to create intricate features and fine details. This capability makes it an ideal choice for manufacturing components with intricate internal passages, thin walls, and complex shapes.
2.Design Freedom:
With lost foam casting, designers have greater freedom to create intricate designs without the constraints of traditional casting methods. The elimination of parting lines and draft angles allows for the creation of seamless and smooth surfaces, reducing the need for additional machining or finishing operations. This not only saves time and costs but also provides greater design flexibility.
3.Weight Reduction:
Lost foam casting enables the production of lightweight components without compromising their structural integrity. By eliminating the need for cores and reducing the thickness of walls, it helps in achieving weight reduction goals. This makes it particularly valuable in industries where weight savings are crucial, such as automotive and aerospace.
4.Cost Efficiency:
Lost foam casting offers cost advantages over other casting methods. The foam patterns used in the process are relatively inexpensive compared to the tooling required for traditional casting methods. Additionally, the elimination of cores and core removal operations reduces material waste and labor costs. The process also requires fewer post-casting machining operations, further contributing to cost savings.
5.Improved Surface Finish:
The absence of parting lines and the smooth surface finish achieved through lost foam casting reduce the need for additional surface treatments. This not only saves time and costs but also ensures a high-quality final product.
6.Reduced Lead Times:
Lost foam casting can significantly reduce lead times in the production of complex components. The process eliminates the need for complex tooling and multiple assembly steps required in traditional casting methods. This streamlined production process results in shorter lead times and faster product delivery.
7.Material Versatility:
Lost foam casting can be used with a wide range of metals, including aluminum, iron, steel, and alloys. This versatility allows for the production of components for various industries, catering to their specific material requirements.
8.Environmental Benefits:
Lost foam casting is considered environmentally friendly due to its low energy consumption and reduced material waste. The foam patterns used in the process can be recycled, reducing the overall environmental impact.
The advantages of lost foam casting make it a preferred choice in industries where complex geometries, design freedom, weight reduction, and cost efficiency are critical factors. As the technique continues to advance, with improvements in process control and materials, it is likely to further unlock its potential and find broader applications in the manufacturing industry.