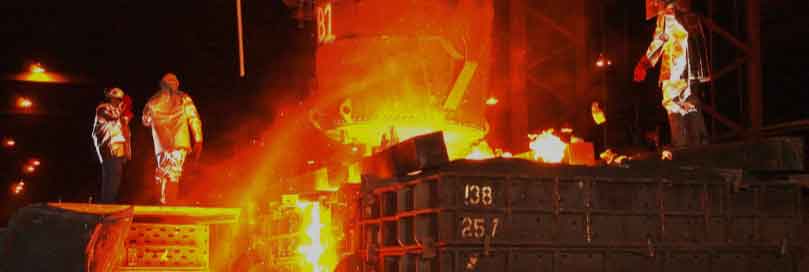
Sand casting offers several advantages that make it a popular and versatile choice for foundry applications in various industries. Some of the key advantages of sand casting include:
- Cost-Effectiveness: Sand casting is a relatively low-cost manufacturing process compared to other casting methods like die casting or investment casting. The raw materials, such as sand and bonding agents, are readily available and affordable. Additionally, the tooling and equipment costs are generally lower, making it an attractive option for both small and large-scale production.
- Versatility: Sand casting can be used to produce a wide range of metal components, from small intricate parts to large and complex structures. Its adaptability allows manufacturers to cast components of varying sizes, shapes, and configurations, meeting the diverse needs of different industries.
- Complex Geometries: Sand casting can accommodate complex and irregular geometries, including internal cavities and undercuts, that may be challenging or expensive to produce with other casting methods. The flexibility of sand molds allows for the creation of intricate designs and unique features in the final casting.
- Design Flexibility: Design changes can be easily implemented in sand casting without significant additional costs. This flexibility makes it suitable for rapid prototyping and iteration during the product development phase.
- Availability of Materials: Sand casting can be used with a wide range of metals and alloys, including aluminum, brass, bronze, cast iron, and steel. This diversity of materials allows manufacturers to choose the most suitable alloy for specific applications, considering factors like strength, corrosion resistance, and thermal conductivity.
- Short Lead Times: Compared to other casting methods that require the production of complex tooling, sand casting has relatively short lead times. Once the sand mold is prepared, the casting process can be carried out quickly and efficiently.
- Sustainability: Sand used in the casting process can be recycled and reused, reducing waste and environmental impact. The recyclability of sand makes sand casting a more sustainable choice compared to some other casting methods that generate more waste.
- Adaptable to Batch Production: Sand casting is well-suited for both single-piece and batch production, making it an ideal choice for foundries that need to produce components in varying quantities.
- Tolerates High Temperatures: Sand molds can withstand high temperatures, making sand casting suitable for casting metals with high melting points, such as steel and some specialty alloys.
Overall, sand casting is a time-tested and reliable method for producing metal components with a balance of cost-effectiveness, design flexibility, and adaptability to various applications. Its ability to handle complex shapes and its compatibility with a wide range of materials make it a favored choice in the foundry industry. As digital technologies continue to be integrated into the process, sand casting is likely to further enhance its efficiency and expand its applications in the manufacturing landscape.