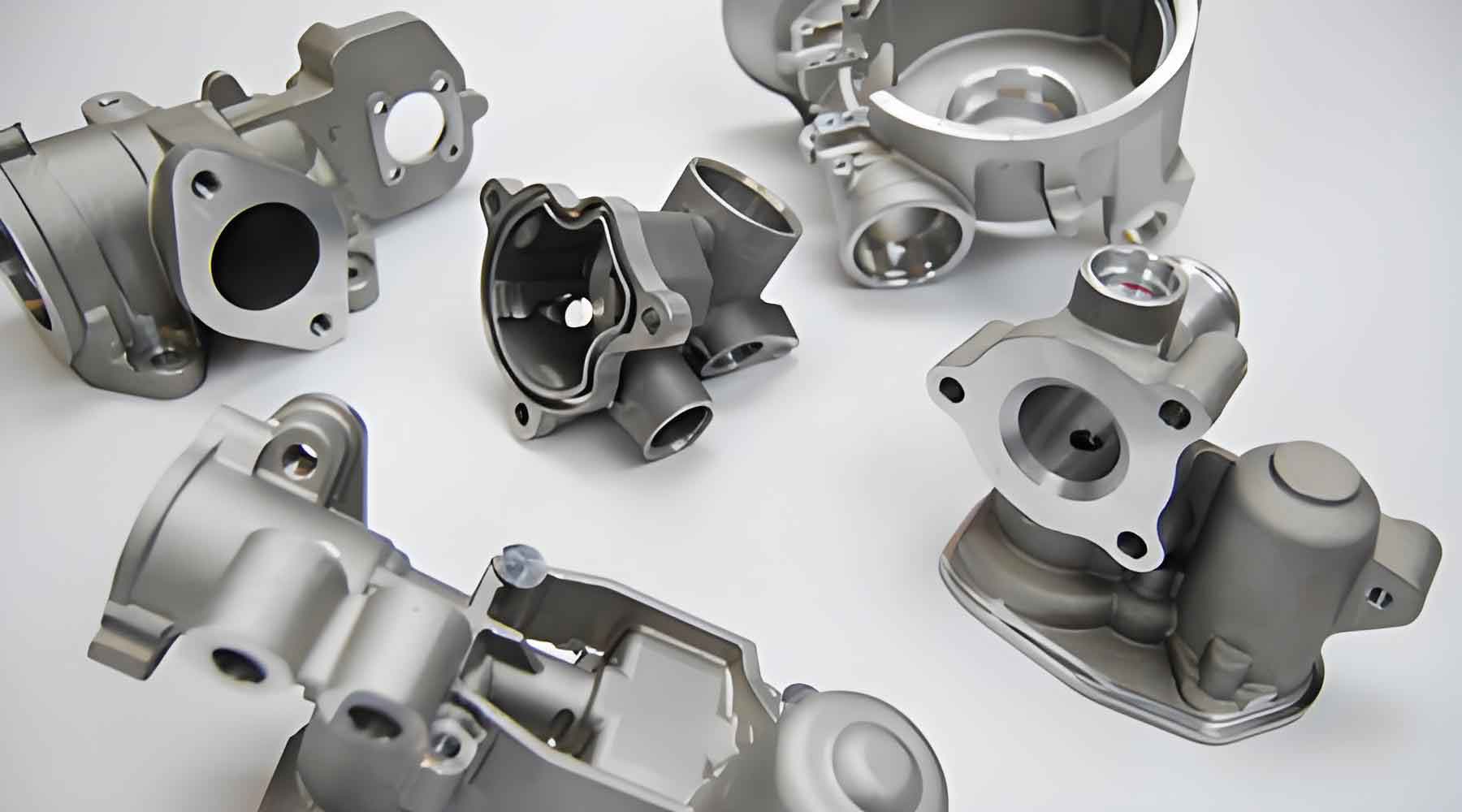
Precision casting is manufacturing process known for its ability to produce high-quality metal components with intricate details and excellent dimensional accuracy. This article explores the various economic benefits of precision casting in industrial manufacturing, highlighting how this advanced technique can lead to cost savings, improved product quality, and increased efficiency.
Introduction to Precision Casting
Precision casting involves creating a wax model of the desired component, coating it with a ceramic shell, and then pouring molten metal into the mold. Once the metal solidifies, the ceramic shell is removed to reveal a precisely cast component. This process is widely used in industries such as aerospace, automotive, medical, and energy due to its ability to produce complex shapes with minimal machining and high material efficiency.
Economic Benefits of Precision Casting
- Reduced Material Waste
- Lower Machining Costs
- Enhanced Design Flexibility
- Improved Production Efficiency
- Higher Quality and Reliability
Reduced Material Waste
One of the primary economic benefits of precision casting is the significant reduction in material waste. The precision and accuracy of the casting process ensure that material is used efficiently, minimizing the amount of excess metal that needs to be machined away.
Benefits:
- Cost Savings on Raw Materials: Less material waste translates to lower raw material costs.
- Environmental Benefits: Reduced waste contributes to more sustainable manufacturing practices.
Benefit | Description | Example Application |
---|---|---|
Cost Savings on Raw Materials | Minimizes excess material usage | Automotive components |
Environmental Benefits | Reduces waste, contributing to sustainability | Aerospace parts |
Lower Machining Costs
Precision casting produces components that are near-net shape, meaning they require minimal machining to achieve the final dimensions. This results in significant cost savings in terms of machining time and labor.
Benefits:
- Reduced Labor Costs: Less machining translates to lower labor expenses.
- Shorter Production Time: Faster turnaround times as components require less post-processing.
Benefit | Description | Example Application |
---|---|---|
Reduced Labor Costs | Minimizes machining, lowering labor expenses | Medical devices |
Shorter Production Time | Faster turnaround due to minimal post-processing | Industrial machinery parts |
Enhanced Design Flexibility
Precision casting allows for greater design flexibility compared to other manufacturing processes. Complex geometries, thin walls, and intricate details can be easily achieved, enabling designers to optimize components for performance and cost.
Benefits:
- Optimized Component Design: Ability to produce complex shapes that enhance performance.
- Cost-Effective Prototyping: Rapid prototyping capabilities reduce development costs.
Benefit | Description | Example Application |
---|---|---|
Optimized Component Design | Enables production of complex shapes | Aerospace engine components |
Cost-Effective Prototyping | Rapid prototyping reduces development costs | Consumer electronics |
Improved Production Efficiency
The precision casting process can be automated to a large extent, leading to improved production efficiency and consistency. Automated systems reduce the likelihood of human error and increase the overall throughput of the manufacturing process.
Benefits:
- Consistent Quality: Automated processes ensure high repeatability and consistency.
- Increased Throughput: Higher production rates due to efficient and automated processes.
Benefit | Description | Example Application |
---|---|---|
Consistent Quality | Ensures high repeatability and consistency | High-volume automotive parts |
Increased Throughput | Higher production rates through automation | Industrial valves and fittings |
Higher Quality and Reliability
Precision casting produces components with excellent surface finishes and tight tolerances, reducing the need for secondary operations and ensuring high-quality and reliable products.
Benefits:
- Reduced Need for Secondary Operations: High-quality finishes and tight tolerances minimize additional processing.
- Enhanced Product Reliability: High precision and quality contribute to the reliability and longevity of the components.
Benefit | Description | Example Application |
---|---|---|
Reduced Need for Secondary Operations | High-quality finishes minimize additional processing | Medical implants |
Enhanced Product Reliability | High precision ensures reliability and longevity | Energy sector components |
Future Trends in Precision Casting
- Integration of Advanced Materials
- High-Performance Alloys: Development of new alloys with superior properties.
- Ceramic Matrix Composites: Use of advanced materials for enhanced performance.
- Adoption of Digital Technologies
- IoT and Smart Manufacturing: Integration of IoT devices for real-time monitoring and control.
- Digital Twins: Creation of digital replicas of casting processes for optimization and quality control.
- Sustainable Manufacturing Practices
- Eco-Friendly Materials: Use of sustainable and recyclable materials.
- Energy-Efficient Processes: Implementation of energy-efficient technologies to reduce carbon footprint.
Conclusion
Precision casting offers numerous economic benefits in industrial manufacturing, including reduced material waste, lower machining costs, enhanced design flexibility, improved production efficiency, and higher quality and reliability. By leveraging these advantages, manufacturers can achieve significant cost savings, enhance product performance, and contribute to more sustainable manufacturing practices. The future of precision casting lies in the continued integration of advanced materials, digital technologies, and sustainable practices, driving further innovations and economic benefits in the industry.