This article focuses on the casting process and common defects of diesel engine exhaust pipes. It analyzes the causes of defects such as porosity, sand holes, and cold shuts, and proposes corresponding preventive measures. Through these measures, the defect rate of exhaust pipe castings has been significantly reduced, and the casting quality has been improved.
1. Introduction
Diesel engine exhaust pipes are crucial components in the exhaust system. The quality of the exhaust pipes directly affects the performance and reliability of the diesel engine. However, during the casting process, various defects may occur, which can lead to reduced performance and even failure of the exhaust pipes. Therefore, it is essential to analyze and prevent these casting defects.
1.1 Significance of Studying Casting Defects in Diesel Engine Exhaust Pipes
The study of casting defects in diesel engine exhaust pipes is of great significance for improving the quality and reliability of diesel engines. By understanding the causes and mechanisms of these defects, appropriate preventive measures can be taken to reduce the defect rate and improve the performance of the exhaust pipes. This, in turn, can enhance the overall efficiency and durability of the diesel engine.
1.2 Overview of the Casting Process of Diesel Engine Exhaust Pipes
The casting process of diesel engine exhaust pipes typically involves several steps, including pattern making, mold making, melting and pouring, and solidification. The choice of casting method and process parameters can have a significant impact on the quality of the final product. In this section, we will provide an overview of the casting process used for diesel engine exhaust pipes.
2. Common Casting Defects in Diesel Engine Exhaust Pipes
2.1 Porosity
Porosity is one of the most common casting defects in diesel engine exhaust pipes. It refers to the presence of voids or holes within the casting. Porosity can be caused by a variety of factors, such as gas entrapment, shrinkage, and improper gating and risering.
Cause of Porosity | Description |
---|---|
Gas Entrapment | During the pouring process, gas can be trapped in the molten metal, leading to the formation of porosity. |
Shrinkage | As the molten metal cools and solidifies, it contracts, which can result in shrinkage porosity if there is not enough molten metal to fill the voids. |
Improper Gating and Risering | Inadequate gating and risering systems can cause improper filling of the mold, resulting in porosity. |
2.2 Sand Holes
Sand holes are another common defect in diesel engine exhaust pipes. They occur when sand particles from the mold or core are incorporated into the casting. Sand holes can weaken the structure of the exhaust pipe and lead to leakage.
Cause of Sand Holes | Description |
---|---|
Poor Sand Quality | Low-quality sand with excessive fines or impurities can increase the likelihood of sand holes. |
Inadequate Core Strength | Weak cores can break during the casting process, resulting in sand holes. |
Improper Cleaning | Failure to properly clean the mold and core before pouring can leave sand particles in the casting cavity. |
2.3 Cold Shuts
Cold shuts occur when two streams of molten metal do not fuse properly during the casting process, resulting in a visible seam or crack in the casting. Cold shuts can reduce the strength and integrity of the exhaust pipe.
Cause of Cold Shuts | Description |
---|---|
Low Pouring Temperature | Insufficient pouring temperature can cause the molten metal to solidify too quickly, preventing proper fusion. |
Interrupted Pouring | Any interruption in the pouring process can lead to cold shuts. |
Poor Mold Design | Inadequate gating and runner design can cause turbulent flow, increasing the risk of cold shuts. |
3. Analysis of the Causes of Casting Defects
3.1 Influence of Raw Materials
The quality of raw materials used in the casting process can have a significant impact on the occurrence of casting defects. For example, impurities in the metal can lead to porosity, while poor-quality sand can cause sand holes.
3.2 Influence of Casting Process Parameters
Casting process parameters such as pouring temperature, pouring speed, and mold temperature can also affect the quality of the casting. Improper settings of these parameters can lead to defects such as porosity, sand holes, and cold shuts.
3.3 Influence of Mold and Core
The design and quality of the mold and core play a crucial role in the casting process. A poorly designed or defective mold or core can cause various casting defects.
4. Preventive Measures for Casting Defects
4.1 Measures to Prevent Porosity
To prevent porosity, it is essential to control the gas content in the molten metal, ensure proper gating and risering, and optimize the solidification process.
Preventive Measure | Description |
---|---|
Degassing | Using degassing techniques to remove gas from the molten metal. |
Optimize Gating and Risering | Designing an appropriate gating and risering system to ensure proper filling and feeding of the mold. |
Control Pouring Temperature | Pouring the metal at the correct temperature to promote proper solidification. |
4.2 Measures to Prevent Sand Holes
Preventing sand holes requires using high-quality sand, strengthening the core, and ensuring proper cleaning of the mold and core.
Preventive Measure | Description |
---|---|
Sand Quality Control | Selecting sand with the appropriate particle size distribution and low impurity content. |
Core Strengthening | Using binders and additives to improve the strength of the core. |
Mold and Core Cleaning | Thoroughly cleaning the mold and core before pouring to remove any sand particles. |
4.3 Measures to Prevent Cold Shuts
To prevent cold shuts, it is necessary to maintain a proper pouring temperature, avoid interruptions in the pouring process, and optimize the mold design.
Preventive Measure | Description |
---|---|
Temperature Control | Pouring the metal at a consistent and appropriate temperature. |
Smooth Pouring | Ensuring a continuous and smooth pouring process. |
Mold Design Optimization | Designing the mold with proper gating and runner systems to promote laminar flow. |
5. Case Study
In this section, we will present a case study of a diesel engine exhaust pipe casting factory that successfully reduced the defect rate by implementing the preventive measures discussed in this article.
Before Implementation | After Implementation |
---|---|
Defect Rate: 13.3% | Defect Rate: 2.03% |
The factory analyzed the causes of the defects and took appropriate measures, such as improving the sand quality, optimizing the casting process parameters, and strengthening the quality control of the mold and core. As a result, the defect rate was significantly reduced, and the quality of the exhaust pipe castings was improved.
6. Conclusion
In conclusion, casting defects in diesel engine exhaust pipes can have a significant impact on the performance and reliability of the diesel engine. By understanding the causes of these defects and implementing appropriate preventive measures, the defect rate can be reduced, and the quality of the exhaust pipes can be improved. This, in turn, can enhance the overall performance and durability of the diesel engine.
It is important for casting factories to pay attention to the quality control of the casting process and continuously improve their production techniques to meet the increasing demands for high-quality diesel engine exhaust pipes.
In the future, further research can be conducted to explore more advanced preventive measures and optimization techniques for casting defects in diesel engine exhaust pipes. This will contribute to the development of the casting industry and the improvement of the quality of diesel engine products.
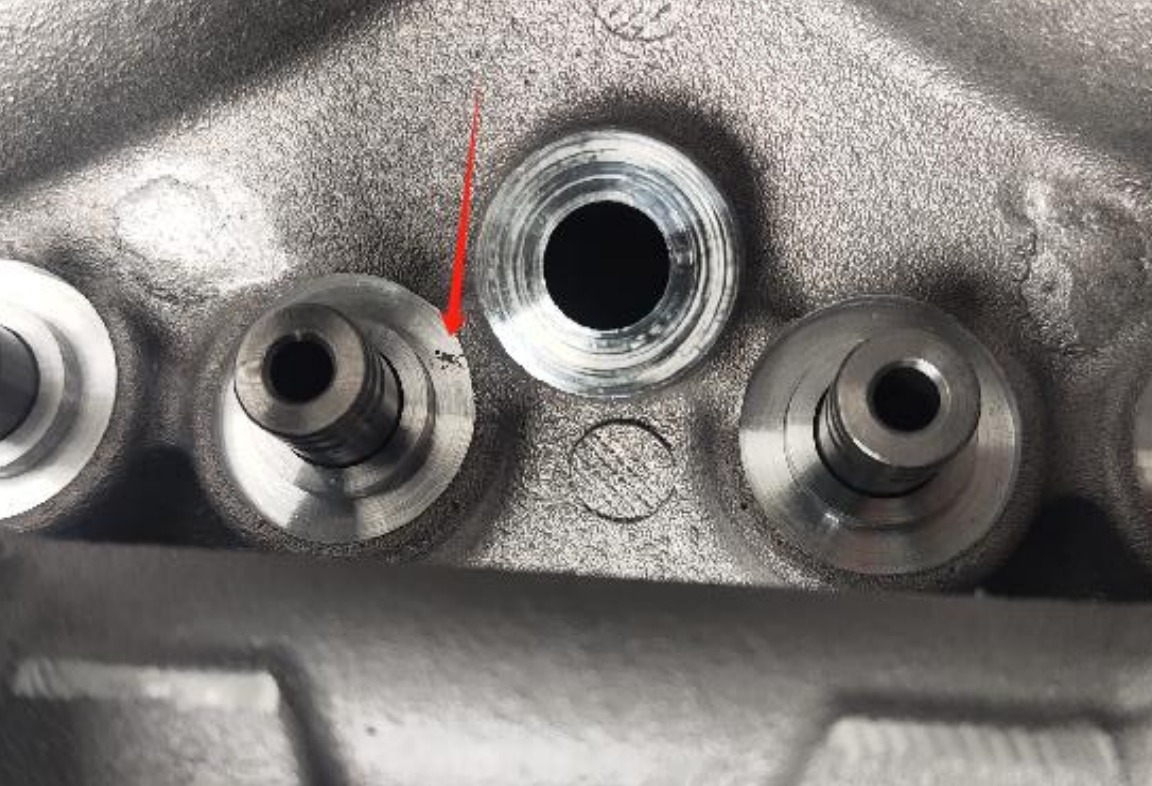