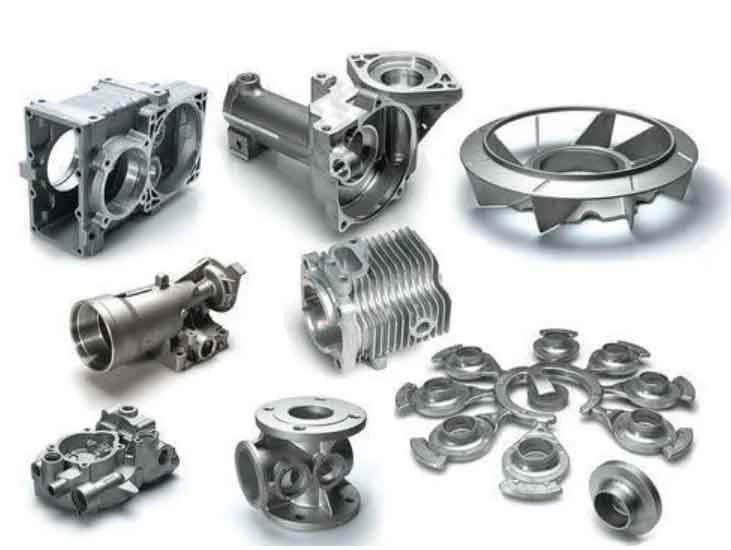
Grey cast iron is well-known for its exceptional wear resistance, making it a preferred choice for applications where components are subjected to sliding or abrasive wear. The wear resistance of grey cast iron can be attributed to its microstructure and the presence of graphite flakes within its matrix. Here are some factors that contribute to the exceptional wear resistance of grey cast iron:
- Graphite Flakes: Grey cast iron contains a significant amount of graphite flakes distributed throughout its matrix. These graphite flakes act as solid lubricants, reducing friction and minimizing wear between contacting surfaces. The graphite flakes provide a self-lubricating mechanism, improving the wear resistance of grey cast iron components.
- Abrasion Resistance: The microstructure of grey cast iron, consisting of graphite flakes embedded in a matrix of ferrite and pearlite, provides excellent resistance to abrasive wear. The hard and brittle nature of the graphite flakes enables them to withstand abrasive forces, preventing excessive wear on the surface of the material.
- Matrix Structure: The matrix of grey cast iron, composed of ferrite and pearlite, contributes to its wear resistance. The pearlite phase, consisting of alternating layers of ferrite and cementite, provides hardness and strength to the material. This matrix structure enhances the overall wear resistance of grey cast iron components.
- Heat Dissipation: Grey cast iron’s high thermal conductivity allows for efficient heat dissipation. In applications involving sliding wear, the generated heat can be effectively dissipated, reducing the risk of thermal damage and wear.
- Proper Lubrication: While grey cast iron exhibits good inherent wear resistance, proper lubrication further enhances its performance in wear-intensive applications. Lubricants help minimize friction and reduce wear rates, extending the lifespan of grey cast iron components.
- Microstructural Control: Through careful control of the casting process and heat treatment, the microstructure of grey cast iron can be optimized for enhanced wear resistance. Heat treatments like annealing, quenching, or alloying can modify the microstructure to achieve specific wear resistance properties based on the application requirements.
Applications that benefit from the exceptional wear resistance of grey cast iron include:
- Brake components: Grey cast iron is commonly used for brake discs and drums due to its ability to withstand the high friction and heat generated during braking, providing reliable and long-lasting performance.
- Machine tool components: Grey cast iron is employed in machine tool beds, slides, and ways to withstand the abrasive forces and wear associated with metal cutting and machining processes.
- Agricultural machinery: Grey cast iron is used in components such as plowshares, tillage equipment, and harvesters, where resistance to abrasive wear from soil and other particles is crucial.
- Mining and construction equipment: Grey cast iron finds applications in mining machinery and construction equipment, where resistance to abrasive wear from rocks, gravel, and other abrasive materials is necessary.
- Pump and valve components: Grey cast iron is utilized in pump impellers, valve seats, and valve bodies to withstand wear caused by abrasive fluids and particulates.
The exceptional wear resistance of grey cast iron, coupled with its other advantageous properties like cost-effectiveness and machinability, makes it a reliable choice for various applications that require durability and extended component life in the face of sliding or abrasive wear.