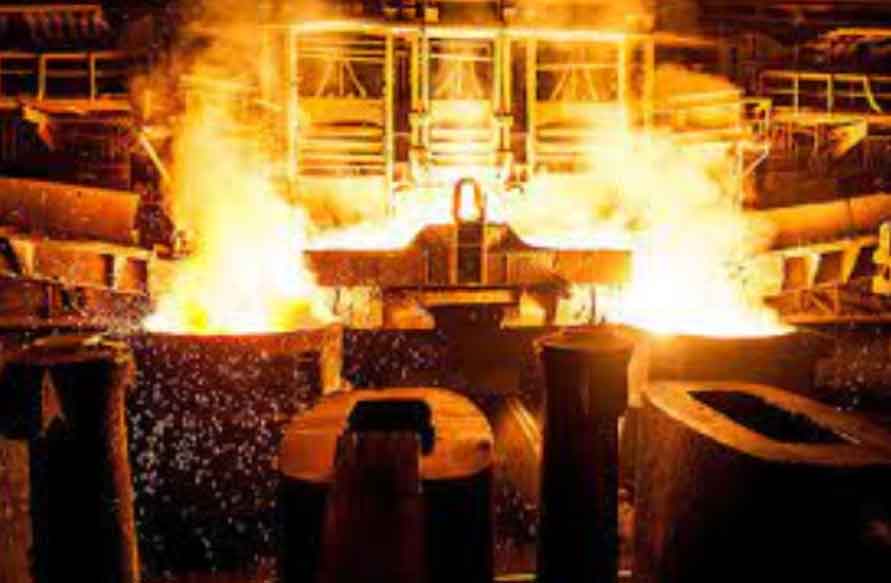
Lost Foam Casting and Gravity Casting are both popular casting processes used in the manufacturing industry. While they share similarities, there are distinct differences between the two. Let’s compare them based on various factors:
- Process Overview:
- Lost Foam Casting: In this process, a foam pattern of the desired part is created and coated with a refractory material. The coated pattern is then embedded in a flask filled with loose sand. Molten metal is poured into the flask, causing the foam to vaporize and the metal to take its place, resulting in a solid metal casting.
- Gravity Casting: Gravity casting, also known as permanent mold casting, involves the use of a reusable mold made of metal (typically steel or iron). The mold is preheated and coated with a refractory material. Molten metal is poured into the mold, and gravity is used to fill the cavity. After solidification, the mold is opened, and the casting is removed.
- Design Complexity:
- Lost Foam Casting: This method allows for complex and intricate designs since the foam pattern can be easily shaped and manipulated. The foam can be easily carved or machined to create intricate details, thin walls, and undercuts, resulting in highly detailed castings.
- Gravity Casting: While gravity casting can accommodate moderately complex designs, it may not be as suitable for intricate details and complex geometries. The mold design for gravity casting typically consists of two halves, limiting the complexity of the part.
- Surface Finish:
- Lost Foam Casting: Lost foam castings generally have a smooth surface finish, requiring minimal post-processing. The foam pattern’s surface quality directly translates into the casting’s surface quality, resulting in good surface finishes without the need for additional finishing operations.
- Gravity Casting: Gravity castings can achieve good surface finishes, but they may require some post-processing, such as sanding or polishing, to achieve the desired level of smoothness.
- Material Versatility:
- Lost Foam Casting: This process is commonly used for casting non-ferrous metals like aluminum, bronze, and magnesium. It can also be used for cast iron and steel, although additional steps are required to handle the higher temperatures involved.
- Gravity Casting: Gravity casting is suitable for casting a wide range of metals, including aluminum, zinc, copper, and various alloys. The process can handle both non-ferrous and ferrous materials.
- Tooling and Equipment:
- Lost Foam Casting: The process requires the production of foam patterns, which can be achieved through CNC machining or rapid prototyping techniques. The investment in tooling and equipment for lost foam casting can be higher compared to gravity casting.
- Gravity Casting: Permanent molds used in gravity casting are typically made of steel or iron and can be reused for multiple castings. The initial investment in tooling and equipment for gravity casting is relatively higher, but the molds’ reusability offsets the cost in the long run.
- Production Volume:
- Lost Foam Casting: Lost foam casting is well-suited for both low and high production volumes. It offers flexibility in producing small to large quantities of castings efficiently.
- Gravity Casting: Gravity casting is generally more suitable for medium to high production volumes. The reusable nature of the molds allows for efficient production runs.
Lost Foam Casting and Gravity Casting have their own advantages and applications. Lost Foam Casting excels in complex designs, intricate details, and superior surface finishes, while Gravity Casting is versatile, cost-effective for medium to high volumes, and suitable for a wide range of metals. The choice between the two processes depends on the specific requirements of the casting project, including design complexity, surface finish, material selection, production volume, and cost considerations.