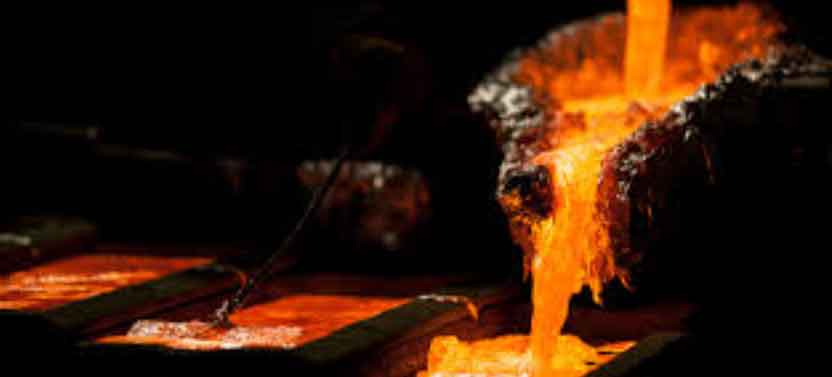
Sand casting is a popular and versatile casting process used to create intricate metal parts and components. It has been employed for centuries and continues to be widely used today due to its cost-effectiveness, flexibility, and ability to produce complex shapes. Let’s explore the intricacies of the sand casting process.
1.Pattern Creation:
The first step in sand casting is the creation of a pattern. The pattern is a replica of the final part and is typically made from wood, plastic, or metal. It includes all the details and features required in the finished casting.
2.Mold Preparation:
A mold is made by packing sand, typically a mixture of silica sand and clay, around the pattern. The sand should be tightly packed to ensure it retains the shape and details of the pattern. The mold is divided into two halves: the cope (top half) and the drag (bottom half). To aid in mold separation, a parting compound is often applied.
3.Pattern Removal and Core Placement:
Once the sand is packed around the pattern, the pattern is carefully removed, leaving a cavity in the sand mold. If the casting requires internal features, cores made of sand or other materials are placed in the mold to create the desired internal cavities.
4.Gating and Risering:
Gates and risers are channels designed into the mold to allow molten metal to flow into the cavity and compensate for shrinkage during solidification. The gating system controls the flow of molten metal, while risers act as reservoirs to supply additional molten metal as the casting cools and solidifies.
5.Pouring:
The molten metal, usually aluminum, brass, bronze, or iron, is poured into the mold through the gating system. The metal is often melted in a furnace and then transferred to a ladle for pouring. The pouring process requires skill and precision to ensure proper filling of the mold.
6.Solidification and Cooling:
After pouring, the molten metal cools and solidifies in the mold cavity. The cooling time depends on the size and complexity of the casting. During this stage, the metal undergoes a phase change from a liquid to a solid, taking the shape of the mold cavity.
7.Shakeout and Cleaning:
Once the metal has solidified and cooled sufficiently, the sand mold is broken apart through a process called shakeout. The casting, still attached to the gating system and risers, is removed. The excess sand is then cleaned off the casting, often through various methods such as sandblasting, shot blasting, or machining.
8.Finishing Operations:
The casting is further refined through various finishing operations such as grinding, machining, sanding, or polishing to achieve the desired surface finish and dimensional accuracy. The gating system and risers are typically removed, leaving behind the final part.
9.Inspection and Quality Control:
The finished casting undergoes inspection and quality control measures to ensure it meets the required specifications. This may involve visual inspection, dimensional measurements, non-destructive testing, and other evaluation techniques.
10.Post-Casting Processes:
Depending on the intended application, the casting may undergo additional processes such as heat treatment, surface coating, or assembly with other components to complete the final product.
Sand casting offers numerous advantages, including low tooling costs, the ability to produce large parts, and the flexibility to create complex geometries. However, it also has some limitations, such as limitations on surface finish and dimensional accuracy compared to other casting methods like investment casting.
Overall, the sand casting process is a versatile and widely used method for creating intricate metal parts, and its continued popularity is a testament to its effectiveness and adaptability.