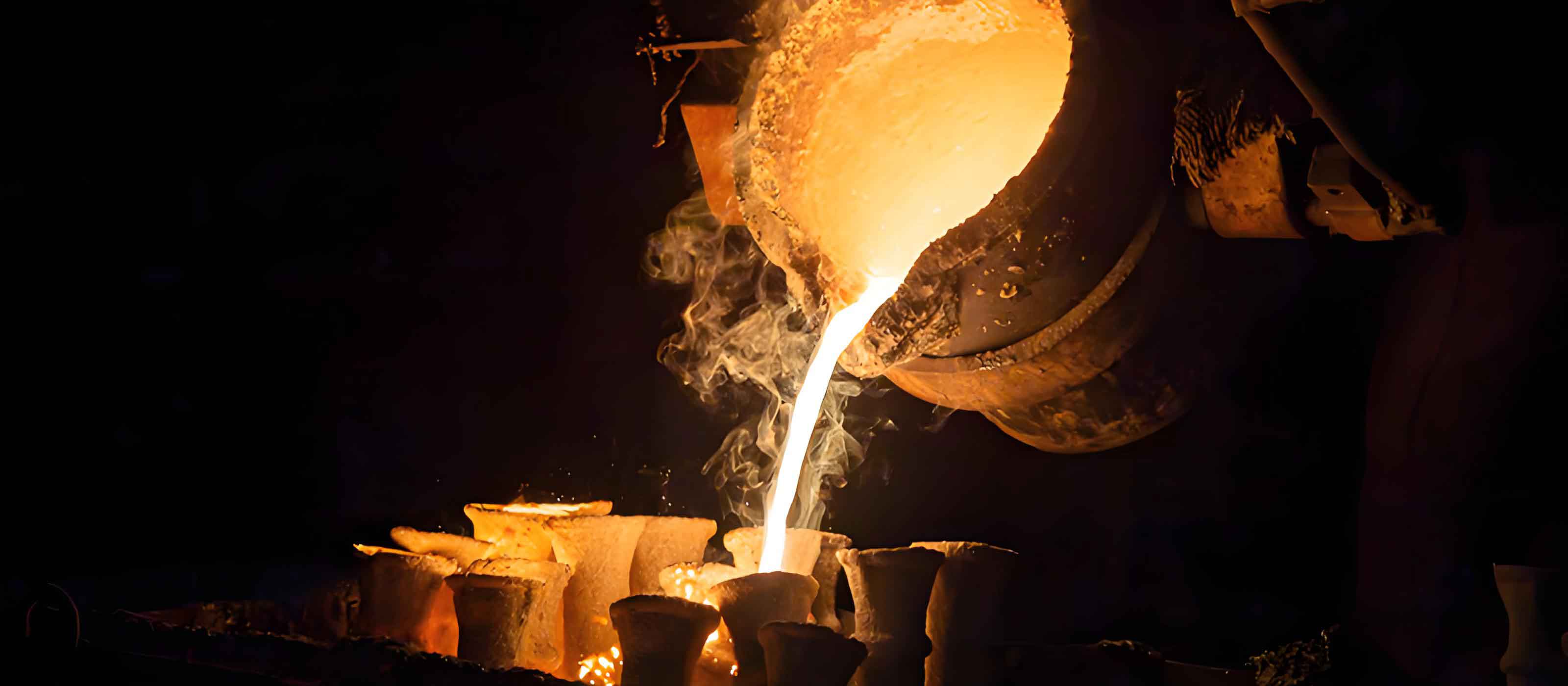
Lost wax casting, also known as investment casting or precision casting, is a time-honored process that dates back thousands of years. This technique, which was once used to create intricate metal objects and sculptures, has evolved with modern technology to produce high-precision components in various industries. This article delves into the materials and techniques used in modern lost wax casting, highlighting the advancements that have made this process indispensable in today’s manufacturing landscape.
Materials Used in Lost Wax Casting
The selection of materials is critical in lost wax casting as it affects the final product’s quality, durability, and functionality. Below is a comprehensive list of materials commonly used in modern lost wax casting:
- Wax:
- Microcrystalline wax
- Paraffin wax
- Beeswax
- Synthetic wax
- Ceramic Materials:
- Silica
- Zircon
- Alumina
- Fused silica
- Metal Alloys:
- Steel alloys (carbon steel, stainless steel)
- Aluminum alloys
- Bronze
- Brass
- Nickel-based alloys
- Titanium
- Binding Agents:
- Ethyl silicate
- Colloidal silica
- Refractory Materials:
- Mullite
- Spinel
- Magnesia
The choice of wax is crucial as it must be easily moldable and have a low melting point. Microcrystalline wax, for example, is favored for its fine granularity and flexibility. On the other hand, the ceramic materials used for creating the shell molds need to withstand high temperatures and provide a smooth finish.
Techniques in Modern Lost Wax Casting
Modern lost wax casting has seen significant technological advancements, improving both precision and efficiency. Here are the key steps involved in the process:
- Creating the Wax Pattern:
- Injection molding: Wax is injected into a metal mold to form the pattern.
- Hand carving: Artisans manually carve detailed designs for custom pieces.
- Assembling the Wax Pattern:
- Multiple wax patterns are assembled onto a central wax sprue to form a tree-like structure.
- Creating the Ceramic Shell:
- Dipping: The wax pattern is repeatedly dipped into a ceramic slurry and coated with fine sand to build a strong shell.
- Drying: The shell is left to dry and harden.
- Wax Removal:
- Dewaxing: The ceramic shell is heated in an autoclave or furnace to melt and drain out the wax, leaving a hollow mold.
- Metal Pouring:
- Preheating: The ceramic mold is preheated to prevent thermal shock during metal pouring.
- Casting: Molten metal is poured into the ceramic mold to fill the cavity left by the wax.
- Shell Removal:
- Cooling: The metal-filled mold is allowed to cool and solidify.
- Shell breaking: The ceramic shell is broken away, revealing the cast metal object.
- Finishing:
- Cleaning: The cast object is cleaned to remove any remaining ceramic material.
- Machining: Additional machining processes may be performed to achieve the desired dimensions and surface finish.
- Inspection: The final product undergoes rigorous inspection for quality control.
Advantages of Modern Lost Wax Casting
- High Precision: Modern techniques allow for the production of components with intricate details and tight tolerances.
- Versatility: Suitable for a wide range of metals and alloys.
- Minimal Material Waste: Efficient use of materials, with minimal waste compared to other casting methods.
- Consistency: Produces high-quality, consistent results suitable for mass production.
Applications of Lost Wax Casting
Lost wax casting is utilized in various industries due to its ability to produce complex and high-quality components. Some notable applications include:
- Aerospace:
- Turbine blades
- Structural components
- Automotive:
- Engine components
- Transmission parts
- Medical:
- Surgical instruments
- Orthopedic implants
- Art and Jewelry:
- Sculptures
- Custom jewelry pieces
- Industrial Machinery:
- Pump components
- Valves and fittings
Case Study: Lost Wax Casting in Aerospace
The aerospace industry heavily relies on lost wax casting for manufacturing high-performance components. For instance, turbine blades used in jet engines are produced using this method. The process ensures that the blades have the necessary aerodynamic shapes, excellent surface finish, and high-temperature resistance.
Table 1: Properties of Materials Used in Aerospace Casting
Material | Density (g/cm³) | Melting Point (°C) | Tensile Strength (MPa) |
---|---|---|---|
Titanium Alloy | 4.5 | 1660 | 950 |
Nickel Alloy | 8.8 | 1450 | 1250 |
Stainless Steel | 7.8 | 1400 | 850 |
Table 2: Key Steps in Aerospace Component Casting
Step | Description |
---|---|
Wax Pattern Creation | High-precision molds used to create detailed wax patterns |
Shell Building | Multiple layers of ceramic material applied to ensure strength and durability |
Dewaxing | Autoclave or furnace used to remove wax and prepare the mold for metal pouring |
Metal Pouring | Molten metal poured into preheated ceramic molds to avoid defects and ensure uniform cooling |
Finishing | Final machining, inspection, and testing to meet stringent aerospace standards |
In conclusion, modern lost wax casting combines ancient craftsmanship with cutting-edge technology, offering unparalleled precision and versatility. The advancements in materials and techniques have expanded its applications across various industries, making it a cornerstone of modern manufacturing. Whether for aerospace, medical, automotive, or artistic purposes, lost wax casting continues to be an essential process in creating high-quality, intricate components.