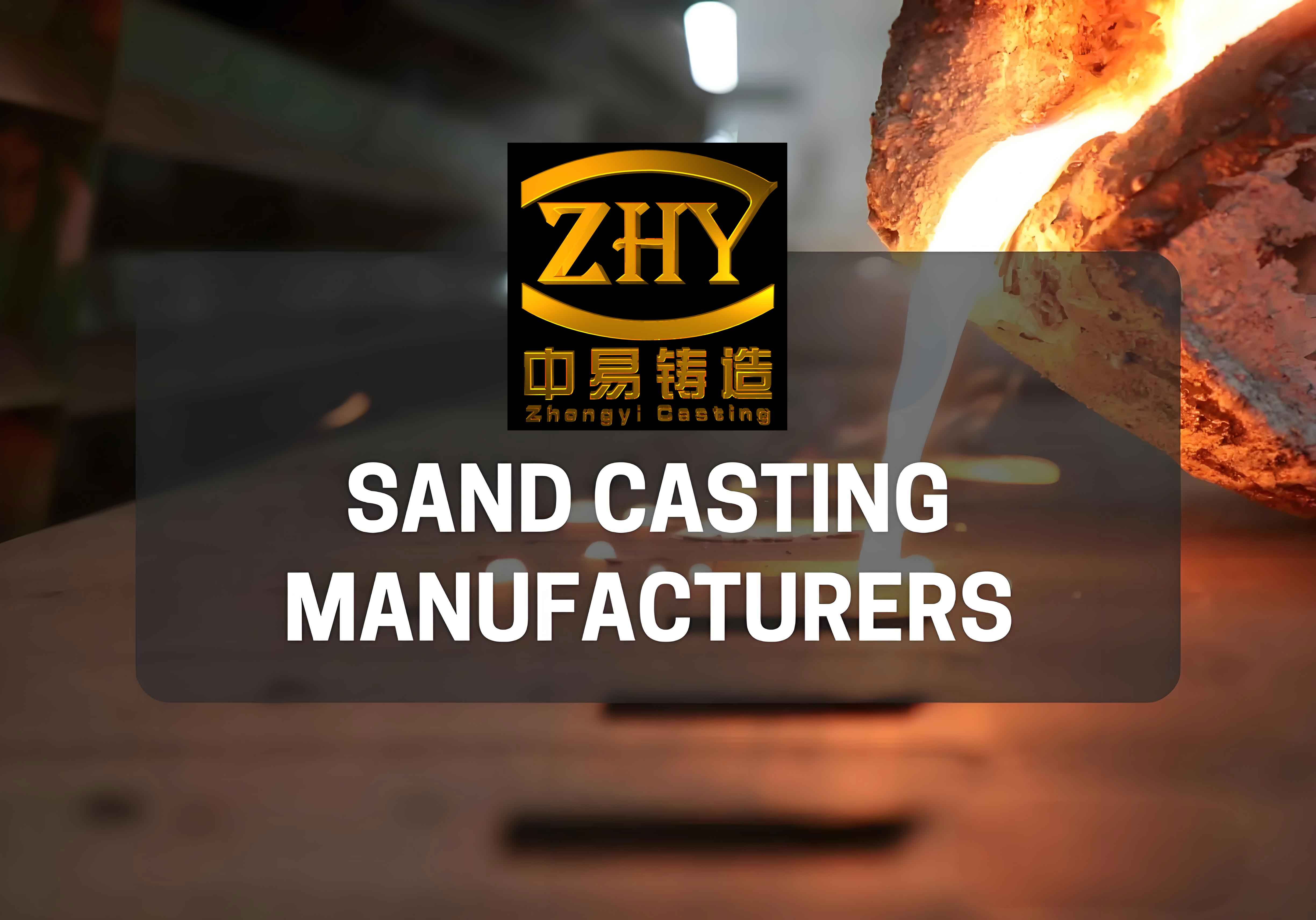
Lean manufacturing is a systematic approach to identifying and eliminating waste through continuous improvement, focusing on enhancing efficiency, quality, and responsiveness to customer needs. Sand casting manufacturers, faced with the challenges of maintaining high-quality standards, controlling costs, and meeting delivery deadlines, are increasingly adopting lean manufacturing practices to stay competitive. This article explores the lean manufacturing practices implemented by sand casting manufacturers and how these practices contribute to operational excellence.
Key Principles of Lean Manufacturing
Lean manufacturing is based on several core principles that guide sand casting manufacturers in streamlining their processes and improving efficiency.
Core Principles of Lean Manufacturing
- Value: Define value from the customer’s perspective.
- Value Stream: Map the value stream to identify and eliminate waste.
- Flow: Ensure smooth flow of materials and processes.
- Pull: Implement pull systems to produce only what is needed, when it is needed.
- Perfection: Strive for continuous improvement and perfection.
Table 1: Core Principles of Lean Manufacturing
Principle | Description |
---|---|
Value | Define value from the customer’s perspective |
Value Stream | Map the value stream to identify and eliminate waste |
Flow | Ensure smooth flow of materials and processes |
Pull | Implement pull systems to produce only what is needed |
Perfection | Strive for continuous improvement and perfection |
Lean Manufacturing Practices in Sand Casting
Sand casting manufacturers employ various lean manufacturing practices to enhance efficiency, reduce waste, and improve product quality. These practices encompass process optimization, waste reduction, inventory management, and continuous improvement.
1. Process Optimization
Optimizing the sand casting process is essential for achieving high efficiency and quality. Sand casting manufacturers use various techniques to streamline their processes.
Techniques for Process Optimization
- Standardized Work: Establishing standardized procedures for each task to ensure consistency and reduce variability.
- 5S Methodology: Implementing the 5S methodology (Sort, Set in order, Shine, Standardize, Sustain) to organize and maintain a clean and efficient workplace.
- Total Productive Maintenance (TPM): Ensuring that equipment is well-maintained to minimize downtime and maximize productivity.
List 1: Techniques for Process Optimization
- Standardized work procedures.
- 5S methodology for workplace organization.
- Total Productive Maintenance (TPM).
2. Waste Reduction
Eliminating waste is a central tenet of lean manufacturing. Sand casting manufacturers identify and eliminate various types of waste to improve efficiency.
Types of Waste and Reduction Strategies
- Overproduction: Producing more than is needed. Strategy: Implement pull systems to produce based on demand.
- Waiting: Idle time while waiting for materials or information. Strategy: Streamline processes to ensure continuous flow.
- Transportation: Unnecessary movement of materials. Strategy: Optimize layout and material handling.
- Inventory: Excess inventory that ties up capital. Strategy: Implement just-in-time (JIT) inventory management.
- Motion: Excessive movement by workers. Strategy: Design efficient workstations and workflows.
- Defects: Production of defective products. Strategy: Implement quality control measures and root cause analysis.
Table 2: Types of Waste and Reduction Strategies
Type of Waste | Description | Reduction Strategy |
---|---|---|
Overproduction | Producing more than needed | Implement pull systems |
Waiting | Idle time waiting for materials or information | Streamline processes for continuous flow |
Transportation | Unnecessary movement of materials | Optimize layout and material handling |
Inventory | Excess inventory tying up capital | Implement just-in-time (JIT) inventory |
Motion | Excessive movement by workers | Design efficient workstations and workflows |
Defects | Production of defective products | Implement quality control measures |
3. Inventory Management
Effective inventory management is crucial for sand casting manufacturers to reduce costs and ensure timely delivery. Lean practices focus on minimizing inventory levels while meeting production needs.
Inventory Management Techniques
- Just-In-Time (JIT): Producing and delivering products just in time to meet customer demand, reducing inventory levels and storage costs.
- Kanban System: Using visual signals to control the flow of materials and ensure that inventory is replenished only when needed.
- Supplier Partnerships: Developing strong relationships with suppliers to ensure reliable and timely delivery of raw materials.
List 2: Inventory Management Techniques
- Just-In-Time (JIT) production.
- Kanban system for inventory control.
- Strong supplier partnerships.
4. Continuous Improvement
Continuous improvement is a cornerstone of lean manufacturing. Sand casting manufacturers foster a culture of continuous improvement to enhance processes, reduce waste, and improve quality.
Continuous Improvement Practices
- Kaizen: Encouraging small, incremental improvements from all employees.
- PDCA Cycle: Using the Plan-Do-Check-Act cycle to implement and monitor improvements.
- Root Cause Analysis: Identifying and addressing the root causes of problems to prevent recurrence.
Table 3: Continuous Improvement Practices
Practice | Description |
---|---|
Kaizen | Encouraging small, incremental improvements |
PDCA Cycle | Plan-Do-Check-Act cycle for implementing improvements |
Root Cause Analysis | Identifying and addressing root causes of problems |
Case Study: Lean Manufacturing in a Sand Casting Manufacturer
A sand casting manufacturer implemented lean manufacturing practices to improve efficiency and reduce waste. The following table outlines the practices adopted and the resulting benefits.
Table 4: Case Study – Lean Manufacturing Practices and Benefits
Lean Practice | Description | Benefit |
---|---|---|
5S Methodology | Organized and maintained a clean workplace | Improved efficiency and safety |
Just-In-Time Inventory | Reduced inventory levels and storage costs | Lowered carrying costs and reduced waste |
Total Productive Maintenance | Ensured equipment was well-maintained | Minimized downtime and increased productivity |
Kaizen | Encouraged continuous improvement from employees | Enhanced processes and employee engagement |
Root Cause Analysis | Addressed root causes of defects | Reduced defect rates and improved quality |
Conclusion
Lean manufacturing practices are essential for sand casting manufacturers to enhance efficiency, reduce waste, and improve product quality. By focusing on process optimization, waste reduction, inventory management, and continuous improvement, sand casting manufacturers can achieve operational excellence and meet the diverse needs of their clients. The adoption of lean principles not only drives cost savings and productivity gains but also fosters a culture of continuous improvement, ensuring long-term success and competitiveness in the market. Through sustained commitment to lean manufacturing, sand casting manufacturers can deliver high-quality, cost-effective, and timely solutions to their customers.