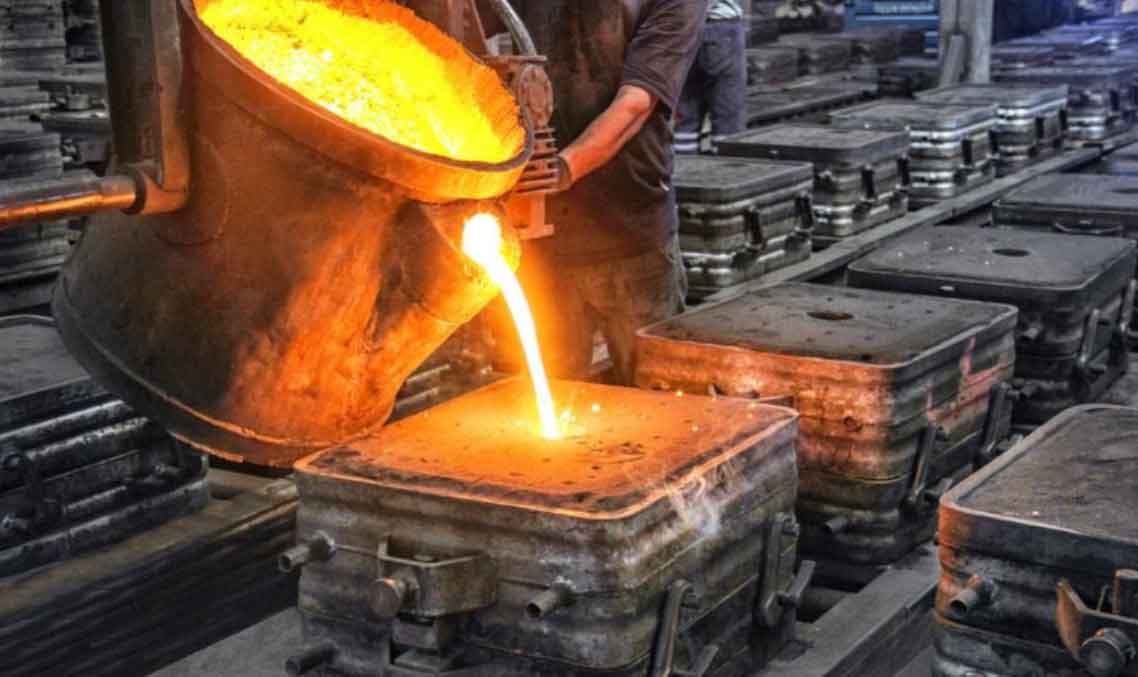
Sand casting is a versatile and widely used process for creating metal castings. It involves the use of sand molds to form intricate shapes and structures from molten metal. Here is an overview of the sand casting process as followed by sand casting manufacturers:
1. Pattern Creation:
- The process begins with the creation of a pattern, which is a replica of the desired final casting. Patterns are typically made from wood, plastic, or metal and are slightly larger than the final casting to account for shrinkage during solidification.
2. Mold Preparation:
- A two-part mold is created around the pattern to form the cavity where the molten metal will be poured. The mold consists of a cope (top half) and a drag (bottom half). The mold material is usually a mixture of sand and a binder to hold the sand grains together.
3. Pattern Placement and Molding:
- The pattern is placed inside the drag, and the cope is positioned on top. The two halves are securely clamped together to create the mold cavity. Additional cores may be inserted into the mold to create internal cavities or intricate features.
4. Molten Metal Pouring:
- The mold is then prepared for pouring by creating gating and risering systems. Gating channels allow molten metal to flow into the mold, while risers serve as reservoirs to feed additional molten metal into the mold as it solidifies.
5. Casting Pouring:
- The molten metal is poured into the mold cavity through the gating system. The metal fills the mold and takes the shape of the pattern and cores.
6. Solidification and Cooling:
- The molten metal cools and solidifies inside the mold. The cooling time depends on the metal’s size, thickness, and cooling rate. Proper gating and risering designs help ensure a smooth and even solidification process.
7. Mold Breakout:
- After the metal has solidified, the mold is opened, and the casting is removed. Sand molds are typically destroyed during the process, so new molds must be created for each casting.
8. Finishing and Cleaning:
- The casting is removed from the mold, and any excess material, such as gating systems or risers, is cut off. Surface finishing techniques, such as grinding, shot blasting, or machining, may be applied to achieve the desired surface quality.
9. Inspection and Quality Control:
- The casting undergoes inspection to check for any defects or imperfections. Non-destructive testing methods, dimensional measurements, and visual inspection are performed to ensure the casting meets the specified requirements.
10. Final Delivery:
- Once the casting passes all quality checks, it is ready for final delivery to the customer for use in their intended application.
Sand casting manufacturers follow these steps with precision and attention to detail to produce high-quality metal castings that meet customer specifications and performance requirements. The process offers flexibility, design freedom, and cost-effectiveness, making it a popular choice for various industries.