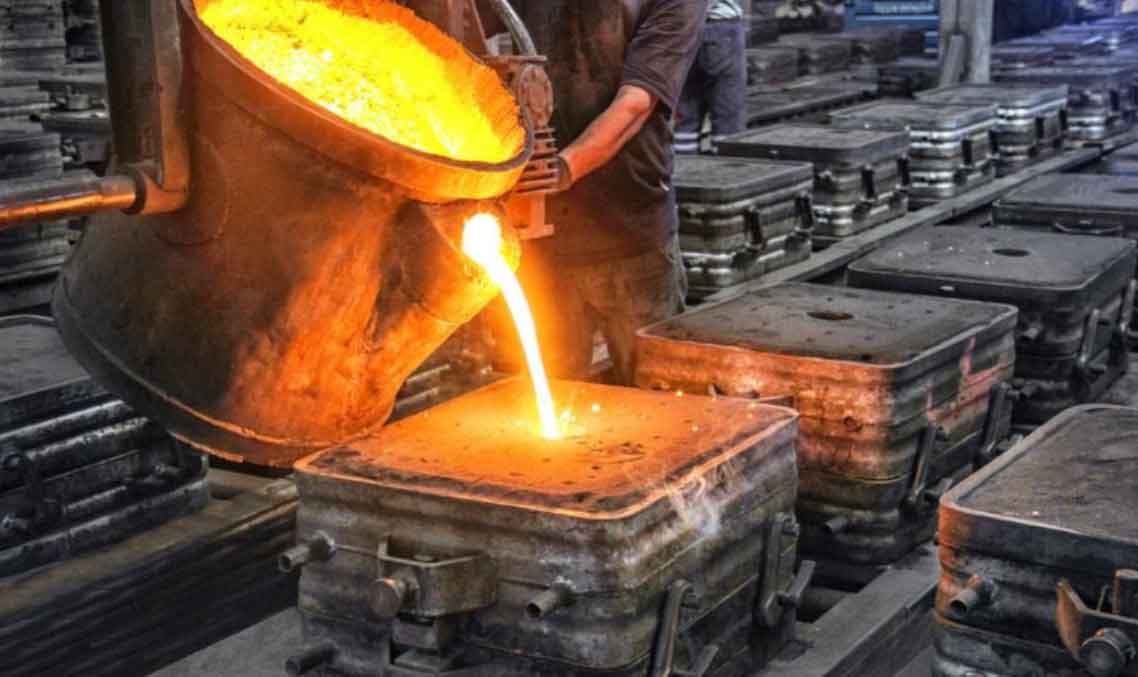
Sand casting is a popular and versatile method for creating metal castings. It involves the use of sand molds to produce intricate and complex metal parts. Here’s an overview of the sand casting process:
- Pattern Making: The first step in sand casting is creating a pattern, which is a replica of the final part to be cast. Patterns can be made from various materials like wood, plastic, or metal. They are designed slightly larger than the desired part to account for material shrinkage during cooling.
- Mold Preparation: A mold is created by packing specially prepared sand around the pattern. The mold is typically made in two halves, with a parting line separating them. The mold must be strong enough to hold its shape during the casting process.
- Core Making (Optional): For parts with internal cavities or features, cores may be created using sand mixed with binders. Cores are positioned within the mold to form the internal shapes of the casting.
- Mold Assembly: The two halves of the mold are brought together, and any necessary gating and riser systems (channels and reservoirs for molten metal flow and feeding) are added to facilitate the casting process.
- Pattern Removal: Once the mold is assembled, the pattern is carefully removed from the sand, leaving a cavity in the shape of the desired part.
- Melting and Pouring: The chosen metal or alloy is melted in a furnace to a specified temperature, and the molten metal is poured into the mold through the gating system. The molten metal displaces the air and fills the entire cavity and core (if used).
- Solidification: As the molten metal cools within the mold, it solidifies and takes the shape of the mold cavity and core. During this process, the metal may contract slightly, which is why the pattern was made larger.
- Cooling and Solidification: The mold is allowed to cool, and the solidified casting is removed from the mold. Sand castings usually have a rough surface finish due to the sand texture. Further finishing processes may be required.
- Finishing: After removal from the mold, the casting undergoes finishing processes such as trimming excess material, removing any gating and riser remnants, and cleaning the casting surface.
- Heat Treatment (Optional): Depending on the material and its desired properties, the casting may undergo heat treatment to improve its mechanical characteristics.
- Quality Control: The finished casting undergoes rigorous inspection, including dimensional checks and non-destructive testing (NDT) to detect any defects or imperfections.
- Post-Processing: Additional post-processing steps like machining, surface treatments (e.g., polishing, painting, or plating), and assembly may be carried out to meet the final product’s specifications.
Sand casting is a versatile and cost-effective method for producing a wide range of metal parts, making it a popular choice in various industries. The process allows for the creation of complex shapes and is suitable for both low-volume and high-volume production runs. However, the surface finish and dimensional accuracy of sand castings may vary and might require further post-processing to achieve the desired end product.