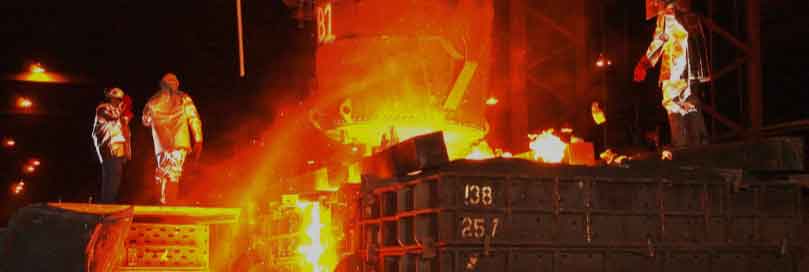
The process of steel castings involves several stages, from design to production. Here is an overview of the typical steps involved:
- Design and Pattern Making: The process starts with the design of the desired component or part. This includes determining the shape, dimensions, and any specific requirements. A pattern, typically made of wood or plastic, is then created based on the design. The pattern represents the final shape of the casting and is used to create the mold.
- Mold Preparation: The pattern is used to create the mold, which is a negative replica of the final casting. The mold can be made of sand, ceramic, or other materials depending on the complexity and requirements of the casting. The mold is prepared by packing the material around the pattern, creating the cavity in which the molten steel will be poured.
- Melting and Pouring: The steel material is melted in a furnace, typically an electric arc furnace or an induction furnace. The molten steel is then poured into the prepared mold through a gating system, which allows the metal to flow smoothly and evenly into the cavity.
- Solidification and Cooling: Once the molten steel is poured into the mold, it starts to solidify and take the shape of the cavity. The solidification process is critical as it determines the final microstructure and properties of the casting. Proper cooling techniques, such as controlled cooling rates or the use of cooling media, are employed to ensure uniform solidification and minimize the formation of defects.
- Shakeout and Cleaning: After the casting has cooled and solidified, the mold is removed. This is typically done through a process called shakeout, where the mold material is broken away from the casting. The casting is then cleaned to remove any remaining mold material, scale, or other impurities. Various cleaning methods such as shot blasting, grinding, or chemical cleaning may be employed.
- Finishing Operations: Once the casting is cleaned, it may undergo additional finishing operations to achieve the desired shape, dimensions, and surface quality. This can include machining, grinding, welding, heat treatment, and other processes to refine the casting and meet specific requirements.
- Quality Control and Inspection: Throughout the casting process, quality control measures are implemented to ensure the final product meets the required specifications. Non-destructive testing methods, such as visual inspection, X-ray, ultrasonic testing, or dye penetrant testing, may be used to detect any defects or inconsistencies in the casting.
- Final Assembly and Delivery: If the steel casting is part of a larger assembly or product, it may undergo final assembly with other components before being prepared for delivery to the customer or integration into the final product.
It’s important to note that the specific process steps and techniques may vary depending on the complexity of the casting, the size and weight of the component, and the requirements of the application. Advanced technologies, such as computer-aided design (CAD), simulation software, and automation, are often used to optimize the casting process and improve efficiency and quality.