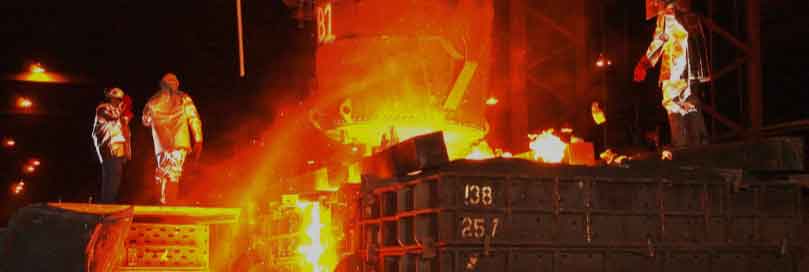
Innovation in steel castings has been driven by the continuous advancements in metallurgical technologies, casting processes, and design optimization. These advancements have opened up new possibilities and expanded the capabilities of steel castings in various industries. Here are some key areas of innovation in steel castings:
- Improved Alloy Development: Researchers and manufacturers have focused on developing new steel alloys with enhanced properties to meet specific application requirements. This includes the development of high-strength, high-temperature, and corrosion-resistant steel alloys that offer improved performance in demanding environments.
- Advanced Casting Processes: Innovative casting processes have been developed to improve the quality, precision, and efficiency of steel castings. For example, advanced computer simulation and modeling techniques help optimize the casting process, reduce defects, and improve casting integrity. Processes such as investment casting, continuous casting, and vacuum casting have also been refined to achieve higher dimensional accuracy and surface finish.
- 3D Printing/Additive Manufacturing: Additive manufacturing, also known as 3D printing, has opened up new possibilities in steel casting production. It allows for complex geometries, customization, and rapid prototyping without the need for traditional tooling. Metal 3D printing techniques, such as selective laser melting (SLM) or electron beam melting (EBM), are being used to produce intricate steel castings with improved design flexibility and reduced lead times.
- Enhanced Quality Control and Inspection: Innovations in non-destructive testing (NDT) methods have improved the quality control and inspection of steel castings. Advanced techniques like ultrasonic testing, X-ray inspection, and 3D scanning enable more accurate detection of defects, internal discontinuities, and dimensional deviations in the castings, ensuring higher quality and reliability.
- Material and Process Optimization: Continuous research and development efforts have focused on optimizing steel casting materials and processes to enhance their performance and efficiency. This includes the development of innovative gating and feeding systems, improved mold materials, and optimized heat treatment processes to minimize casting defects, improve mechanical properties, and increase overall casting yield.
- Environmental Sustainability: Innovations in steel casting have also been driven by a focus on environmental sustainability. Efforts have been made to reduce energy consumption, minimize waste generation, and implement recycling and reuse practices in the casting process. Additionally, the development of sustainable steel alloys and production methods that reduce the environmental impact is gaining attention.
These innovations in steel castings have led to improved product performance, expanded design possibilities, and increased efficiency in various industries, including automotive, aerospace, energy, and construction. They have also contributed to cost reduction, shorter lead times, and enhanced sustainability in steel casting manufacturing.