Sand casting is known for its versatility in manufacturing, offering several advantages that make it a preferred choice in various industries. Let’s explore the versatility of sand casting in manufacturing:
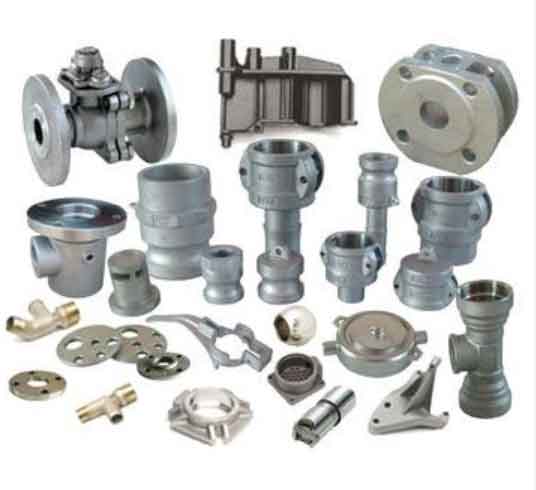
- Wide Range of Materials:
- Sand casting can work with a broad range of metals and alloys, including aluminum, iron, steel, brass, bronze, and even precious metals like gold and silver.
- Different materials can be selected based on the specific properties required for the application, such as strength, corrosion resistance, or heat resistance.
- Complex Geometries:
- Sand casting allows for the production of complex-shaped components with intricate details, such as internal cavities, undercuts, and thin walls.
- The ability to create molds using sand enables the casting of parts with complex shapes that may be challenging or costly to produce using other manufacturing methods.
- Scalability:
- Sand casting is suitable for both small-scale and large-scale production.
- It can accommodate the production of single custom parts, as well as high-volume production runs.
- Cost-Effectiveness:
- Sand casting is a cost-effective manufacturing method, particularly for large and heavy parts.
- The low cost of sand, the ability to reuse molds, and the simplicity of the casting process contribute to its cost advantages.
- Design Flexibility:
- Sand casting offers design flexibility, allowing for modifications and iterations without significant costs or time investments.
- Design changes can be easily implemented by modifying the pattern or core without requiring extensive tooling modifications.
- Quick Turnaround:
- Compared to other casting methods, sand casting generally has a faster turnaround time.
- The simplicity of the process and the availability of materials contribute to shorter lead times for producing sand castings.
- Versatility in Part Size:
- Sand casting can handle a wide range of part sizes, from small intricate components to large and heavy castings.
- It is well-suited for producing parts that are too large or impractical for other casting methods.
- Tooling Adaptability:
- Sand casting can accommodate changes in tooling requirements for different projects or production runs.
- Alterations to the pattern or mold can be made easily and quickly, allowing for flexibility in adapting to different casting needs.
- Sustainability:
- Sand casting is considered an environmentally friendly process since the sand used in molds can be recycled and reused multiple times.
- Recycling sand reduces waste generation and lowers the overall environmental impact of the casting process.
These characteristics make sand casting a versatile manufacturing method that can meet a wide range of requirements across various industries. Whether it’s for small-scale production of intricate parts or large-scale production of heavy components, sand casting offers flexibility, cost-effectiveness, and the ability to produce complex geometries efficiently.