Due to the special operating environment, rail transit trains are subject to impact and vibration during normal operation, so the traction motor structural parts that provide power for trains must have a certain mechanical strength. In order to ensure that the strength of traction motor structure meets the use requirements, the first motor shall be developed according to GB/T21563-2018 Impact and Vibration Test of Rail Transit Locomotive and Vehicle Equipment, and the whole machine shall be subject to simulated long-life test, impact test and functional test in vertical, horizontal and vertical directions. As an important supporting structure of traction motor, aluminum casting works with the outer ring of bearing to position the shaft axially, and provides a sealed operating environment for the operation of motor stator and rotor.
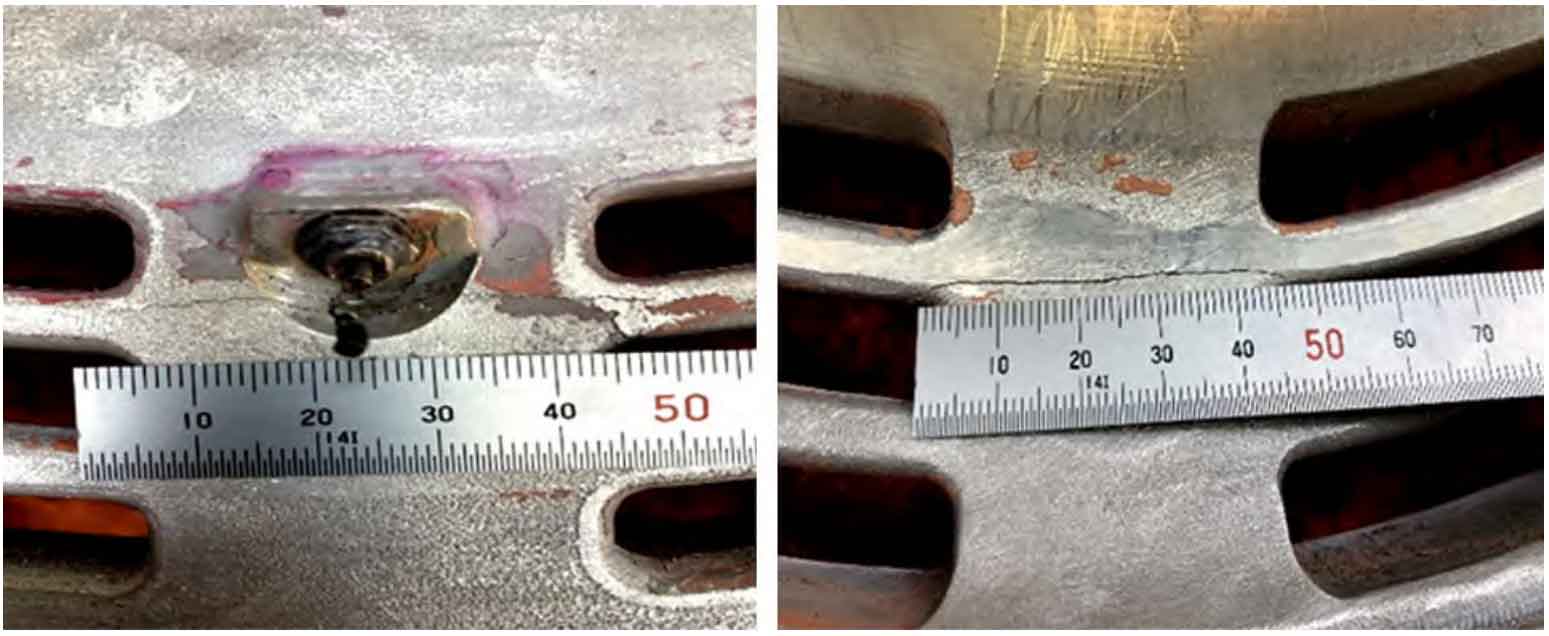
During the impact vibration test of the motor, a through crack with a length of about 46mm was found at the groove of the nozzle piston of the cast aluminum structure, as shown in the figure. The casting material is AlSi7Mg0.3 aluminum alloy, which complies with DINEN1706 standard. After low-pressure casting, it is processed by T6 to obtain finished products with good comprehensive mechanical properties. The tensile strength, yield strength, elongation and hardness of the cast aluminum structural member are 290 MPa, 210 MPa, 5% and 90 HB respectively. In this paper, the failure analysis of the cast aluminum structure was carried out, and its structure was optimized.
Through fracture analysis, the failure mechanism is determined, and corresponding structural optimization suggestions are proposed. The conclusions are as follows:
(1) Casting inclusions provide conditions for crack initiation, and high stress provides power for crack propagation.
(2) The purity of liquid aluminum and the thin thickness of the groove are the main reasons for the casting defects. During the casting process, the purity of liquid aluminum is improved and the thickness of the groove is increased to improve the casting quality.
(3) The stress concentration is formed by the right angle transition at the groove, which is the main reason for the high stress here. The structure is optimized, and the right angle transition at the groove is changed to the fillet transition. After the improvement, the stress level at the groove is obviously reduced, and the safety factor of the aluminum casting structure is improved.