Spheroidal Graphite Cast Iron is highly regarded for its mechanical properties, particularly its fatigue and wear resistance. These properties make Spheroidal Graphite Cast Iron a preferred material for a wide range of applications, especially those involving cyclic loading and high wear conditions. This article delves into the factors contributing to the fatigue and wear resistance of Spheroidal Graphite Cast Iron and explores various methods to enhance these properties.
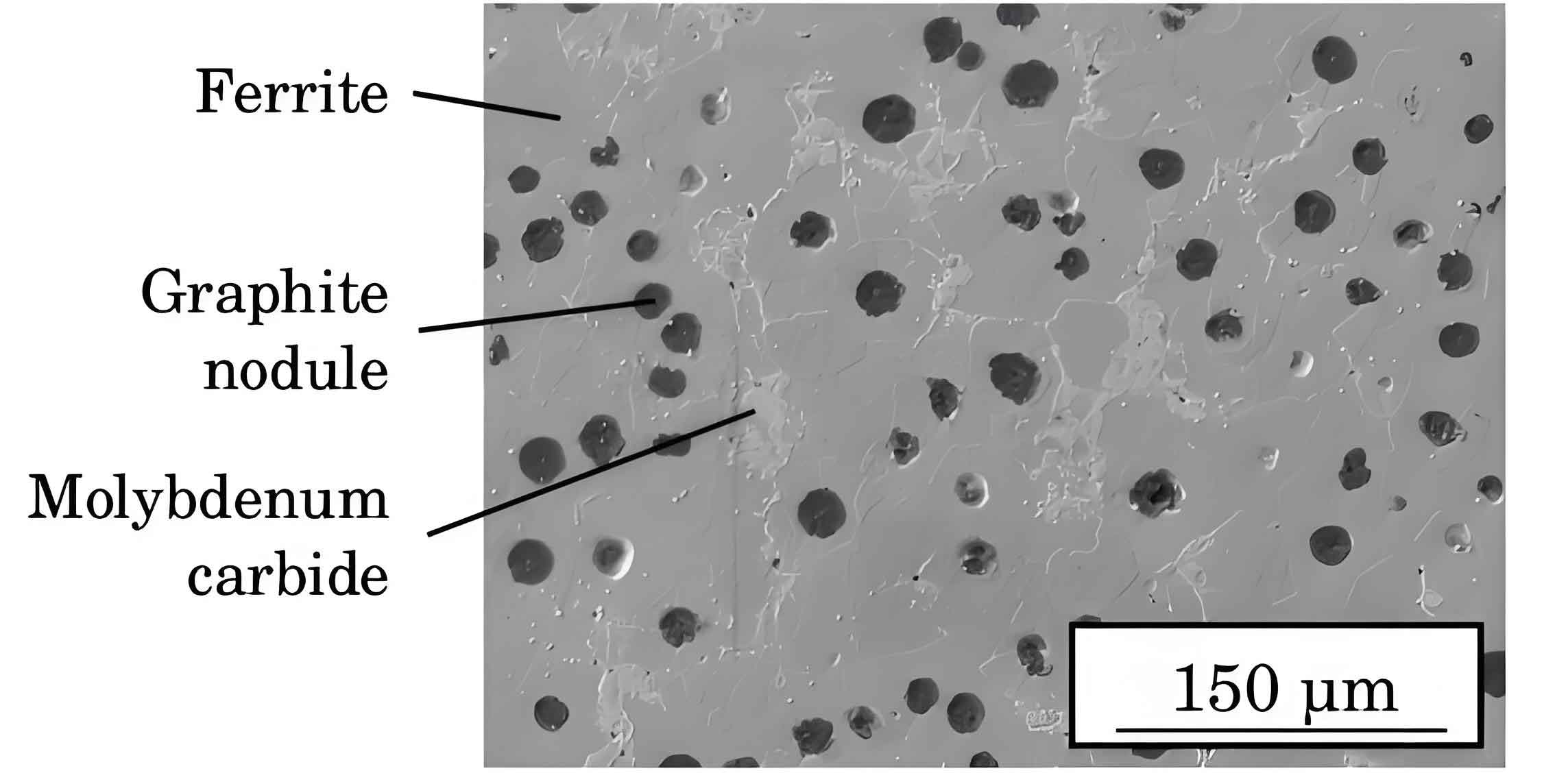
Understanding Fatigue Resistance in Spheroidal Graphite Cast Iron
Fatigue resistance refers to the material’s ability to withstand repeated loading cycles without failure. In Spheroidal Graphite Cast Iron, fatigue resistance is crucial for components subjected to cyclic stresses, such as automotive parts and industrial machinery.
Factors Affecting Fatigue Resistance
- Microstructure: The presence of spherical graphite nodules reduces stress concentration points, enhancing fatigue resistance.
- Matrix Structure: A fine-grained pearlitic or bainitic matrix improves fatigue strength.
- Heat Treatment: Processes like annealing, normalizing, and austempering refine the microstructure, improving fatigue resistance.
- Surface Quality: Smooth surface finishes reduce the initiation sites for fatigue cracks.
Table 1: Factors Affecting Fatigue Resistance
Factor | Description |
---|---|
Microstructure | Spherical graphite nodules reduce stress concentrations |
Matrix Structure | Fine-grained pearlitic or bainitic matrix enhances strength |
Heat Treatment | Refining microstructure through various processes |
Surface Quality | Smooth finishes reduce fatigue crack initiation |
Enhancing Fatigue Resistance
To enhance the fatigue resistance of Spheroidal Graphite Cast Iron, several techniques can be employed:
- Optimized Alloying: Adding elements like copper and nickel to improve toughness and fatigue strength.
- Heat Treatment: Applying processes like austempering to achieve a bainitic structure.
- Surface Treatments: Techniques like shot peening to introduce compressive stresses and improve surface quality.
List 1: Techniques to Enhance Fatigue Resistance
- Optimized alloying with copper and nickel.
- Heat treatment such as austempering.
- Surface treatments like shot peening.
Understanding Wear Resistance in Spheroidal Graphite Cast Iron
Wear resistance refers to the material’s ability to resist surface degradation due to mechanical action. In Spheroidal Graphite Cast Iron, wear resistance is vital for components in contact with other surfaces, such as gears, bearings, and engine parts.
Factors Affecting Wear Resistance
- Microstructure: The distribution and morphology of graphite nodules affect wear resistance.
- Hardness: Higher hardness levels typically improve wear resistance.
- Heat Treatment: Processes like quenching and tempering increase hardness and wear resistance.
- Alloying Elements: Adding elements like chromium and molybdenum enhances wear resistance.
Table 2: Factors Affecting Wear Resistance
Factor | Description |
---|---|
Microstructure | Distribution and morphology of graphite nodules |
Hardness | Higher hardness levels improve wear resistance |
Heat Treatment | Increases hardness and wear resistance |
Alloying Elements | Chromium and molybdenum enhance wear resistance |
Enhancing Wear Resistance
Enhancing the wear resistance of Spheroidal Graphite Cast Iron can be achieved through various methods:
- Alloying: Adding elements like chromium and molybdenum to form hard carbides.
- Heat Treatment: Applying quenching and tempering to increase surface hardness.
- Surface Coatings: Using coatings such as nitriding or PVD to improve surface wear resistance.
List 2: Techniques to Enhance Wear Resistance
- Alloying with chromium and molybdenum.
- Heat treatment like quenching and tempering.
- Surface coatings such as nitriding or PVD.
Heat Treatment Processes for Enhancing Fatigue and Wear Resistance
Heat treatment processes play a crucial role in enhancing both fatigue and wear resistance of Spheroidal Graphite Cast Iron. The following are key heat treatment processes and their effects:
1. Annealing
Annealing is used to soften the material, relieve internal stresses, and improve ductility. While primarily aimed at enhancing ductility, it also contributes to improved fatigue resistance by reducing residual stresses.
Benefits of Annealing
- Stress Relief: Reduces internal stresses that could initiate fatigue cracks.
- Improved Ductility: Enhances the material’s ability to absorb cyclic stresses.
2. Normalizing
Normalizing refines the grain structure and enhances the mechanical properties, including fatigue and wear resistance.
Benefits of Normalizing
- Refined Grain Structure: Improves overall strength and fatigue resistance.
- Uniform Properties: Ensures consistent mechanical properties throughout the material.
Table 3: Benefits of Normalizing
Benefit | Description |
---|---|
Refined Grain Structure | Improves strength and fatigue resistance |
Uniform Properties | Ensures consistent mechanical properties |
3. Austempering
Austempering produces a bainitic microstructure, significantly enhancing both fatigue and wear resistance.
Benefits of Austempering
- Enhanced Strength: Bainitic structure improves strength and toughness.
- Improved Wear Resistance: Bainitic microstructure offers excellent wear resistance.
4. Quenching and Tempering
Quenching and tempering increase the hardness and strength of Spheroidal Graphite Cast Iron, making it more resistant to wear and fatigue.
Benefits of Quenching and Tempering
- Increased Hardness: Higher hardness levels improve wear resistance.
- Balanced Toughness: Tempering ensures that the material remains tough and resistant to fatigue.
List 3: Benefits of Quenching and Tempering
- Increased hardness for wear resistance.
- Balanced toughness for fatigue resistance.
Applications Benefiting from Enhanced Fatigue and Wear Resistance
The enhanced fatigue and wear resistance of Spheroidal Graphite Cast Iron make it suitable for a variety of demanding applications across multiple industries.
Automotive Industry
- Engine Components: Crankshafts, camshafts, and connecting rods benefit from enhanced fatigue resistance.
- Transmission Parts: Gears and shafts require high wear resistance and fatigue strength.
Aerospace Industry
- Landing Gear: Components that undergo cyclic loading benefit from high fatigue resistance.
- Engine Parts: Turbine housings and other high-wear components require enhanced wear resistance.
Industrial Machinery
- Pumps and Valves: High wear resistance is essential for longevity in harsh environments.
- Gears and Bearings: Components subjected to constant friction benefit from improved wear resistance.
Table 4: Applications of Spheroidal Graphite Cast Iron
Industry | Applications |
---|---|
Automotive | Engine components, transmission parts |
Aerospace | Landing gear, engine parts |
Industrial Machinery | Pumps, valves, gears, bearings |
Conclusion
Spheroidal Graphite Cast Iron is highly valued for its exceptional fatigue and wear resistance, making it a versatile and reliable material for numerous demanding applications. The material’s performance in these areas is influenced by its microstructure, hardness, and the presence of specific alloying elements. Through careful control of these factors and the application of appropriate heat treatment processes, the fatigue and wear resistance of Spheroidal Graphite Cast Iron can be significantly enhanced. These enhancements ensure that components made from Spheroidal Graphite Cast Iron can withstand the rigors of cyclic loading and high-wear conditions, providing long-lasting performance and reliability. As technology advances and new techniques are developed, the potential for further improving the fatigue and wear resistance of Spheroidal Graphite Cast Iron continues to grow, expanding its applications and benefits across various industries.