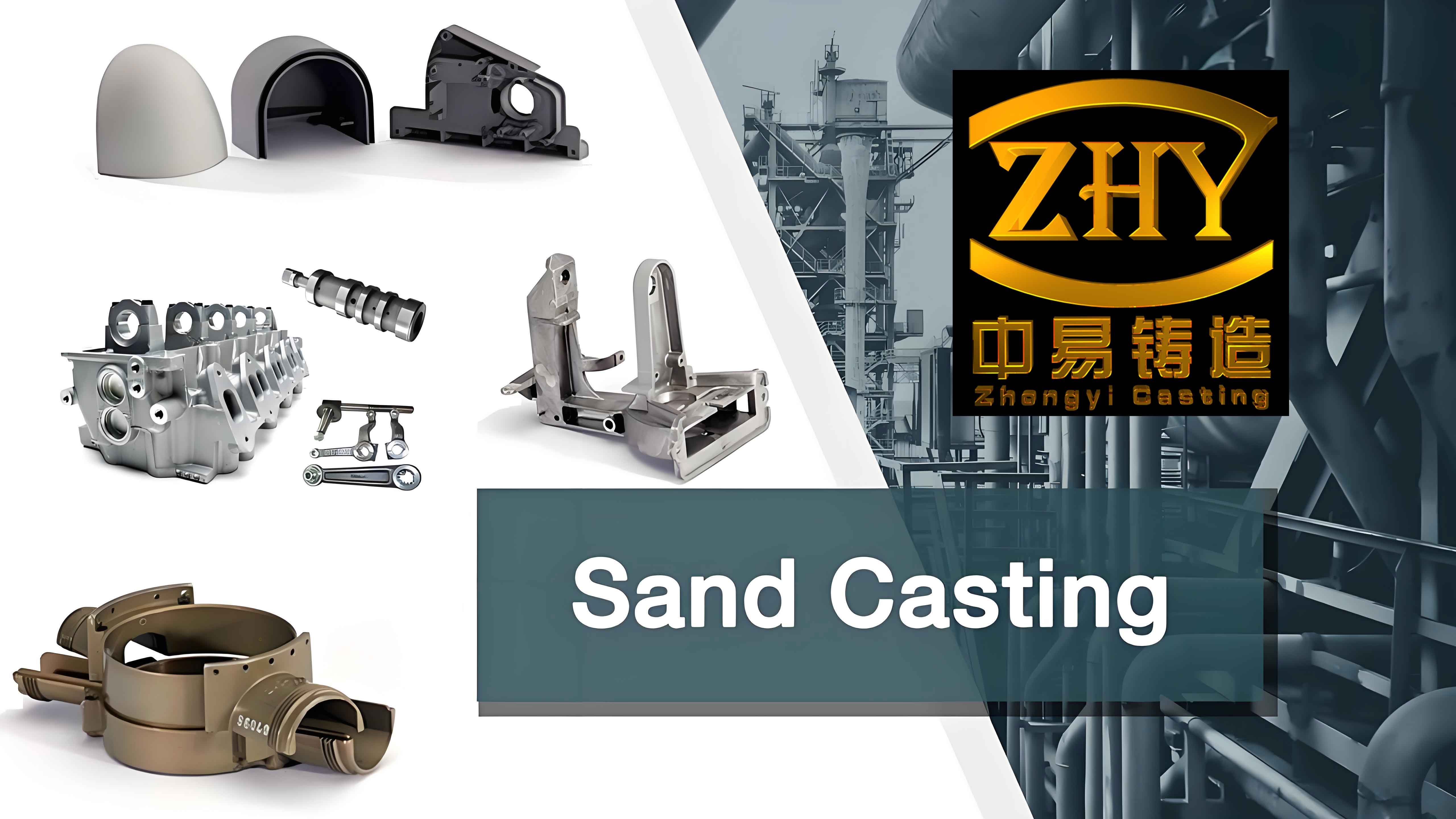
Sand casting is a widely used manufacturing process that allows for the creation of complex metal parts with intricate geometries. Despite its versatility, producing complex sand casting parts poses several challenges that can impact the quality and cost-effectiveness of the final product. This article explores these challenges and offers solutions to mitigate them, ensuring the successful production of complex sand casting parts.
Challenges in Producing Complex Sand Casting Parts
- Design Complexity
- Intricate Geometries: Complex sand casting parts often require intricate geometries that can be difficult to achieve with traditional sand casting techniques. This includes thin walls, deep pockets, and intricate internal passages.
- Tolerance Control: Maintaining tight tolerances in complex sand casting parts is challenging due to the nature of the sand mold, which can shift or deform during the casting process.
- Material Selection
- Compatibility: Not all metals are suitable for sand casting. The choice of material can affect the casting’s properties, such as its strength, durability, and resistance to wear and corrosion.
- Shrinkage: Different metals shrink at different rates as they cool. Predicting and compensating for this shrinkage is crucial to producing accurate and high-quality sand casting parts.
- Mold Design and Preparation
- Core Complexity: For parts with internal cavities or intricate internal features, the design and placement of cores can be particularly challenging.
- Sand Quality: The quality of the sand used in the mold affects the surface finish and dimensional accuracy of the sand casting parts. Poor sand quality can lead to defects such as rough surfaces, inclusions, and gas porosity.
- Casting Defects
- Porosity: Gas porosity, caused by trapped air or gases within the mold, can weaken the sand casting parts and cause them to fail under stress.
- Cold Shuts: These occur when two streams of molten metal meet but do not fuse properly, resulting in a weak seam within the sand casting parts.
- Shrinkage Defects: As the metal cools and solidifies, it shrinks. If the shrinkage is not properly managed, it can lead to cracks or voids within the sand casting parts.
Solutions for Producing Complex Sand Casting Parts
- Advanced Design Techniques
- Computer-Aided Design (CAD): Utilizing CAD software allows for precise design of complex sand casting parts, ensuring that all geometrical features and tolerances are accurately represented.
- Simulation Software: Casting simulation software can predict potential issues such as shrinkage, porosity, and cold shuts, allowing for design adjustments before the actual casting process begins.
- Material Considerations
- Alloy Selection: Choosing the right alloy for the specific application can help mitigate issues related to shrinkage and compatibility. For example, using alloys with lower shrinkage rates can improve dimensional accuracy.
- Material Testing: Conducting thorough material testing can ensure that the selected material meets the required mechanical properties and performance criteria.
- Improved Mold and Core Design
- Core Boxes and Patterns: Utilizing precision-machined core boxes and patterns can enhance the accuracy of the cores, reducing the likelihood of defects in the sand casting parts.
- Binder Systems: Advanced binder systems can improve the strength and stability of the sand mold, reducing the risk of deformation and defects.
- Quality Control Measures
- Non-Destructive Testing (NDT): Techniques such as X-ray inspection, ultrasonic testing, and magnetic particle inspection can detect internal defects in the sand casting parts without damaging them.
- Process Monitoring: Implementing real-time process monitoring can help identify and address issues during the casting process, ensuring consistent quality of the sand casting parts.
Tables and Lists for Clarity
Table 1: Common Casting Defects and Their Causes
Defect Type | Description | Common Causes |
---|---|---|
Porosity | Small holes or voids within the casting | Trapped air, gases in mold |
Cold Shuts | Weak seams where molten metal streams do not fuse | Improper pouring temperature |
Shrinkage Cracks | Cracks due to metal shrinkage as it cools | Poor mold design, inadequate risers |
Inclusions | Foreign material embedded in the casting | Contaminated sand or molten metal |
Table 2: Solutions for Enhancing Sand Casting Quality
Solution | Description |
---|---|
CAD Design | Precision design of complex geometries |
Simulation Software | Predicts potential issues before casting |
Alloy Selection | Chooses materials with favorable properties |
Precision Core Boxes | Ensures accurate core formation |
Advanced Binder Systems | Improves mold stability and strength |
Non-Destructive Testing (NDT) | Detects internal defects without damaging the casting |
Process Monitoring | Real-time monitoring to maintain consistent quality |
List: Steps for Successful Production of Complex Sand Casting Parts
- Design Phase
- Utilize CAD and simulation software for accurate design.
- Conduct material testing to ensure compatibility and performance.
- Mold Preparation
- Use high-quality sand and advanced binder systems.
- Design precise core boxes and patterns.
- Casting Process
- Monitor the process in real-time to detect and address issues.
- Implement quality control measures such as NDT.
- Post-Casting Operations
- Inspect sand casting parts for defects using NDT techniques.
- Perform necessary finishing operations to meet specifications.
Conclusion
Producing complex sand casting parts involves navigating various challenges related to design complexity, material selection, mold preparation, and defect management. By leveraging advanced design techniques, selecting appropriate materials, improving mold and core design, and implementing stringent quality control measures, manufacturers can overcome these challenges and produce high-quality, complex sand casting parts. The combination of technological advancements and meticulous planning is key to achieving success in the sand casting process, ensuring that the final products meet the desired specifications and performance standards.